出荷量は増えるのに、人手は減る──
そんな現場のプレッシャーを、毎日のように感じていませんか?
「熟練者が辞めた」「新人教育に時間がかかる」「ピッキングミスで返品が増えた」……
その課題、実はAMR(自律走行搬送ロボット)で大きく改善できるかもしれません。
いま注目されているのが、AMRを活用した倉庫ピッキング・仕分け作業の自動化です。
歩行距離の大幅削減、作業の標準化、誤ピックの防止など、すでに導入効果が出ている事例も多くみられるようになりました。
導入済みの企業では、“人が足りなくても出荷が止まらない仕組み”を築きつつあり、人手依存の現場との差が、繁忙期の対応力や教育コストで徐々に表れています。
この記事では、AMRによる自動化の実際の効果や活用のヒントを、図解とともに実務目線でわかりやすく整理しています。
「うちの規模でも使えるのか?」「どこから手を付けるべきか?」
その疑問の答えを、ここで見つけてください。今読まずにあとで追いつくのは、難しくなっていきます。
AMRによる倉庫ピッキング自動化の最新動向
近年、物流業界で急速に注目を集めているのが「AMR(自律走行搬送ロボット)」による倉庫ピッキング作業の自動化です。人手不足、出荷量の増加、多品種少量化といった課題に対し、AMRは柔軟で効率的な解決策として期待されています。
本稿では、AMRの基本概念から、従来のピッキングカートとの違い、主要メーカーのソリューションまでを体系的に解説し、導入検討中の企業にとって実用的かつ納得感のある情報を提供します。
AMRとは何か?物流現場を変える自律走行ロボットを解説
AMRとは「Autonomous Mobile Robot」の略で、自己位置推定(SLAM技術など)を活用し、人や障害物を回避しながら自律的に移動するロボットのことを指します。従来のAGV(無人搬送車)が磁気テープなどの固定経路に依存していたのに対し、AMRは柔軟にルートを変更できるため、レイアウト変更や混雑時の対応が可能です。
物流現場では、棚から商品を取り出す「ピッキング」作業をAMRがサポートすることで、作業員の移動距離を大幅に削減。ピッキング効率の改善と人的負担の軽減の両立が可能になります。
以下は、AGVとAMRの違いを簡潔に比較した表です。
項目 | AGV | AMR |
---|---|---|
移動方法 | 磁気テープ・QRコード等 | 自己位置推定+センサー制御 |
経路の柔軟性 | 固定された経路 | ダイナミックに変更可能 |
障害物回避 | 不可(停止のみ) | 可能(障害物を避けて進行) |
レイアウト対応 | 困難(再設計が必要) | 柔軟に対応(即時反映可能) |
この表が示す通り、AMRは現場の変化に即応できる柔軟性が強みです。新商品の増加や在庫配置の最適化にも追従できる点で、成長志向の物流拠点に最適な技術といえるでしょう。
なお、AMRとAGVの違いを初心者向けに整理した解説記事もありますので、基礎から学びたい方はこちらをご参照ください。
ピッキングアシストロボットとピッキングカートの違いと役割
ピッキング作業を効率化するための手段として、従来は「ピッキングカート」が一般的でした。これは作業員がカートを押しながらリストに従って商品をピックアップする方式です。
一方で、AMRを活用した「ピッキングアシストロボット」は、作業員の移動を最小限に抑える設計になっており、以下のような違いがあります。
- ピッキングカート:作業員が移動の主体で、効率は人の熟練度に依存
- ピッキングアシストロボット:ロボットが指示された場所に自律移動し、作業員はその場でピッキングに専念可能
とくに多品種少量出荷の現場では、アシストロボットによって作業者1人あたりの処理能力が1.5〜2倍に向上する事例も報告されており、人的コストと処理速度の両面で大きな差別化要因となります。
寺岡精工など主要メーカーが提供するソリューションの特徴
AMRを活用したピッキングソリューションは、複数のメーカーから提供されていますが、なかでも注目されているのが寺岡精工の「Delious Pick」や「自動搬送ソリューション」です。
寺岡精工の特徴は、単にAMRを導入するだけでなく、WMS(倉庫管理システム)や電子棚札(ESL)などとのシームレスな連携を重視している点です。これにより以下のような統合的メリットが実現されます。
- ピッキング指示の自動化と誤出荷防止
- 作業履歴のトレーサビリティ確保
- デジタルピッキングとAMRの連携による全体最適化
また、現場視察や初期設定支援、レイアウト設計支援といった伴走型の導入支援体制も整っており、中小〜大規模倉庫まで柔軟に対応可能です。
AMRの導入は単なる設備投資にとどまらず、「作業プロセスの再設計」と「デジタル連携による生産性革新」を同時に実現する取り組みでもあります。自社の現場においても、単なる効率化を超えた競争力強化の手段として検討する価値があるでしょう。
なお、製造業におけるAMRの活用事例については、こちらの記事でも詳しく紹介しています。
倉庫ピッキング・仕分け作業におけるAMRの活用メリット
物流現場では、出荷量の変動や人手不足といった課題が深刻化しています。とくに「ピッキング」や「仕分け」といった作業は、作業者の熟練度や体力に依存する部分が多く、人的コストの最適化が難しい領域とされてきました。こうした課題に対し、AMR(自律走行搬送ロボット)は現場の業務構造そのものを変えるソリューションとして注目を集めています。
以下では、ピッキング作業の精度とスピード向上、作業者の負担軽減、さらには運搬作業の自動化範囲について、具体的な実用効果とともに解説します。
ピッキング精度・効率の向上と作業時間短縮の効果
AMRが最も貢献する領域の一つが、「作業者の移動の最適化」によるピッキング精度とスピードの向上です。従来は作業者がピッキングリストを手に、棚を巡回しながら必要な商品を手作業で取り出していました。しかしAMRを活用することで、この「歩行・検索」のプロセスが劇的に削減されます。
たとえば、ピッキングアシスト型AMRでは、ロボットが最適ルートで棚間を移動し、作業者はその場で商品をピックするだけという状態が実現します。
【AMR導入によるピッキング工程の変化】
従来:
作業者が1人で棚を巡回 → 商品をピック → カートに格納 → 次の棚へ移動
AMR導入後:
AMRが棚間を自律走行 → 作業者は定位置で待機 → 商品到着後にピック → AMRが次の棚へ移動
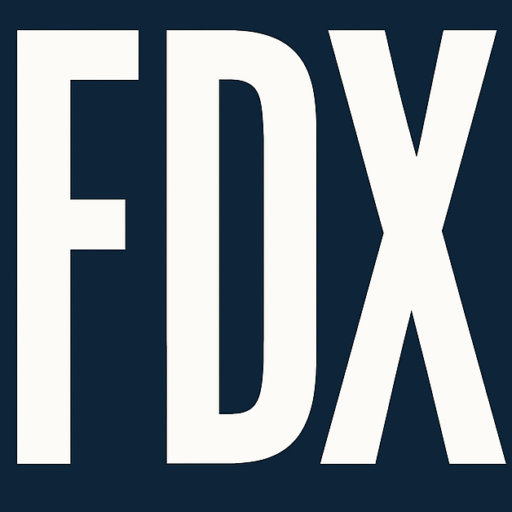
Factory DX
運営事務局
このように、「人が歩く距離をゼロに近づける」ことができ、1時間あたりのピッキング件数は最大1.5〜2倍に向上することもあります。
また、誤ピックを防止するために、LEDやディスプレイ連携によるピッキングナビゲーション機能が実装されているケースも多く、精度面でも優れた成果が期待できます。
作業者の負担軽減と省人化を実現する方法
物流現場では、特に繁忙期になると長時間にわたる立ち作業や重量物の搬送など、作業者の身体的負荷が問題となります。AMRの導入は単なる効率化だけでなく、作業者の健康面や働きやすさを守るという観点からも重要な役割を果たします。
実際に多くのAMRには「高さ調整機能付きカート」や「音声指示」「表示ガイド」など、作業者の姿勢や動作負荷を最小限に抑える工夫が盛り込まれています。また、同時に複数のAMRが稼働することにより、1人の作業者が複数のロボットと連携しながら作業を進める「協働型モデル」も実現でき、省人化にもつながります。
特筆すべきは、AMRは単に人手を減らすのではなく、「作業者の生産性を高める」ための支援ツールであるという点です。定型業務をロボットが担い、人は検品や品質管理などの判断業務に集中する──これが持続可能な省人化のカギとなります。
AMR導入による搬送・運搬業務の自動化範囲
AMRの活用はピッキング作業にとどまりません。たとえば以下のような搬送・仕分け業務にも応用されています。
- 商品ピック後の仕分けゾーンへの自動搬送
- 梱包エリアや出荷ステーションまでの最短ルート搬送
- 空コンテナや梱包資材の補充運搬
- 搬送完了後の自動戻り運転
これらをAMRが担うことで、作業動線が最適化され、人の手をほとんど介さない「ハンズフリーオペレーション」が実現します。
現場によっては、AI画像認識やRFIDと連携することで、AMRがバーコード読み取りや棚番照合などの簡易検品まで行うケースもあり、今後はさらに「判断機能を持つロボット」への進化が期待されます。
なお、AMR導入時に想定される現場課題やその乗り越え方については、こちらの記事で実例をもとに詳しく解説しています。
以上が、AMRが倉庫のピッキング・仕分け作業にもたらす具体的メリットです。導入は一朝一夕ではありませんが、従来の人中心のオペレーションでは成し得なかった「作業品質の標準化」「人的ミスの削減」「作業者の生産性最大化」が、AMRの導入によって現実的な選択肢となりつつあります。
物流業界で注目されるデジタルピッキング&自動倉庫との連携
物流業界は、EC市場の拡大と人手不足の深刻化により、ピッキング業務の効率化が喫緊の課題となっています。従来の「人が歩いて探す」作業から、「モノが人の元に届く」新しいオペレーションへの転換が加速するなか、デジタルピッキングシステムとGTP(Goods To Person)方式、そして自動倉庫との連携が注目を集めています。
このセクションでは、それぞれの方式の違い、導入の目的、連携による具体的な業務改善の仕組みを解説しながら、AMRやWMSとの統合活用によって実現する次世代物流の姿を具体的に紹介します。
GTP(Goods To Person)方式とデジタルピッキングシステムの比較
物流倉庫におけるピッキング業務は、従来「Person To Goods(作業者が棚へ向かう)」という形式が主流でした。しかし、これでは作業者の歩行距離が長く、誤ピックのリスクも高くなります。これに対し、GTP(Goods To Person)方式は、必要な商品を自動倉庫や搬送ロボットが作業者のもとまで運ぶ手法で、近年の自動化ニーズにマッチしています。
一方、デジタルピッキングシステムは、「作業者は動くが、指示が視覚で提示される」ことでピッキングの精度を高める仕組みです。どちらも精度・効率化を追求した仕組みですが、導入目的と適用規模が異なります。
以下に、両者の違いをわかりやすく示した表を挿入します。
特徴項目 | GTP(Goods To Person) | デジタルピッキング |
---|---|---|
商品の移動 | ロボットまたは自動倉庫が商品を搬送 | 商品は固定、作業者が移動 |
作業者の役割 | 定位置でピッキング | 倉庫内を移動してピッキング |
作業精度支援 | システム側で棚の提示、誤ピック防止 | ライト・画面・音声などで誤ピック防止 |
適用範囲 | 中〜大規模倉庫向け、自動化重視 | 中小倉庫・省人化重視 |
この表が示すように、GTPは自動倉庫との連携を前提とした高効率モデルであるのに対し、デジタルピッキングは既存倉庫にも柔軟に導入できる省人化アプローチです。現場の規模や目指す運用レベルに応じて、最適な方式を選定することが重要です。
WMSや既存システム連携による現場改善事例
GTPやデジタルピッキングは単体で導入するだけでは真価を発揮しません。WMS(倉庫管理システム)やMES(製造実行システム)とのデータ連携があって初めて、在庫精度の維持やピッキング履歴のトレーサビリティ、さらには棚補充計画の自動化までが可能になります。
たとえば、寺岡精工が提供するピッキングアシストカートは、電子棚札とWMSと連携し、指示された商品をリアルタイムでピック&チェックできる仕組みです。出荷指示情報をAMRに連携させることで、在庫移動から出荷前工程までを一貫して自動化する事例も増えています。
ある物流事業者では、WMSとAMR、デジタルピッキングシステムを統合的に運用することで、以下のような改善が報告されています。
- ピッキングエラー率の70%削減
- 作業時間の30%短縮
- 教育期間の大幅短縮(新人でも1日で戦力化)
これらの事例は、単なるロボット導入ではなく「情報と現場の連携」がカギであることを物語っています。物流DXを推進する上では、業務プロセスとITインフラの両輪で最適化を図る必要があります。
“連携”の次フェーズ──動的ピッキングゾーン切替の仕組み
ここまでGTP・デジタルピッキング・WMSとの連携による効率化事例を紹介しましたが、実は「さらに高度な最適化」を図る動きが、先進現場では始まっています。それが、動的ピッキングゾーンの切り替えという考え方です。
これは、出荷波動・SKU配置・作業員スキル・混雑状況などをリアルタイムで分析し、時間帯ごとにピッキングゾーンの運用ルールを再定義する仕組みです。
たとえば以下のような動的運用が可能になります。
時間帯 | 主なオーダー傾向 | ピッキングゾーン設定例 |
---|---|---|
午前中 | BtoC・単品出荷中心 | 低SKU・高回転エリアをGTP集約 |
昼過ぎ | BtoB・多品種混載増加 | 手動ゾーンに経験者を配置し精度優先 |
夜間 | 自動補充・返品処理 | 無人AMRによる棚間巡回と補充搬送へ移行 |
この動的ゾーニングは、AMRやWMSのログ分析、ヒートマップ、スキャン傾向などの“場内リアルデータ”に基づいて構成されるのが特徴です。従来の固定レイアウトではなく、データに応じて「場内の運用設計自体を変化させる」ため、作業効率と柔軟性を高次元で両立できます。
このような手法は、WMS+GTP+AMRの“トリプル連携”を導入した現場でないと実現できず、導入企業同士でもそのノウハウは共有されていないのが現状です。
つまり、動的ピッキングゾーンの概念は、今後数年で物流の自動化設計の「差」を決定づける分岐点となる可能性があります。
AMR導入時によくある見落としポイントを具体例付きで解説しています。
「知らなかった」では済まされない失敗を回避するための要点をまとめました。
後悔しない導入を目指すなら、今この資料をチェックしておくべきです。
→ 失敗回避ガイドブックを無料ダウンロード
AMRによる仕分け自動化の実現事例と効果
物流現場の仕分け作業は、出荷量の波動、商品多様化、人手不足など複数の課題が重なる領域です。従来は固定ベルトコンベアや人手に頼る運用が一般的でしたが、近年、AMR(自律走行搬送ロボット)を活用した「柔軟性の高い仕分け自動化」が注目されています。
この記事では、実際の導入事例、製品バリエーション、ロケーションや荷量に応じた柔軟な運用方法を体系的に紹介し、現場視点での納得感と実行可能性を高める情報を提供します。
寺岡精工・ラピュタなどの最新導入事例を解説
国内では寺岡精工やラピュタロボティクスなどが、AMRを活用した仕分けソリューションを実運用に落とし込んでいます。
寺岡精工は、電子棚札やWMSと連携可能な「AMR型ピッキングカート」に加え、仕分け作業用のAMRラインも展開。たとえば、オルビス東日本流通センターでは、出荷商品の自動仕分けにAMRを活用し、作業時間を大幅に短縮しています。出荷先・店舗ごとにAMRが自動でエリア分けを行い、人的ミスの大幅な削減が実現しました。
一方、ラピュタロボティクスの「ラピュタAMR」は、ピッキング・搬送・仕分けを一体化した統合型AMRを提供しており、ユナイテッドアローズなど複数のアパレル物流拠点で導入されています。ハンガー商品と箱物商品の混載管理にも対応する独自アルゴリズムが評価され、多品種少量対応の現場に最適な設計となっています。
PEERやRobotシリーズなど多様な製品・機能の紹介
AMR仕分け自動化に用いられる製品群には、用途や搬送能力に応じて多彩なバリエーションが存在します。特に注目されるのが以下のシリーズです。
- 寺岡精工「PEER」:仕分けラベルと照合しながら搬送する汎用型AMR。ESLと連携し、誤仕分けをリアルタイムで防止可能。
- ラピュタロボティクス「ラピュタAMR」シリーズ:最大500kgまでの荷重に対応し、高さ調整や障害物自動回避、バッテリー自動交換など高機能を備える。
- ZMP「CarriRo」:ローコスト・小型AMRで、中小倉庫や仮設仕分け場向けにも活用可能。デジタル仕分け看板と連動し、作業者誘導にも対応。
これらは単なる搬送機器ではなく、「誰でも扱える仕分けシステム」として、作業教育の負荷を大幅に軽減する特徴を持っています。
【補足図解:代表的なAMR製品と仕分け支援機能の比較】
製品名 | 最大積載 | 特徴機能 | 適用現場 |
---|---|---|---|
PEER | 約150kg | ラベル照合・WMS連携 | アパレル・日用品 |
ラピュタAMR | 約500kg | ピッキング+仕分け統合、障害物回避 | 大規模DC・医療品 |
CarriRo | 約100kg | 自動追従、小型・簡易運用 | 小規模拠点・店舗内物流 |
この表は、現場規模や用途に応じて選定すべきAMRの参考になります。すでに導入済みのWMS・ピッキングシステムとの親和性も重要なポイントです。
波動やロケーションに応じた柔軟な運用ソリューション
仕分け業務の最大の難所は「波動」と「ロケーション変動」にあります。繁忙期の出荷量増加、突発的な人員不足、棚配置の変更などに対応するには、固定ライン型の自動化では限界があります。
AMRは、動的な棚配置やエリア設計にも柔軟に対応できるため、「一時的な増設」「夜間運用」「スポット業務」など、運用変動への強さが際立ちます。
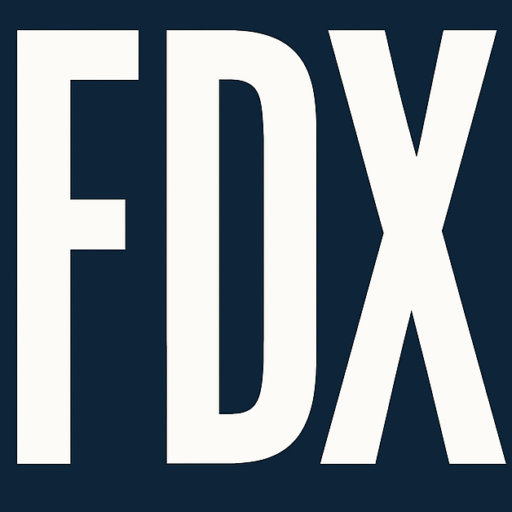
Factory DX
運営事務局
たとえば、波動期には通常稼働台数を2倍に増やし、閑散期には必要数だけ稼働させるといった運用が可能です。
また、出荷先が日替わりで変動するセンターでは、目的地情報をダイナミックに変更できるAMRが、固定ピッキングラインよりも高いROIを示すこともあります。これにより、従来は人手で調整していた仕分けルールを、システム側で自動反映させる「ノールック仕分け」も現実のものとなっています。
AMR導入企業の声と導入を検討する上での注意点
自律走行搬送ロボット(AMR)は、物流現場における人手不足や作業効率の課題に対するソリューションとして注目を集めています。しかし、導入すればすぐにすべての問題が解決するわけではなく、現場とのギャップや導入設計のミスがトラブルに発展するケースもあります。
本記事では、実際にAMRを導入した企業の声と、導入検討時に押さえておくべきポイントを整理し、自社への応用可能性を具体的に考えられる構成としました。
作業者・現場担当者の反応と人手不足への改善効果
AMR導入に対して、現場作業者が最も反応するのは「歩かなくて済むようになった」「疲労感が激減した」という点です。寺岡精工やラピュタロボティクスなどの導入企業の事例では、平均で1人あたりの歩行距離が40~60%削減されたという声が寄せられています。
また、複数のAMRが自律的に動くことによって、1人の作業者が2〜3倍のピッキング・仕分けを担当できるようになり、実質的な人員削減(省人化)につながったとの報告もあります。とくにアパレルや日用品物流において、教育が難しい繁忙期の新人でも「AMRと一緒ならすぐに仕事を覚えられる」という現場の評価が多数確認されています。
実際の導入で生じやすい課題とその改善策
導入現場で共通して挙がる課題は、以下の3つに集約されます。
- 現場レイアウトとの非整合
→ AMRが通行できない狭路や突発的な障害物で誤作動や停止が発生するケース。 - 作業者との役割分担の混乱
→ AMRに頼りすぎて、人がやるべき作業や判断の部分で手順が不明確になる事例。 - 導入後の運用定着に時間がかかる
→ 操作教育やトラブル対応に慣れるまで、実運用までに2〜3か月かかる場合も。
こうした課題に対応するためには、事前に以下のようなステップを設けることが重要です。
【AMR導入における課題と対応フロー】
課題:通行不可/誤作動/作業分担混乱
↓
対応策:
① 仮設エリアでのプレテスト実施(1〜2週間)
② 作業フローを「人+ロボット協業型」に再設計
③ マニュアル整備・教育ツールの動画化
④ 日次でのAMRログチェックとPDCA実施
このように、単に導入するだけでなく「運用の前後を設計する」ことが、AMR成功の鍵となります。実際に成功している現場では、導入前に必ず「プレ実証」と「シナリオトレーニング」を実施しています。
省人化・効率化を進める上でのAMR活用アイデア
AMRは単なる運搬ロボットではなく、現場の人材を「判断・検品・教育」といった高付加価値作業へシフトさせる装置でもあります。省人化や業務改善をさらに進めるには、以下のような活用アイデアが有効です。
これらを段階的に導入することで、AMRは単なるコスト削減装置ではなく、業務プロセスを「見える化・最適化」する経営ツールとして機能します。
見逃しがちな盲点もカバー!AMR導入前のQ&Aまとめ
- AMRを導入すると、どのくらい作業時間が短縮されますか?
現場によりますが、多くの事例でピッキング作業の歩行距離が40〜60%削減され、それに伴って1日あたりの作業時間が20〜30%短縮されるケースが報告されています。
- AMRは既存の倉庫レイアウトでも使えるのでしょうか?
はい、AMRはSLAM技術により自己位置推定と経路探索が可能なので、固定されたレイアウトでなくても対応できます。ただし、幅80cm以上の通路確保や勾配制限などの物理条件は必要です。
- ピッキング作業のミスは本当に減りますか?
減ります。AMRが正確な位置まで商品を搬送し、ピッキング指示がディスプレイやライトで明示されるため、人為的ミスを約70%削減した事例もあります。
- AMRは人手不足の解消にどれくらい貢献しますか?
1人の作業者が複数のAMRと協働することで、従来の2〜3人分の業務をこなせるようになり、パート・アルバイト採用への依存度が大幅に下がった企業もあります。
- AMRは「波動出荷」に対応できますか?
対応可能です。AMRは稼働台数の調整やエリア分散が容易なため、繁忙期には台数を増やし、閑散期には台数を減らす「スケーラブルな運用」が実現できます。柔軟性は固定ラインを凌駕します。
- AMRは作業ログを自動で記録・分析できますか?
はい、多くのAMRはクラウド連携により、「誰が・どこで・何を・どれだけ」処理したかを時系列で記録します。これにより、ボトルネック分析やKPI管理、作業者ごとの教育にも応用できます。
- AMRは夜間や無人状態でも動かせますか?
可能です。センサーとWMS連携により、深夜帯の棚補充や梱包エリアへの搬送など、無人稼働が行われている現場も存在します。人がいない時間帯に作業前準備が完了する体制が構築可能です。
- AMRの誤作動や障害時の対応はどうすればよいですか?
主要メーカーのAMRは遠隔モニタリングと自動エラーログ送信機能を備えており、障害が発生してもダウンタイムを最小限に抑える設計がされています。一部製品では自動自己復旧モードも搭載されています。
- AMRは作業者の「安全性」にどのように配慮されてますか?
AMRは人や障害物をリアルタイムで検知し、衝突回避・減速・停止機能を標準装備しています。また、音声アラートやLEDによる接近警告機能もあり、協働ロボットとしての安全基準(ISO 3691-4)に準拠した製品が多くあります。
今後の展望|AI・DX時代の倉庫ピッキングと物流自動化
物流業界は現在、AMR(自律走行搬送ロボット)を中心とした自動化の第一フェーズを経て、次なるステージ「AI・DXを組み込んだ最適化型ロジスティクス」へと進化しようとしています。単なる「作業の代替」ではなく、ピッキング工程そのものの構造を見直し、データ駆動で柔軟かつ高効率な現場運営を実現する時代が到来しています。
この記事では、ピッキング作業におけるAI・DX導入の最新動向と、実務での応用可能性、そして中長期的な業界変革の兆しについて具体的に解説します。
ピッキング工程は「人から判断を奪う」ステージへ
従来の倉庫ピッキング自動化は、「人が歩く作業を減らす」「指示を間違えないようにする」といった課題解決が中心でした。しかし今後の進化では、「ピッキング対象・順番・搬送方法」までをAIが自律的に判断し、最も効率的な順序とルートを設計・実行する仕組みが構築されつつあります。
これは、人的判断や経験に依存していた業務を、AIとWMSが統合的に制御する「プロセス標準化・最適化」の段階です。
【補足図解:倉庫ピッキングの進化フェーズ】
フェーズ1:人による手作業(紙リスト+カート)
↓
フェーズ2:デジタル化(デジタルピッキング+WMS連携)
↓
フェーズ3:AMRによる搬送自動化(作業距離の削減)
↓
フェーズ4:AI連携による順序最適化・判断自動化(DX統合)
↓
フェーズ5:自己学習型ロジスティクス(AIが改善サイクルを自律実行)
このテキストフローが示すように、物流自動化は単なる「作業の機械化」に留まらず、最終的には判断・改善・最適化を含む「知的プロセスの外部化」へとシフトしていきます。
今後の進化を牽引する3つのキーファクター
中長期的な展望:データを核とした“自己進化型物流”の時代へ
最終的にAIとDXがもたらす価値は、作業コストの削減や人手の代替だけではありません。ピッキングデータ、作業ログ、温湿度履歴、在庫移動履歴といったデータを多次元的に活用し、「物流プロセス自体を自己最適化できるシステム」への転換が進むと予測されます。
具体的には、以下のようなシナリオが現実味を帯びてきています。
- 特定商品の出荷ミスが多発 → AIが自動検知 → 配置や流れを再設計
- 季節変動に応じた搬送ルートやピッキング頻度の自動補正
- AMRが日次の実績から自己学習し、稼働率や電力使用を最適化
こうした「自己学習・自己改善」を行うAMR+WMS+AIのトライアングルが、次世代の倉庫運用の中核を担うと予測されます。
成果が出た企業は何を変え、どこに注力したのか──AMR導入前後の変化を可視化しました。
再現性のある成功要因を抽出した資料で、自社導入の参考にしてください。
同じ失敗を避け、同じ成功に近づくために、今すぐチェックを。
→ 導入準備の成功ステップ資料をダウンロード