「AMRって最近よく聞くけど、正直AGVと何が違うの?」
本記事は、そんなモヤモヤを抱えたまま、なんとなく調べ始めた方にこそ読んでほしい内容です。
AMR(自律走行搬送ロボット)とAGVの違いを正しく理解しないまま導入を進めると、無駄な投資や現場トラブルの原因になりかねません。
一方で、ポイントを押さえて導入すれば、人手不足解消・生産性向上・安全性アップなど、現場が劇的に変わる可能性もあります。
この記事では、AMRの基本からAGVとの違い、導入メリット、費用、安全性まで初心者にもわかりやすく解説。
「なんとなく知ってる」を「的確に判断できる」レベルへ引き上げる5分間を、今ここで始めましょう。
なぜ今、AMRが注目されているのか?背景と導入が進む理由
近年、製造業や物流業界を取り巻く環境は急速に変化しています。少子高齢化による労働力の確保難、物流の「2024年問題」による働き方改革への対応、そして人件費の上昇といった課題が重なり、現場では効率化と省人化が強く求められています。
これまでの固定型自動化設備では対応が難しかった多様なニーズに、柔軟に応える手段として脚光を浴びているのがAMR(自律移動型搬送ロボット)です。
加えて、AMRを支えるソフトウェア技術の進化も見逃せません。ナビゲーション精度の向上、AIによる最適ルート選定、導入インターフェースの簡素化などにより、初期導入のハードルは着実に低下しています。
特に、頻繁にレイアウトが変更される工場や、限られたスペースを効率的に使いたい倉庫などで、AMRの柔軟性とスケーラビリティが高く評価されています。AMRは単なるロボットではなく、時代の要請に応じた現場改革のキーソリューションとして注目されています。
AMRの基本から、AGVや協働ロボットとの違い、導入メリット、選び方までを網羅的に知りたい方は、こちらのガイドをご覧ください。初心者から導入検討中の方まで役立つ情報をまとめています。
AGVとはどう違う?AMRとの違いと使い分けの判断ポイント
AGVとAMRの機能比較一覧表|搬送方式の選定に役立つ基礎比較
導入時に混同されやすいAGV(無人搬送車)とAMR(自律移動ロボット)の違いを明確に比較した表です。目的や現場環境に応じた適切な選定の参考になります。
比較項目 | AGV(無人搬送車) | AMR(自律搬送ロボット) |
---|---|---|
移動方式 | 磁気テープやQRコードなどの固定ルート | センサー+SLAMによる自己位置推定とマップ構築 |
ルート変更 | 手動でガイドテープ貼替が必要 | ソフトウェアで自動ルート再設定が可能 |
環境適応力 | 一定環境下での繰り返し作業に適応 | レイアウト変更や障害物にも柔軟に対応可能 |
初期導入コスト | 比較的安価(100〜300万円程度) | 高め(300〜800万円程度)だが高ROIが期待可能 |
最適な利用環境 | 整備された工場ライン、単純構内搬送 | 変動の多い工場・倉庫、複雑な動線の現場など |
補足:AGVは整備された環境での定型作業に向き、AMRは柔軟な運用が求められる環境に適しています。
製造・物流・医療でどう活かす?AMR活用事例と導入効果を現場別に紹介
工場の搬送を自動化!AMRが製造現場にもたらす3つの効果
製造業では、人手による搬送作業が多くのリソースを消費しています。AMRを導入することで、工程間の部品供給や完成品の移動といった単純かつ繰り返しの作業を自動化できます。
たとえば、作業員が1日何往復も行っていた台車移動をAMRが代替すれば、作業者は組立・検査といった付加価値の高い業務に集中でき、生産性向上につながります。
さらに、薬品や高温部品など、取り扱いに注意が必要な物の搬送をAMRに任せることで、作業者の安全リスクを減らし、職場の環境改善にも貢献します。
倉庫業務の効率を劇的に改善!物流現場におけるAMRの使い方
ECや小売業界では、多品種・少量出荷が常態化しており、倉庫業務に求められる柔軟性も高まっています。AMRは、「棚を人に運ぶ」棚搬送型のほか、ピッキングリストに応じてスタッフを最短距離でサポートする巡回型など、多様な運用スタイルに対応可能です。
作業者の移動距離が大幅に削減されることで、作業時間の短縮や人的ミスの低減にも寄与します。変化の激しい物流現場において、AMRは拡張性の高い即戦力です。
なお、倉庫でのピッキング作業をAMRで自動化した最新事例については、こちらの記事で詳しく解説しています。
病院・ホテルでも活躍!非製造業でのAMR導入事例と効果
AMRは、製造・物流業界にとどまらず、医療・サービス分野でも導入が進んでいます。たとえば、病院では検体や医薬品を各部門へ搬送したり、病棟間の物資を定時配送したりする用途に活用されています。
ホテル業界でも、ルームサービスを客室まで自動で届けるAMRが稼働しており、非接触ニーズが高まる中で、衛生面や顧客体験の向上に貢献しています。人手を補完するツールとして、施設運営の効率化と省人化の両立を実現する存在です。
AMR導入による現場の変化比較|人手作業と自動搬送の違い
AMR導入前後で何がどう変わるのかを「ビフォー・アフター」で比較。定量的な効果イメージを把握できます。
比較項目 | 導入前(人手作業) | 導入後(AMR) |
---|---|---|
作業内容 | 作業員が台車を押して搬送 | ロボットが自律走行で自動搬送 |
稼働時間 | 長時間作業・シフト制が必要 | 24時間稼働が可能、休憩なし |
安全性 | 衝突・転倒・誤配送リスクがある | 障害物回避・停止機構付きで安全性が向上 |
移動距離 | 作業者の移動距離が多く体力的負担も大 | 最短ルート走行により移動距離・時間を削減 |
トラッキング | 作業履歴は人依存で記録されにくい | センサーによる自動ログ記録で可視化が容易 |
補足:導入効果を定量的に社内説明する際や、ROI計算時の前提データとしても活用できます。
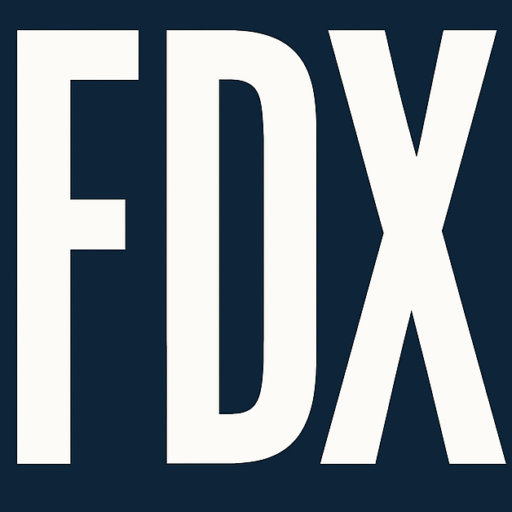
Factory DX
運営事務局
「『今のやり方で大きな問題はない』——それが最大のリスクかもしれません。
AMRはどうやって動く?自律走行を支える仕組みと主要テクノロジー3選
SLAM×センサーで実現する自己位置推定と地図構築
AMRの自律走行を支える中核技術が「SLAM(Simultaneous Localization and Mapping)」です。これは、LiDAR(レーザーセンサー)やカメラから取得した情報をもとに、自身の現在位置を把握しながら周囲の地図を同時に作成する仕組みです。これにより、事前のルート設定が不要となり、リアルタイムに変化する環境にも即座に対応可能になります。
障害物回避と動的ルート選択のメカニズム
AMRは走行中も常にセンサーを通じて環境情報を取得し、自分の周囲にある障害物や人の動きに応じて動作を変更します。仮に通路が一時的にふさがっていても、別ルートを自律的に計算し、目的地まで安全に到達する機能を備えています。これにより、人が介入せずとも高い安全性と効率性を両立できます。
AIによる経路最適化と複数台の協調搬送
複数のAMRが同時に稼働する環境では、AIアルゴリズムがそれぞれの目的地、バッテリー残量、通行量などを加味して最適な経路を自動的に判断します。これにより、衝突リスクを避けつつ、搬送効率を最大化する「フリートマネジメント」も実現可能になります。
AMRのナビゲーション技術の仕組み図解|自律移動を支える主要技術の構造
AMRの自律走行は複数のセンサーとAI処理によって成立しています。以下はその代表的な構成を示した図解です。
フェーズ | 主な構成要素 | 機能概要 |
---|---|---|
センサー入力 | LiDAR・カメラ・IMU | 周囲の障害物・人・壁などの情報をリアルタイム収集 |
自己位置推定 | SLAMアルゴリズム | 地図を同時に生成しながら自己位置を特定 |
経路判断 | AIアルゴリズム(最短経路計算) | 障害物や混雑状況を考慮した経路の自動最適化 |
行動制御 | モーター制御+障害回避ロジック | 減速・停止・回避などリアルタイムな運行制御 |
補足:SLAMを中心としたナビゲーション構成は、従来のAGVに比べて「判断力」「適応力」に優れているのが特徴です。
AMR導入で何が変わる?現場にもたらすメリットと具体的効果
人手不足、搬送作業の負担、現場のレイアウト変更対応など、製造業や物流業界が抱える課題は年々複雑化しています。こうした中、AMR(自律移動ロボット)の導入によって現場にどのような変化が生まれるのか。
ここでは、AMRがもたらす具体的なメリットや改善効果について、実際の運用イメージを交えながらわかりやすく解説します。
AMRのメリット・デメリットをより詳しく比較した記事はこちら。AMR導入前に必ず知っておきたい内容をまとめています。
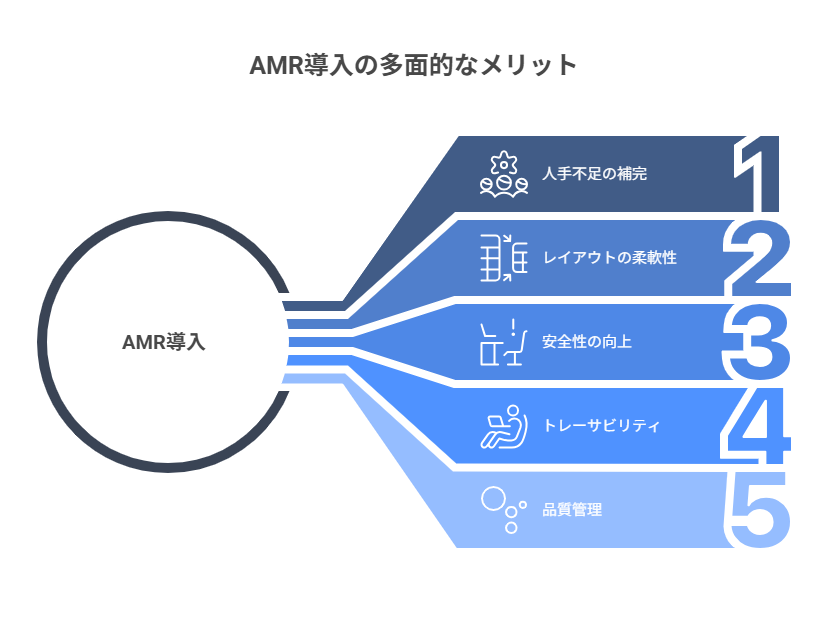
人手不足を補完し、業務の効率を向上
AMRは、人手が必要だった単純な搬送作業を自動化し、スタッフをより付加価値の高い業務に集中させることができます。これにより、作業の分業が進み、生産性の底上げにつながります。
レイアウト変更や多品種少量生産にも柔軟に対応
固定ルートが不要なAMRは、レイアウト変更や工程の再設計にも柔軟に対応できるのが特長です。マップを再構築するだけで運用を再開できるため、将来的な変化にも強い搬送体制を構築できます。
安全性・トレーサビリティ・品質管理を強化
人手による搬送と比べて接触事故や誤配送リスクが低く、安全性が向上します。さらに、センサーによる走行ログや搬送履歴の記録により、トレーサビリティの確保や品質保証の面でも有効に機能します。
このように、AMRは単なるロボットではなく「自律型の搬送プラットフォーム」として、現場全体の効率化・品質向上に寄与するテクノロジーです。構造を理解することで、導入判断の精度と社内説明力も大きく高まります。
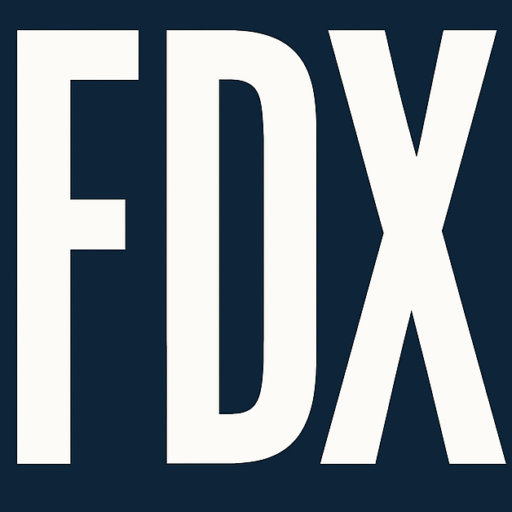
Factory DX
運営事務局
ロボットに任せられる仕事は、ロボットに。人は“考える作業”に集中する──それが今の現場に必要な分業のかたちです。
失敗しないAMR導入のために確認すべき5つの重要ポイント
AMRは非常に有効な自動化ツールですが、導入すれば必ず成功するわけではありません。現場との相性、システム連携、運用体制など、事前に見極めるべきポイントを押さえておかないと、思わぬトラブルや投資対効果の低下を招く可能性があります。
このセクションでは、AMR導入で失敗しないために、成功へと導くために最低限確認しておきたい5つの重要なチェックポイントを整理して解説します。
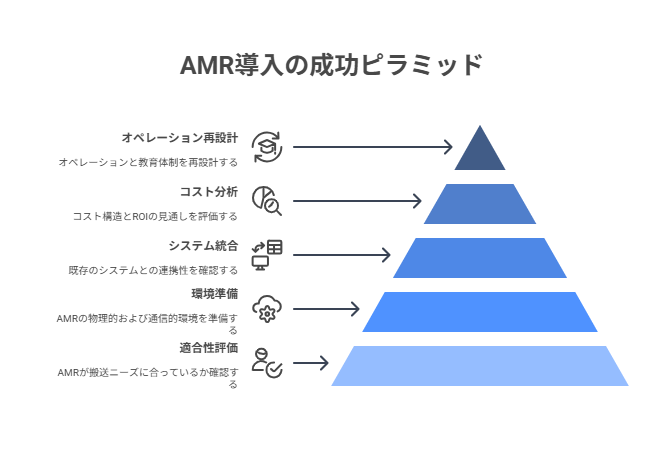
1. 自社の搬送業務とAMRの適合性を見極める
まず着目すべきは、AMRが自社の搬送ニーズに本当に合っているかどうかです。日々の搬送回数、運ぶ物の重量・サイズ、通行ルートの長さや複雑さなどを細かく洗い出し、どの工程をAMRに置き換えるのが効果的かを可視化します。特に、人手がかかる単純作業や、ルート変更が頻繁なエリアはAMRの得意領域です。
2. 稼働環境の整備状況を事前にチェック
AMRの性能を最大限発揮させるには、物理的・通信的な環境の準備が欠かせません。床の段差や傾斜がAMRの走行に支障をきたさないか、通路幅は機種の最小回転半径を確保できているかを確認しましょう。また、安定したWi-Fiや5Gの通信インフラも、遠隔制御やマップ更新に不可欠です。
3. WMSやMESなどの既存システムとの連携性
AMRは単体で動くだけでなく、WMS(倉庫管理システム)やMES(製造実行システム)との連携により、搬送指示や在庫情報とリアルタイムに連動します。自社が導入している業務システムと互換性があるか、APIや連携ツールの対応状況を事前にベンダーに確認することが重要です。
4. コスト構造とROIの見通しを立てる
AMRのコストはハード本体だけではありません。ナビゲーションソフト、保守契約、初期設定費用、社員向けトレーニングなど、トータルでの費用感を把握した上で、想定される業務削減効果と比較してROIを試算します。数値で効果を可視化することが、社内稟議や経営判断の後押しにもなります。
5. 現場オペレーションと教育体制の再設計
AMRの導入は、単にロボットを導入するというよりも、業務フローそのものを見直す契機です。誰がAMRに指示を出すのか、トラブル発生時にどう対応するのかなど、具体的な運用体制を構築する必要があります。また、現場スタッフへの操作研修・トラブル対応教育は、導入効果を安定して継続させるための不可欠な投資です。
よくあるAMR導入失敗の原因と、それを避けるためのチェックポイントをまとめました。
実際の現場で起こった失敗事例をもとに、再現性の高い対策を解説しています。
事前に知っておくだけで、無駄なコストや手戻りを防げます。
→ 失敗事例から学ぶ防止策付き資料を無料ダウンロード
導入前に知っておきたい!AMRでよくある誤解と現場での注意点
「導入すれば全自動で稼働する」は誤解
AMRはあくまで搬送工程の一部を自動化するツールであり、荷物の積み下ろしや棚入れといった周辺作業は別途設計が必要です。
たとえば、ピッキングや出荷工程が人手のままでは、AMRの効率性が限定的になってしまいます。業務全体の流れを見直し、AMRを中心とした業務設計を行うことが、真の業務改善につながります。
地図作成とルート設計は導入前の要
AMRは現場の地図データをもとに走行ルートを決定します。そのため、初期段階での3Dマップ作成や停止位置の定義は非常に重要です。
狭い通路や障害物の多いエリアでは、事前の地図設計次第で稼働効率が大きく左右されます。ベンダーとの連携を密にしながら、現場に即した最適なマップを構築する必要があります。
テスト運用で「現場特有のリスク」を洗い出す
AMRはセンサーで環境を認識して動きますが、実際の現場では反射素材による誤認識や、日差し・照明の変化、通信遮断などが思わぬトラブルを引き起こす可能性があります。
特にWi-Fiの弱いエリアでは、AMRが一時停止したり、ルート修正ができなくなるケースもあります。本格導入前にテスト走行を実施し、現場環境に潜むリスクを可視化・対策しておくことが安定運用の鍵です。
AMR導入ステップと比較検討の進め方をわかりやすく解説
3ステップで進めるAMR導入の全体フロー
AMRの導入は、一度にすべてを完了するのではなく、段階的な検証と展開が成功の鍵を握ります。以下の3ステップに沿って進めることで、失敗リスクを抑えながら、現場に最適な形で定着させることが可能です。
AMR導入プロセスの3ステップ|失敗しないための進行フロー
AMR導入は一気に進めるのではなく、段階的に評価・展開するのが最適です。以下はその標準ステップをまとめたものです。
ステップ | 内容概要 | 主な確認・実施項目 |
---|---|---|
初期検討 | 現場課題の洗い出しと要件整理 | 搬送対象・距離・頻度・導線構成・既存システムとの連携性 |
実証導入(PoC) | 限定エリア・少数台でテスト導入 | 走行精度・障害回避・作業者との協調性の確認 |
本格展開 | 導入効果を踏まえた最適化+台数スケールアップ | 導入範囲の拡大、教育・保守体制の整備 |
補足:PoC(概念実証)で現場適合性を検証することで、本格展開の失敗リスクを大幅に低減できます。
ベンダー選定は「機能+体制+将来性」で比較
AMRベンダー選びは、機能スペックだけでなく、長期的な運用を見据えた評価が重要です。ナビゲーション方式(SLAM、マーカー型など)、積載重量・サイズの適合性、導入後のサポート内容、ソフトウェアアップデートの頻度などを総合的に比較しましょう。導入後のトラブル対応力も重視すべきポイントです。
複数社からの相見積もりを取得することで、価格の妥当性やサポート体制の差も明確になります。
AMR導入前に必ず確認すべき10のチェックポイント
導入前に確認すべき実務チェック項目を表形式で整理しました。社内検討・ベンダー打合せ時の指標にも有効です。
チェック項目 | 確認内容のポイント |
---|---|
搬送物の重量・形状 | AMRの積載許容量・サイズ対応範囲と合致しているか |
移動距離 | 長距離/短距離でバッテリー容量や走行時間が足りるか |
通路幅 | 最小通過幅を確保できているか、交差点・旋回余裕の有無 |
通信環境 | Wi-Fi/5Gの通信強度が安定しているか |
地図作成支援 | ベンダーが現場マッピングやルート設計をサポートするか |
システム連携 | WMSやMESなどとの接続インターフェースがあるか |
稼働時間 | バッテリーの持続時間と運用シフトの相性 |
導入コスト | 初期費用+保守費用含めた総額の見積もりが取れているか |
安全性機能 | 停止ボタン・障害物センサー・認証機構が装備されているか |
教育・運用体制 | 操作研修・障害時マニュアル・社内リーダー育成体制があるか |
補足:この表は、導入の可否だけでなく「どこに不安要素があるか」を明確化するためにも活用できます。
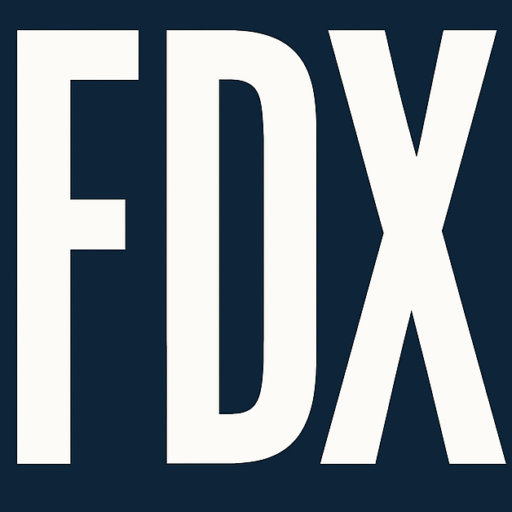
Factory DX
運営事務局
「“とりあえず導入してみる”では、絶対に失敗します。現場に合わないAMRは、ただの重くて高い箱です。
AMRの進化はどこへ向かう?拡張性と連携で広がる可能性
AIとの連携で実現するリアルタイム最適化
今後のAMRは、単に「動くロボット」から「考えて最適化する搬送システム」へと進化していきます。走行中のセンサー情報や稼働履歴をAIが蓄積・分析することで、通路の混雑状況に応じたルート変更、バッテリー消費を抑える走行制御、メンテナンスの予兆検知などが可能になります。これにより、現場の変化に即応する柔軟なオペレーションが実現します。
複数台の連携によるフリートマネジメントの高度化
1台ずつのAMR運用から、複数台が協調して稼働するフリートマネジメントの時代へ移行が進んでいます。中央の統合管理システムが、各AMRに最適な指示をリアルタイムで出し、搬送対象やタイミングに応じて役割を自動で振り分ける仕組みです。これにより、ボトルネックの回避や搬送効率の最大化が実現し、大規模施設でも安定した無人搬送体制が構築できます。
ロボットアームや自動棚との統合ソリューションへ
AMRは今や単独での導入にとどまらず、ロボットアームや自動倉庫システムとの連携により、ピッキング・仕分け・棚入れまで一貫して自動化する「トータル搬送ソリューション」へと進化しています。たとえば、AMRが目的地まで移動し、その場でロボットアームがピッキングを行うといった連携により、人的介在を最小限に抑えたスマート物流が現実化しています。
AMR選びに迷ったら?比較と情報収集で失敗しない導入判断を
目的や現場に合ったAMRを見極めるために
AMRと一口に言っても、その性能や対応範囲はメーカー・モデルによって大きく異なります。搬送物の種類、環境の広さ、通路の形状、導線の複雑さなど、現場の条件に合致するかを見極めるには、ユースケース別の情報収集が欠かせません。
「人手搬送のどこを、どのように自動化したいか」という導入目的を明確にした上で、具体的な成功事例や導入効果を比較することが、判断の精度を高めます。
AMRメーカー比較で失敗しないためのポイント
導入後のパフォーマンスやトラブル対応に大きな影響を及ぼすのが、ベンダー選定です。ナビゲーション方式(SLAM・マーカー型など)の精度、WMSやMESとのソフトウェア連携のしやすさ、導入支援や保守体制、トレーニング制度、そして初期・ランニングコストのバランスまで、多面的に評価する必要があります。
自社にとって「何が必須で、何が妥協できるのか」をあらかじめ整理したうえで比較検討を行いましょう。
「これだけは知っておきたい」AMR導入前のよくある質問10選
- AMRとは何の略称で、どのような意味を持ちますか?
AMRは「Autonomous Mobile Robot」の略で、日本語では「自律走行型搬送ロボット」と訳されます。環境を自ら認識し、指示された目的地まで自律的に移動できる点が特徴です。
- AGVとの違いは具体的にどこにありますか?
AGV(無人搬送車)は磁気テープやガイドによる走行が前提で、ルート変更には設備変更が伴います。一方、AMRは地図情報とセンサーを活用し、柔軟にルートを判断・変更可能です。
- 中小規模の工場や倉庫でもAMRを活用できますか?
はい。近年のAMRは設計・導入のハードルが下がっており、スモールスタートに対応したモデルも多く、中小企業でも実用可能です。
- AMR導入にはどの程度のコストがかかりますか?
導入費用は数百万円規模が一般的ですが、人的工数の削減や搬送ミスの防止といった面で、投資対効果(ROI)は比較的早期に見込めます。
- AMRはどのような業務に適していますか?
主に倉庫内や工場内での部材・製品の搬送業務に適しており、繰り返し頻度の高い作業ほど導入効果が高くなります。
- AMRは人と同じ空間で運用しても安全性に問題はありませんか?
安全性を確保するため、LiDARやカメラ等の障害物検知センサーが搭載されており、歩行者との協働環境にも対応可能です。
- 運用中に搬送ルートを変更したい場合、どのような対応が必要ですか?
AGVと異なり、AMRはソフトウェア上で地図やルートの調整が可能なため、物理的な工事を伴わず迅速に変更できます。
- AMRの導入により現場の人員配置にはどのような影響がありますか?
単純な搬送作業をAMRが担うことで、人員はより高度な判断を要する業務に専念でき、生産性の向上が期待されます。
- AMRの運用にはインターネットやWi-Fi環境が必須ですか?
多くのAMRはクラウドまたはローカルネットワークによる運用が前提ですが、基本動作をオフラインで対応可能な機種も存在します。
- AMRは一過性のブームではなく、今後も導入が進むと考えて良いでしょうか?
はい。労働人口の減少や製造現場の自動化ニーズの高まりを背景に、AMRの需要は今後も着実に拡大していくと見込まれます。
まとめ|AMRは現場変革を支える次世代の搬送ソリューション
AMR(自律移動型搬送ロボット)は、固定ルートに頼らない柔軟な走行と、環境変化に即応できる自律性を備えた次世代の搬送ツールです。人手不足の深刻化、物流効率の向上、安全性の確保といった多面的な課題に対し、現場レベルでの実効性の高い解決策を提供します。
ただし、その導入には業務との適合性確認、稼働環境の整備、社内オペレーションの設計など、入念な準備が欠かせません。安易に導入するのではなく、自社の課題と目的に合致するかどうかを見極めることが成功の鍵です。
まずは、AMRにできること・できないことを正しく理解し、現場に合った機種やベンダーを比較検討するところから始めましょう。将来の業務革新に向けた第一歩として、情報収集と意思決定の質を高めることが、最適なAMR導入への近道です。
最適なAMRを選ぶには、運用目的と現場環境に合った比較が不可欠です。
導入前に押さえるべきチェックポイントをわかりやすくまとめました。
後悔しない選定のために、今この資料を確認しておきましょう。
→ 選定チェックリスト付き資料を無料ダウンロード