「AMRを導入することで、搬送作業の自動化により生産性が最大40%向上し、人件費やミスの削減にもつながっています。」
これは、単なる理論ではありません。現場で日々汗を流す製造業の工場で、すでに実証されている成果です。
人手不足が深刻化するなか、搬送作業の属人化は工場全体の効率を鈍らせる要因の一つとなっています。その中で注目されているのが、「AMR(自律移動ロボット)」の導入です。
この記事では、AMRがどのように工場で活用され、どのような効果をもたらしているのかを、具体的な事例や定量データをもとに深掘りしていきます。
製造現場の責任者、工場経営者、改善担当者の皆様にとって、「自社でも活用できるのか?」「費用に見合う効果があるのか?」という疑問に、明確に答える内容をお届けします。
- なぜ今、工場でAMRの導入が進んでいるのか?
- AMR導入で何が変わる?工場が実感する具体的な改善効果を公開
- AMRはどんな工場で使われている?導入事例から活用シーンを解説
- なぜAGVでは限界があるのか?AMRとの違いを現場視点で比較
- 初めてのAMR導入でも安心!現場に必要な準備と導入プロセスを解説
- AMRのROIはどれくらい?導入判断に必要なコスト試算と回収モデル
- 導入前に必ずチェック!AMRに関するFAQと現場目線のアドバイス
- 工場の課題はこう解決される!AMR導入が加速する背景と現場適応の理由
- あなたの工場はAMR導入に向いている?判断のためのチェックリスト
- AMR導入で変わる現場の未来とは?製造業が今考えるべき次の一手
なぜ今、工場でAMRの導入が進んでいるのか?
人手不足、搬送効率の限界、DX推進──これらの課題が同時に工場を襲っています。特に、単純作業ながら人員が必要な搬送工程は、多くの工場にとってボトルネックになっています。
AMR(Autonomous Mobile Robot)は、このような搬送課題を解決するために進化してきました。従来のAGVとは異なり、AMRはセンサーとマッピング技術を駆使し、固定されたルートではなく、現場の状況を自律的に判断して最適な経路で物資を運搬します。
これにより、混在環境にも柔軟に対応し、ライン間の部品供給、組立エリアへの仕掛品移動、出荷エリアへの最終搬送など、多岐にわたる搬送工程を無人化できます。
その結果、工場内の作業効率が大幅に向上し、従業員が付加価値の高い業務に集中できるようになるのです。
AMR導入で何が変わる?工場が実感する具体的な改善効果を公開
AMRを導入すべきかどうかを判断するうえで、最も関心が高いのが「実際にどのような効果が得られるのか」という点です。
表面的なメリットではなく、数字としての改善幅、業務の変化、従業員への影響、さらには経営インパクトまでを具体的に理解することで、納得感のある判断が可能になります。
ここでは、単なるコスト削減だけでなく、業務品質や安全性、生産性、人的資源の再配置といった、AMR導入によって得られる多面的な効果を実例に基づいて解説します。
効果の本質は「削減」ではなく「変革」
AMRの導入によって得られる効果は、単に作業時間や人件費の削減にとどまりません。それ以上に重要なのは、工場全体の「働き方」が変わるということです。
たとえば、搬送作業にかかっていた4人の人員が2人で済むようになった場合、残りの2人を検査や工程管理といった他の業務に転換することで、全体のスループットや品質保証体制を強化できます。これは、目先の効率改善以上に、工場全体の生産性向上と品質安定化に貢献する取り組みとなるのです。
生産性だけでなく、安全性・定時性も向上する
人が台車を押して行う搬送作業は、物理的な負荷だけでなく、ヒューマンエラーによる事故や破損のリスクも含んでいます。AMRは経路上の障害物を検知して自動で停止・回避しながら搬送を行うため、接触事故のリスクを最小限に抑えることができます。
また、人の都合に左右されないため、「決まった時間に決まった場所へ運ぶ」といった定時搬送が可能となり、工場内のリードタイム短縮や工程の平準化にもつながります。
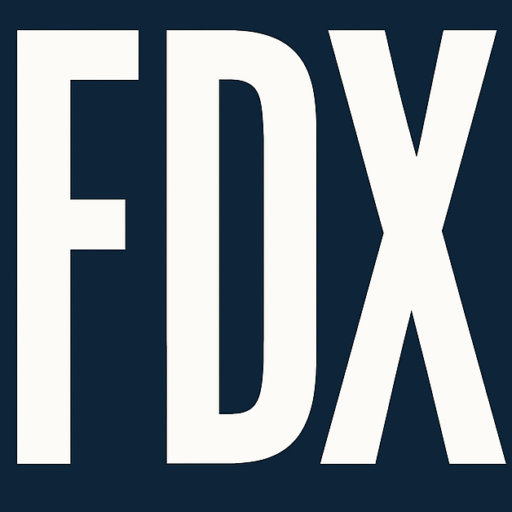
Factory DX
運営事務局
これにより、製造業全体で重視されている“ジャストインタイム”な生産体制の構築にも貢献します。
AMR導入前後での改善インパクト
以下の表では、AMR導入前と導入後の主要な業務指標を比較し、どれほどの改善が見込めるかを視覚的に示しています。特に作業時間、人員数、ミス件数、年間コストの4項目は、導入効果を測るうえで重要な指標となります。
項目 | AMR導入前(従来) | AMR導入後(自動化) | 改善率の目安 |
---|---|---|---|
搬送作業時間 | 100%(基準) | 約60〜70% | ▲30〜40% |
搬送人員数 | 4人 | 1〜2人 | ▲50% |
搬送ミス件数 | 月5〜10件 | 月1〜2件 | ▲70〜80% |
年間搬送コスト | 約800万円 | 約560万円 | ▲30% |
この表にある数値は、あくまでも平均的な参考値ではありますが、実際に導入された現場で観測された実績に基づいたものです。特に注目すべきは「搬送ミスの減少率」と「人員最適化」です。搬送ミスが減ることで、手戻りや不良品発生率が抑制され、品質の安定化にも寄与します。
現場が実感する「手応え」とは
AMRを導入した企業の現場担当者が口を揃えて言うのが、「想像していた以上に、現場のオペレーションがスムーズになった」ということです。
これは、単に作業の一部が自動化されたのではなく、「人が考えながら動く必要のない作業」がごっそり消えたことで、従業員が精神的にも肉体的にも楽になったという実感です。
加えて、「AMRが動いていることでDXが進んでいるという実感が湧く」「若手社員の定着率が上がった」という声もあります。これは、単なる省力化ではなく、職場環境そのものの改善につながっていることを示しています。
「想像していた以上に、現場のオペレーションがスムーズになった」「若手社員の定着率が上がった」という声は、まさに実践現場の声といえます。さらに、より多様な成功パターンを知りたい方は、以下の記事もご覧ください。現場ごとの工夫や成果が一覧化され、導入検討に具体性が加わります。
数値効果を最大化する運用設計も重要
同じAMRを導入しても、効果が大きく出る工場とそうでない工場があるのは、運用設計と導線設計に差があるためです。特に重要なのは以下の3点です。
- 搬送対象を明確に絞る(全部門一斉導入は非効率)
- 最短ルートと混在環境の安全性を設計段階で考慮する
- タスク管理システムとの連携によって人との協調性を担保する
これらを踏まえることで、AMR導入の効果を単なる「機器導入」に留めず、「業務改革」へと昇華させることができます。
運用設計では、導入すべき対象・最短ルートの設計・他システムとの連携などに加え、「現場に合わないAMRタイプを避ける」ことも重要です。
そのための実践的なポイントは、以下の記事で詳しくまとめていますので、併せてご覧ください。
AMRはどんな工場で使われている?導入事例から活用シーンを解説
AMRは特定の業界だけに限定されず、多くの製造業種で導入が進んでいます。以下は、代表的な業種とその活用パターンをまとめたマッピングです。
工場別AMR活用マッピング|業種ごとの活用パターン
AMRがどのような工場で、どんな目的で活用されているのかを業種ごとに整理しました。自社との類似性を探しやすくなっています。
工場業種 | 主なAMR活用領域 | 備考・特徴 |
---|---|---|
電子部品工場 | 部材供給、仕掛品搬送 | 精密搬送が求められる工程に適用 |
自動車部品工場 | 重量物搬送、ライン間連携 | 長距離搬送に強み |
食品・化粧品工場 | 衛生区域間の無人搬送 | 異物混入リスクの低減に貢献 |
医療機器工場 | 組立部品のライン供給 | スペース制限がある現場にも対応 |
このように、業界や工場規模を問わず、搬送業務を抱える工場ならAMR導入の余地があります。
電子部品工場部品供給の自動化
電子部品工場では、組立ラインへの部材供給が日々の業務の中で大きな工数を占めています。作業者が台車で部品を運び、都度補充していくスタイルでは、人手が不足するたびにラインが止まり、生産効率に悪影響を及ぼします。
AMRを導入することで、この部材供給を全自動化。たとえば、複数の製品ラインに対し、センサーで部品残量を検知し、自動で搬送を行う体制を構築できます。
結果として、部品供給ミスが大幅に減少し、ライン停止のリスクも低減。作業員は運搬作業から解放され、検査や組立といった付加価値業務に集中できるようになります。
自動車工場大型部材のピッキング搬送
自動車工場では、重量部品や中距離搬送の頻度が高く、人的ミスや事故リスクも大きな課題となってきました。特に構内の広大なレイアウトでは、手作業の搬送に限界がありました。
AMRは地図データに基づき、最短ルートを自動探索しながら、大型部品のピッキングや納品を安全かつ正確に行います。障害物があれば回避し、混在する作業員とも共存できるため、現場の安全性が向上します。
この自律性と柔軟性により、工程全体のスループットが改善され、生産性の向上に大きく寄与しています。
食品・化粧品工場異物混入リスクを抑えた搬送
食品や化粧品工場では、衛生区域を跨ぐ搬送には高い基準の管理が求められます。人が行き来する場合、毛髪や微粒子の混入リスクを完全にゼロにするのは困難です。
ここでAMRを導入すると、クローズド構造の搬送ボックスやUV殺菌処理を組み合わせることで、衛生区域を跨ぐ無人搬送が可能になります。
また、深夜帯や休日にも稼働できるため、24時間の安定供給体制を構築することができます。これにより、製造リズムが一定になり、不良率の低減にもつながります。
製造業だけでなく、物流倉庫におけるAMR活用の成功事例も注目されています。倉庫でのピッキング作業を自動化した最新事例についてはこちらをご覧ください。
なぜAGVでは限界があるのか?AMRとの違いを現場視点で比較
多くの工場では、すでにAGV(無人搬送車)を導入して一定の成果を上げているケースもあります。そのため、「AMRを導入する必要があるのか?」「AGVのままで十分ではないか?」という疑問を持つのは自然なことです。
しかし結論から言えば、AMRはAGVとは本質的に異なるアーキテクチャと運用思想を持っており、両者は単なる後継機というよりも「まったく別の機能を果たすロボット」であると捉えるべきです。
AMRの利点は、単に新しい技術であるという点ではなく、「変化に強い運用設計が可能になること」、そして「製造現場の人的負担と不確実性を大きく減らせること」にあります。
AGVは「決められたことを繰り返す装置」、AMRは「現場に応じて判断するロボット」
AGVは、磁気テープや誘導線など物理的な経路を必要とするため、工場のレイアウトや搬送動線が固定されているケースには適しています。しかし、柔軟性に乏しく、障害物や急な経路変更に対応できないため、レイアウトの変更やライン増設時には再設定・再配線が必要となります。
一方、AMRは内蔵されたセンサーとマップ学習機能を活用して、自律的に最適なルートを選択・走行することが可能です。現場に突然現れた作業員や障害物を自動で検知・回避することで、より安全かつダウンタイムの少ない搬送が実現できます。
この違いは、搬送の質と継続性に直結します。
AMRとAGVを比較する視点は「短期運用」ではなく「長期適応性」
導入初期の比較においては、AGVの方が初期コストが抑えられる場合もあります。経路設計が単純で、フル自動化までは求めていない工場であれば、AGVでも一定の成果が出せるでしょう。
しかし、現場の課題は日々変化します。搬送対象のサイズ変更、新ラインの追加、工程レイアウトの変更、異常時対応の強化など、多くの要素に即応できるかどうかが中長期的な成功のカギになります。
AMRはこの「運用継続性」や「スケーラビリティ」の点で大きく優れています。
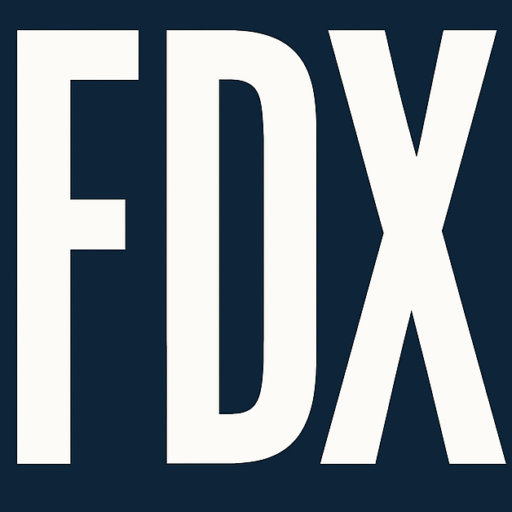
Factory DX
運営事務局
つまり、将来的な拡張や自動化レベルの向上を視野に入れている工場にとっては、はじめからAMRを選定する方が戦略的に有利だということです。
安全性と協働性の観点でもAMRは次世代仕様
従来のAGVは、作業員との動線が被らないようゾーンを完全に分ける必要がありました。つまり、AGVが走行するエリアには人が入らないように制限をかけるという考え方です。これにより、安全性は担保できる一方で、レイアウト制約が多く、現場の柔軟性は失われてしまいます。
一方、AMRは作業者との共存を前提に設計されており、LiDARや3Dカメラなどによる障害物検知機能を持ち、接触前に自動停止・回避が可能です。この「共存性」は、特に人とロボットが混在する作業環境では極めて重要な要素となります。
AGVとAMRの比較表|選定の根拠を視覚的に整理
以下は、AGVとAMRを機能・柔軟性・運用面で比較した表です。
比較項目 | AGV(従来型) | AMR(自律型ロボット) |
---|---|---|
移動方式 | 磁気テープやガイド必要 | 自律走行(センサー・地図) |
経路変更の柔軟性 | 低い | 高い |
導入コスト | やや安価 | 中程度 |
現場の適応性 | 限定的(定型環境) | 高(複雑レイアウト対応) |
作業者との共存性 | 基本不可 | 可(人感知・停止対応あり) |
このように、AMRは現代の製造現場が求める「変化への適応力」「人との協調性」「運用継続性」において、圧倒的な優位性を持っています。
AGVからAMRへの“置き換え”ではなく“進化”
AMRの登場は、単にAGVをアップグレードしたというレベルの話ではありません。工場全体のスマート化、DX推進、人員最適配置など、より本質的な業務改革を支える「次世代の製造インフラ」としての役割を担っています。
今AGVを使っていて満足している企業であっても、数年後に自社の生産戦略や工場レイアウトが変化したとき、既存のAGVシステムが柔軟に対応できるかどうかを見越して、AMRへの転換を考える企業が急増しています。
その動きは、決して一時的なブームではなく、製造業が持続可能なオペレーションを築いていくための“必然”として、今後さらに加速していくはずです。
現場の声をもとに作成した「AMR導入で後悔しないための10のチェック項目」。
導入前にチェックするだけで、リスクが大幅に軽減されます。
慎重な判断が求められる今だからこそ、活用してください。
→ チェックリスト付き失敗防止マニュアルを無料ダウンロード
初めてのAMR導入でも安心!現場に必要な準備と導入プロセスを解説
AMRの導入に興味を持ち始めた段階で、最も多く挙がる悩みが「何から着手すれば良いのかわからない」という声です。多機能で柔軟なAMRだからこそ、導入にあたっては目的の明確化や現場分析、ステークホルダーの合意形成など、計画的なアプローチが不可欠です。
ここでは、AMR導入を成功に導くために必要な準備項目と、進め方のポイントを整理して解説します。
準備不足による導入失敗を防ぐ
よくある失敗パターンとして、「なんとなく最新技術だから」「競合が入れているから」という理由だけで導入を決め、結果として現場に馴染まずに運用停止してしまうケースがあります。
こうした事態を防ぐためには、「なぜ導入するのか」「どの工程をどう変えたいのか」を明確にし、それに応じた設計を行う必要があります。
搬送業務のどこにボトルネックがあり、それがどれほどのコストインパクトや品質リスクを生んでいるかを洗い出す作業は、非常に地味ではありますが、導入後の成果を左右する最重要プロセスです。
現場との対話が成否を分ける
導入を進める中で忘れてはならないのが、「AMRはあくまで現場で運用されるものである」という視点です。AMRを導入するのは経営判断であっても、日々使いこなすのは現場の作業員であり、彼らの協力なしに成功はあり得ません。
特に、以下のような点について現場とのすり合わせが必要です。
- 現在の搬送動線にどの程度の無駄や重複があるか
- 搬送対象物のサイズ、重量、優先順位
- 搬送の頻度や時間帯のピーク
- AMRが通るスペースや経路に障害物がないか
- 作業者との接触リスクをどう低減するか
こうした情報を現場のリーダーやオペレーターから引き出すことで、導入するAMRの仕様や台数、動作パターンが具体化し、PoC(概念実証)の精度が高まります。
AMR導入ステップ図|導入の全体像を理解する
以下に、AMR導入をスムーズに進めるための標準的なステップを示します。ステップごとに実施すべき作業と注意点を整理しています。
導入フェーズ | 主な内容 | ポイント |
---|---|---|
ステップ1:現状分析 | 搬送プロセスの可視化、課題の特定 | 業務棚卸と対象エリア選定が重要 |
ステップ2:PoC導入 | 小規模テスト導入 | 効果測定・現場適応性の検証 |
ステップ3:本導入 | 全体設計・レイアウト調整・AMR配備 | 人の動線との協調運用設計が鍵 |
ステップ4:運用定着 | マニュアル整備・保守体制の構築 | 内製運用と外部支援のバランスが重要 |
この流れを一貫して踏むことで、現場がAMRをスムーズに受け入れ、継続的に運用していくための土台が整います。
自社で設計できるか?それともパートナー企業に任せるか?
AMR導入においては、社内にロボティクスや自動搬送の知見がある場合は内製化も可能ですが、多くの中小工場ではそれが難しいのが現実です。
その場合、実績のあるAMRソリューション提供会社と連携し、初期設計からPoC、定着運用までを伴走してもらう体制を整えることが現実的です。
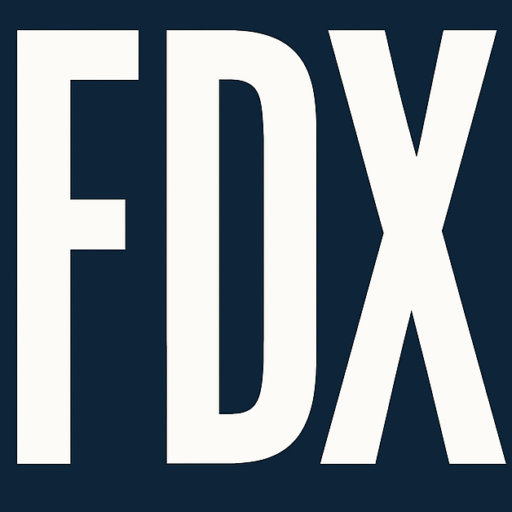
Factory DX
運営事務局
特に注意すべきは、機体を売って終わりのベンダーではなく、導入後の保守や運用改善の提案まで一貫して対応してくれるパートナーを選ぶことです。
現場への導入説明とトレーニング体制も必須
AMRは「機械的に動くロボット」ではありますが、日常的に使用するうえで現場の作業者が「どう使えばいいか」「何ができて何ができないか」を正しく理解している必要があります。
そのためには、以下のような取り組みが有効です。
- AMRの基本機能と注意点を説明する導入研修
- 操作パネルや設定画面のシンプル化
- 異常発生時の対応フローをあらかじめ共有
- トライアル期間中に現場から改善フィードバックを収集
これらの取り組みによって、現場の抵抗感を減らし、AMRを「歓迎される設備」として根付かせることができます。
導入はスタート地点であり、継続運用が成果を決める
AMR導入はゴールではなく、新たな改善サイクルの出発点です。導入によって得られた効果を可視化し、次にどの工程でAMRを活用するか、どう連携させるかという視点で継続的に改善していくことで、AMRの価値を最大化できます。
短期的なROIだけでなく、中長期的な製造プロセスの革新につなげるためには、運用チーム・改善チーム・ITチームなどとの横断的な連携体制も重要です。
このように、AMR導入の準備は単なる機器調達ではなく、工場の運用設計そのものを再構築する取り組みでもあります。そのため、段階を追って丁寧に設計・実行することが、導入成功への最短ルートとなるのです。
AMRのROIはどれくらい?導入判断に必要なコスト試算と回収モデル
AMRの導入を検討する際、最も現実的でかつ重要なポイントが「いくらかかるのか、いつ回収できるのか」というコストとROI(投資回収)に関する部分です。特に中小企業では、この点が導入の可否を分ける最大の判断材料になります。
「AMR=高額設備」という先入観を持たれている方も多いですが、実際には小規模な導入であっても数百万円程度から始められ、計画的に導入すれば数年以内に十分な投資回収が見込めます。
このセクションでは、AMR導入にかかる費用の内訳と、投資対効果の判断に必要な視点を整理し、より納得感のある判断を下すための材料を提供します。
導入費用の構成と変動要因
AMR導入時に発生する主なコストは、大きく以下の4つに分類されます。
- 機体本体の購入費(1台あたり100〜300万円程度)
- 周辺機器・通信インフラの整備費(無線LAN、ビーコン等)
- ソフトウェアライセンス・管理システム導入費
- 導入支援・設計コンサルティング・トレーニング費用
工場の規模や導入台数、連携システムの有無によって費用は前後しますが、最小構成であれば数百万円からでも導入可能です。最近では「リース契約」や「月額課金モデル」を用意するベンダーも増えており、初期負担を抑えながら試験導入を進める企業も増えています。
AMRによるコスト削減の仕組み
AMR導入によって得られるコスト削減効果の内訳は、主に以下のような項目で構成されます。
- 搬送業務に関わる人件費の削減
- 作業時間の短縮によるスループット向上
- 搬送ミスによる手戻り・不良品の低減
- 作業者の安全対策費の削減(事故・トラブル予防)
これらは単体で見ると小さな削減に見えるかもしれませんが、年単位で積み重ねると数百万円規模のインパクトになります。
投資対効果(ROI)の考え方と試算例
AMR導入の費用対効果を評価するうえで、単年度の費用回収にこだわる必要はありません。中長期的に見て、どのくらいの期間で投資額を回収できるかを見極めることが重要です。
以下に、AMR3台を導入した場合の試算例を示します。
ROI試算表|導入判断の材料となる数値提示
導入規模 | 年間コスト削減額 | 導入費用総額 | 投資回収期間(概算) |
---|---|---|---|
3台導入 | 約720万円 | 約900万円 | 約1.25年 |
この試算は、搬送業務にかかっていた作業員のうち2名分(年収360万円×2名相当)をAMRに置き換えたケースをベースにしています。ここにミス防止・夜間稼働などの付加価値を加えると、実際にはさらに短期間での回収も可能となります。
補助金・支援制度の活用で実質コストを抑える
中小企業が設備投資を行う場合、多くの自治体や国の機関が提供する補助金・助成金制度を活用することができます。例えば、以下のような制度がAMR導入に適用されるケースがあります。
- ものづくり補助金(最大1,250万円支給、補助率1/2〜2/3)
- 事業再構築補助金(業態転換時の設備支援)
- 地方自治体のDX・自動化推進支援事業
これらを活用することで、実質的な負担額を半額以下に抑えられる可能性があります。導入検討時には、補助金の申請サポートが可能なベンダーを選ぶと、申請業務の手間も大幅に軽減できます。
コストは“障害”ではなく“未来への投資”
最後に、AMR導入に関する費用を「コスト」として捉えるのではなく、「変化に対応できる工場運営体制を構築するための投資」として見ることができれば、戦略的な意思決定につながります。
特に人手不足が構造的な問題となっている今、AMRは単なる自動化機器ではなく、「人的資源を最適化し、競争力を維持するための鍵」として機能します。
短期の削減額ではなく、5年後、10年後の現場の在り方をイメージしながら、今投じるべき一歩としてAMRの導入を捉えることで、より納得感のある判断ができるはずです。
導入前に必ずチェック!AMRに関するFAQと現場目線のアドバイス
AMR導入を前向きに検討している方に向けて、特によく聞かれる質問とその答えをまとめました。
- AMRとAGVの違いは何ですか?
AMR(自律移動ロボット)はセンサーやAIにより自律的にルートを判断して移動できます。一方、AGV(無人搬送車)は磁気テープなどの決められたルートしか走れず、柔軟性に劣ります。
- どんな工場にAMRは向いていますか?
搬送作業が多く、人手不足やミス・工数過多に悩む工場に最適です。特に電子部品、医療機器、食品、自動車部品など多品種・変種の現場で活躍します。
- AMRの導入にはどのくらいの費用がかかりますか?
導入費用はAMR1台あたり300万~500万円程度が目安です。工場の規模や台数、連携設備の有無によって変動します。
- 中小企業でもAMRは導入できますか?
はい。近年では小規模現場向けの小型AMRやリース・補助金対応のソリューションも増えており、中小企業での導入も進んでいます。
- AMRの導入効果はどれくらいありますか?
搬送作業時間の30~40%短縮、人件費の20~50%削減、ミス率の大幅低減など、定量的な効果が報告されています。
- 既存のレイアウトでもAMRは導入できますか?
可能です。AMRは環境マッピング機能により複雑な動線にも対応可能で、既存レイアウトを大きく変えずに導入できます。
- 運用には専門のオペレーターが必要ですか?
基本的な操作はマニュアル化されており、専門知識がなくても現場運用が可能です。ただし、初期設定や保守面では外部支援を活用することが一般的です。
- AMRは他の機器と連携できますか?
はい。WMS(倉庫管理システム)やMES(製造実行システム)と連携することで、搬送指示の自動化やトレーサビリティの確保が可能です。
- 導入までにどれくらいの期間がかかりますか?
PoC(小規模検証)を含めて3~6か月程度が一般的です。本格導入には現場調査・設計・調整期間が必要です。
- AMRのメンテナンスはどうなっていますか?
メーカーやSIerによる定期点検・サポート体制が整っている場合が多く、リモート監視やオンサイト保守なども選べます。
工場の課題はこう解決される!AMR導入が加速する背景と現場適応の理由
近年、製造業の現場においてAMR(自律移動ロボット)の導入が急速に進んでいます。その背景には、単なる「省人化ニーズ」だけではなく、工場全体のオペレーション構造に潜む課題が深く関係しています。
このセクションでは、AMRが「なぜ今求められているのか?」という本質的な問いに対し、現場で顕在化している課題とAMRの機能がどのように結びつくのかを整理し、AMR導入の妥当性を解説します。
根本的な課題は「変化に対応できない構造」
工場の多くの課題は、「人が足りない」という単純な理由だけで起きているのではなく、「属人化」「変化耐性の低さ」「リアルタイム性の欠如」といった、構造的な問題が複雑に絡み合って発生しています。
たとえば、作業員の退職や欠勤が生産計画に直接的な影響を与えるような状態は、もはやリスク管理の範囲を超えており、恒常的な生産性の不安定化を招きます。AMRはこうした属人性の高い工程を可視化・自動化することで、業務の「人依存リスク」を低減する役割を担います。
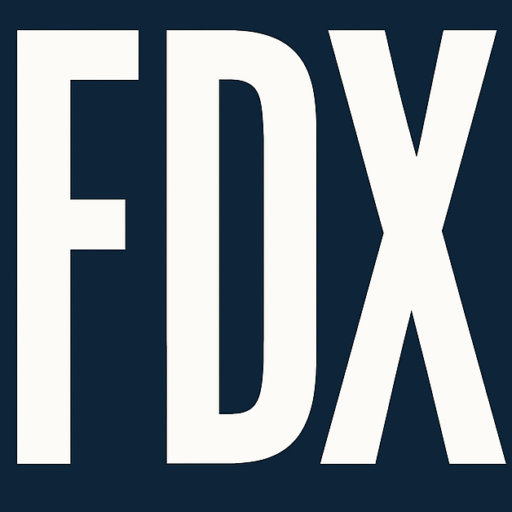
Factory DX
運営事務局
この“人に依存する構造”、あなたの現場にも心当たりありませんか?
課題をマッピングしながら導入判断を進める
AMRの導入検討は、漠然と「導入してみよう」ではなく、現場の課題を定義し、それに対する打ち手として位置づけることが重要です。下記のような形で、課題とAMRの機能をマッピングすることで、自社にとってAMRが「今必要な投資」かどうかを論理的に判断できます。
製造現場課題とAMR対応表|「うちの課題」に答える
以下の表では、実際の工場現場でよく見られる代表的な課題と、それに対してAMRがどのように対応できるかを整理しています。自社の状況と照らし合わせながら、AMRの導入価値を具体的にイメージする参考にしてください。
現場の課題 | AMRによる対応 |
---|---|
人手不足で搬送が遅れる | 無人搬送で人員負荷を軽減 |
ピーク時に作業が追いつかない | タスク自動割り当てでリアルタイム対応 |
運搬中のミスや破損が多い | 精密制御による安定搬送 |
導線が複雑で無駄が多い | 最短ルート自動探索による効率化 |
これらは一例ですが、どれか一つでも当てはまる場合、AMRが業務改善に大きな効果を発揮する可能性が高いと言えます。
数字だけでは測れない「安定性」への貢献
AMRの導入効果は、コスト削減や作業時間短縮といった数値だけにとどまりません。たとえば、「毎日決まった時間に確実に部品が供給される」ことの安心感は、現場のストレスを大きく減らし、間接的に品質や安全性を高めます。
また、AMRが業務を代替することで、従業員がより価値の高い業務(検査、品質管理、設備保全など)に時間を割けるようになり、人材の成長やモチベーションの向上にもつながります。
あなたの工場はAMR導入に向いている?判断のためのチェックリスト
実際にAMRを導入すべきかどうか迷っている方のために、現場の状況をセルフチェックできるリストを用意しました。
これは、ユーザー自身の現場課題とAMRの適合性を照らし合わせるためのツールであり、導入判断の第一歩として活用できます。
導入判断チェックリスト|読者の行動を後押し
以下のチェックリストは、AMR導入の適性をセルフチェックするための簡易ツールです。該当する項目が多いほど、AMR導入によって得られる改善効果が高いと考えられます。導入検討の第一歩として、ぜひ自社の状況と照らし合わせてみてください。
チェック項目 | 状況 |
---|---|
搬送作業が1日20回以上ある | □ |
搬送に2名以上を常時割いている | □ |
AGVでは現場レイアウトに対応しきれないと感じている | □ |
ピーク時に搬送ボトルネックが発生している | □ |
DX・スマートファクトリー化を推進していきたいと考えている | □ |
このチェック項目のうち、3つ以上に該当する場合は、AMR導入による改善効果が非常に高いと考えられます。
導入の第一歩は「課題の言語化」から始まる
チェックリストに該当する項目が多い場合でも、「まずどこから改善すべきか」が明確でなければ、導入計画が進まないこともあります。
そのためには、現在の搬送作業の実態を定量的に把握し、「どの工程をどう改善したいのか」「どれだけのコスト・人員が関与しているのか」を言語化しておくことが、最初の重要ステップです。
AMRは、決して“万能なロボット”ではありません。しかし、的確な課題設定と導入設計によって、“劇的な現場改善”を実現する力を持ったソリューションです。
自社の課題と正しく向き合うことで、AMRの導入は「難しい選択」ではなく「必然の判断」として見えてくるはずです。
AMR導入で変わる現場の未来とは?製造業が今考えるべき次の一手
AMRの導入は、単なる設備導入ではありません。それは、製造業の構造的課題に対する「変革の起点」であり、次世代の現場づくりに向けた本質的な一歩です。
人手不足、属人化、非効率な搬送動線──こうした課題に対し、AMRは自律性と柔軟性をもって解決策を提示します。単純なルーチン作業をロボットが担うことで、人間はより創造的・価値の高い業務に集中できるようになります。
それは単にコスト削減にとどまらず、「人が活きる現場」を再構築することにつながるのです。
今回ご紹介した事例や数値、導入ステップ、チェックリストを通じて、AMRの導入が特別な一部企業だけの話ではないことをご理解いただけたのではないでしょうか。むしろ今後、AMRの導入有無が「競争力の差」として顕在化していく時代がすぐそこに迫っています。
初期投資が不安でも、補助金制度やリースの活用でハードルは大きく下げられます。また、ROIも1〜2年という短期で回収可能なモデルが主流であり、中小企業こそ“今”が先手を打つチャンスです。
導入に迷っているのであれば、まずは自社の搬送工程を見つめ直すことから始めてみてください。
そして「本当にこのやり方を3年後も続けていられるのか?」と自問してみてください。その答えが明確でないなら、AMRという選択肢は必ず検討に値するはずです。
「こんなはずじゃなかった…」を防ぐための事前チェックリストをご用意しました。
AMR導入に潜むリスクと、見逃しがちな注意点を体系的に整理。
後悔する前に、導入前の今だからこそ知っておく価値があります。
→ 導入前の注意点をまとめた資料を今すぐ見る