「導入したAGVが、実はクリーンルームに適していなかった――」
このような事態が、医薬品・半導体・精密部品の製造現場で現実に起きています。クリーンルーム対応と明記されたAGVを、カタログスペックや“ISO Class 5対応”という表示だけで選定した結果、後になって発塵が発覚し、生産停止や再導入に追い込まれる――そんなリスクが、今まさにあなたの現場にも潜んでいるかもしれません。
なぜ、そのAGVは発塵したのか? なぜ、証明書があったのにトラブルは防げなかったのか?
本記事では、こうした“よくある誤解”と“見落としがちな構造リスク”を、徹底的に掘り下げて解説します。
読み進める中で、次のような確信を持てるはずです。
- 自社の清浄度環境には、どの構造のAGVが本当に適しているのか
- カタログにない“仕様の落とし穴”をどう見抜くか
- 導入前に絶対に確認すべきチェックリストとは?
読み終わるころには、AGV選定における“判断の軸”がクリアになり、再選定のリスクをゼロに近づける視点を得られるでしょう。
AGV選定は「清浄度クラス+構造仕様の整合性」が成否を分ける
クリーンルーム対応AGVの選定において、最も多い失敗は「カタログに記載された清浄度クラス」だけを見て、構造面の検証を行わずに導入を決定してしまうことです。一見すると「Class 5対応」「無発塵仕様」といった表記があるAGVでも、実際には構造上の課題によって清浄度維持が難しくなるケースが多く見られます。
とりわけ重要なのは、排気構造・可動部の密閉性・材質の選定といった、AGVの内部構造が実環境の清浄度要件と整合しているかどうかです。たとえば、清浄度Class 3〜5の環境では、側方排気や露出した駆動系があるだけで、空気中に粒子が拡散し、製造物の品質に重大な影響を及ぼすリスクがあります。
また、証明書があるからといって「すべての環境に適している」とは限りません。証明書の試験条件が実際の運用環境と異なれば、その証明は実質的な意味を持ちません。清浄度ラベルや認証はあくまで参考値であり、選定時には構造要件との照合が必須です。
クリーンルームAGVの導入において、「清浄度クラス × 構造要件」の整合性を無視すると、以下のようなリスクが連鎖的に発生します。
AGV選定ミスによるリスク連鎖
AGV選定における“構造仕様の見落とし”が、どのように現場トラブルへ波及するかをフロー図で視覚化しました。
[構造要件の見落とし]
↓
[排気や可動部からの粒子放出]
↓
[空中浮遊粒子の増加]
↓
[製品歩留まりの低下・異物混入クレーム]
↓
[再検証・再導入による時間損失とコスト増大]
構造を誤ったAGVを導入すると、単なる機械の問題では済まず、製品不良・信頼喪失・業務停滞といった「経営リスク」にまで波及します。検証は導入前に徹底すべきです。
清浄度クラスと構造仕様の適合性マトリクス
以下は、各ISO清浄度クラスにおいて求められるAGV構造の参考基準です。自社の運用環境に応じて、どのような構造的配慮が必要かを把握できます。
清浄度クラス | 推奨排気方式 | 可動部構造 | 推奨材質 | 清浄度証明の扱い |
---|---|---|---|---|
ISO Class 1 | 完全密閉+循環型 | 完全密閉・非接触式 | SUS316L | 必須 |
ISO Class 3 | HEPAフィルター付き | 密閉構造 | SUS304+研磨処理 | 強く推奨 |
ISO Class 5 | 上部排気+制御型 | シール付き | SUS304 | 推奨 |
ISO Class 7 | 通常排気可 | 標準構造 | 鋼材+塗装仕様 | 任意 |
表のとおり、清浄度が高くなるほど、AGV構造への要求も高度になります。中でも排気構造と可動部の設計は、発塵を抑える上で最も重要な項目です。
このように、AGVを「清浄度対応のスペック」で見るのではなく、「構造仕様との組み合わせで選ぶ」視点に切り替えることが、クリーンルーム運用における成功のカギを握ります。
構造仕様を軽視したまま導入を進めると、後戻りできないリスクが待っています。
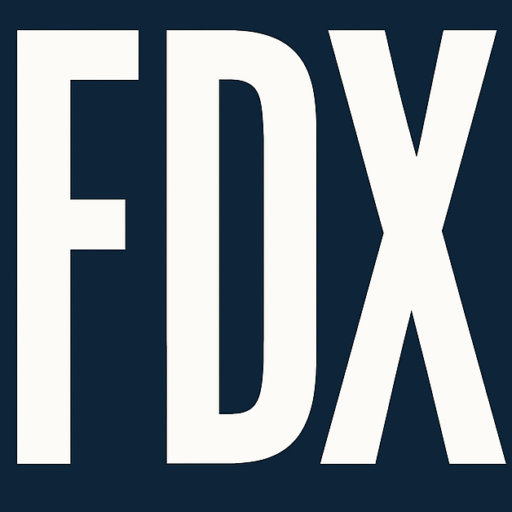
Factory DX
運営事務局
逆に、適切なAGVを初期段階で選定できれば、長期的に歩留まり改善・異物混入ゼロ・品質安定といった成果を生み出すことが可能です。
選定の初期フェーズで「清浄度クラス × 構造仕様」の整合性をしっかり見極めることこそが、現場を守り、経営判断を支える最も実用的かつ確実なステップです。
なぜクリーンルームでAGV選びが難しいのか?排気・材質・密閉性の罠
クリーンルームで使用するAGVの選定が難しい最大の理由は、AGVごとに構造仕様が異なり、見た目やカタログスペックからでは発塵リスクを正確に把握できない点にあります。
どれほど「クリーンルーム対応」をうたっていても、その実態は構造次第で大きく異なるのです。
とくにISO規格における清浄度クラスは、わずかな粒子差でも大きな差異として表れます。たとえば、ISO Class 3とClass 7では許容される粒子数が1,000倍以上の差があります。このため、「Class 3対応」と「Class 7対応」では、AGVに求められる密閉性、排気方式、構造材のレベルがまったく異なるものになります。
さらに、AGVの構成要素には、清浄度維持を難しくするリスクがいくつも潜んでいます。カタログに記載されていない内部構造や素材の仕様、さらには排気の方向や冷却機構といった要素も、発塵に直結する重要な判断材料です。
見落とされがちな発塵リスクの具体例
以下のような項目は、AGV選定の際に見逃されやすく、実際にクリーンルーム導入後に問題となることが多い部分です。
- 排気口の向きや方式(側方排気、下方排気、HEPA有無など)
- タイヤや駆動部の摩耗による微粒子発生
- 材質がSUS304かSUS316Lか、それに施された表面処理の有無
- 可動部の密閉性と使用されている潤滑剤の成分
これらは、実際の運用環境での動作確認や、専門的な知見に基づく検証によってしか判断がつかないケースもあります。見た目のスペックや販売資料だけに頼らず、実機の構造と動作を“環境目線”で評価する姿勢が必要です。
清浄度クラス別に異なるAGV構造要件
以下はISO清浄度クラスごとに求められるAGV構造の一例です。選定時には、この構造要件が満たされているかどうかを必ず確認する必要があります。
清浄度クラス | 推奨排気方式 | タイヤ仕様 | 可動部構造 | 使用材質 |
---|---|---|---|---|
ISO Class 1 | 密閉・循環型 | 無摩耗タイプ | 非接触+完全密閉 | SUS316L鏡面仕上げ |
ISO Class 3 | HEPAフィルター付き | 静電防止ゴム | シール付き密閉構造 | SUS304研磨処理 |
ISO Class 5 | 上方排気またはHEPA搭載 | 通常ゴムタイヤ | 簡易密閉構造 | SUS304 |
ISO Class 7 | 通常排気 | 通常ゴムタイヤ | 開放構造でも可 | 防錆鋼材 |
表のように、清浄度が高くなるほどAGVに求められる仕様も精密になります。Class 3以上の環境では排気の位置や密閉構造、摩耗部品の管理が重要視され、Class 1では非接触部品や特殊材質が求められる場合もあります。
AGV構造の違いによる発塵リスク
同じ「クリーン対応AGV」と言っても、その内部構造によって発塵リスクがまったく異なります。以下の図では、一般的なAGVと高清浄度対応AGVの違いを簡易的に表現しています。
項目 | 通常AGV | 高清浄度対応AGV |
---|---|---|
外装 | 鋼材パネル(塗装) | SUS304/SUS316L研磨仕様 |
排気 | 側面に向けて放出 | 上部排気+HEPAフィルター |
タイヤ | ゴム摩耗あり | 無摩耗樹脂タイプ |
可動部 | 露出したチェーン | 密閉+無潤滑構造 |
上記のように、表面材質から排気方向、内部可動部まで、構造が異なれば発塵挙動も全く変わります。
選定では「構造を見る」ことが品質トラブルを防ぐ第一歩になります。
このように、クリーンルーム対応AGVの選定では、「見えない構造こそがリスク要因」であるという認識を持ち、単なるスペックや宣伝文句に惑わされない実務的な評価が求められます。導入後のトラブルを未然に防ぐには、AGVの本質的な構造理解が不可欠です。構造の理解こそが、清浄度維持と製品品質の保証に直結するのです。
どのAGVがどの清浄度クラスに適合する?【クラス別早見表付き】
AGVの選定において、「クリーンルームで使用可能」との記載だけを根拠に導入を決定するのは非常に危険です。AGVが本当に自社の清浄度クラスに適合しているかを判断するには、「クリーンルームのクラス別要件」と「AGVの構造仕様」がどの程度一致しているかを確認する必要があります。
たとえば、ISO Class 5のクリーンルームであれば「Class 5対応」と記載されたAGVでも使えるように見えますが、排気口の配置や駆動部の構造によっては微細粒子が発生し、実際の運用環境に適さないケースもあります。逆にClass 3環境では、SUS316L材・完全密閉構造・循環排気機構など、非常に高水準のAGV構造が求められます。
また、清浄度証明書が発行されているかどうかも判断材料のひとつですが、これは「必須」「推奨」「任意」などクラスによって求められるレベルが異なるため注意が必要です。
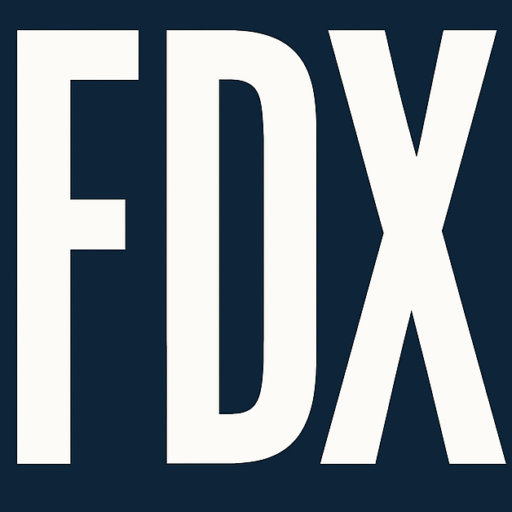
Factory DX
運営事務局
証明書があるからといって即採用できるわけではなく、その試験条件や発行機関の信頼性も見極めるべきです。
ここでは、代表的なISOクラス別に、どのようなAGV仕様が望ましいかを早見表にまとめました。導入検討の際の「比較基準」としてご活用ください。
清浄度クラス別AGV要件早見表
自社のクリーンルームがどのクラスに該当するかを前提に、下記の早見表を使って、AGVに求められる構造要件・仕様の妥当性をチェックしてください。
ISOクラス | 材質要件 | 排気方式 | 可動部の密閉性 | 清浄度認証の有無 |
---|---|---|---|---|
Class 1 | SUS316Lフルステンレス | 無排気(循環冷却) | 全方位シール構造 | 必須 |
Class 3 | SUS304+表面コーティング | HEPAフィルター付き排気 | 密閉チェーン使用 | 強く推奨 |
Class 5 | SUS304 | 排気位置・量を制御可能 | 簡易シール構造 | あれば望ましい |
Class 7 | 鋼材+防塵塗装仕様 | 通常排気 | 標準密閉 | 任意 |
この表は、AGV選定における「構造の整合性」を可視化した指標です。たとえばClass 3ではHEPAフィルター付きの排気制御や、SUS材の表面処理が不可欠になります。Class 7では、比較的柔軟な仕様が許容される一方で、発塵源が増えやすくなるため、現場運用における粒子管理が重要になります。
このように、AGVの導入は単に「清浄度対応モデル」を選ぶのではなく、「自社環境で求められる要件に本当に適合しているか」を仕様面から見極めることが重要です。AGVは一度導入すると簡単には変更できないため、事前に十分な仕様比較と現場ニーズの突き合わせを行うことで、長期的な品質安定とコスト最適化につながります。
現場に合わないAGVを選んでしまうと、高額なコストロスにつながる恐れがあります。
失敗事例から学べる「見落としがちな落とし穴と回避策」をまとめました。
導入前の今こそ、知っておくべき内容です。
→ 失敗事例から学ぶ注意点資料を今すぐ見る
失敗しないAGV選定のカギとは?清浄度・構造別に押さえるべき5つの鉄則
クリーンルーム対応AGVの導入は、単なる設備投資ではなく、製品品質や工場運用全体に直結する重要な判断です。しかし、実際には「仕様書に書かれていたから」「対応モデルと書いてあったから」といった理由で導入し、後にトラブルとなるケースが多く発生しています。
導入後のやり直しや追加コスト、ライン停止による生産影響を回避するために、選定段階で最低限チェックすべき5つの鉄則を以下にまとめました。
1. 清浄度適合証明は「発行元」と「試験条件」を確認する
AGVに清浄度適合証明が添付されていても、それが信頼できる第三者機関によるものか、また実際に自社の運用条件に即したテスト内容なのかを確認しなければなりません。条件が違えば、証明の意味を成さない場合があります。
2. 材質・コーティングは“洗浄方法”とセットで評価する
クリーンルームでは定期的に薬品洗浄が行われます。その際、塗装や表面処理が剥がれやすい材質では、使用中に発塵源となるリスクがあります。材質の耐薬品性や表面硬度も重要な評価指標です。
3. 排気・冷却方式はクリーン度への影響大
排気ファンからの吹き出しによって空中に粒子が拡散することがあります。クリーン度を保つには、上部排気・HEPAフィルター付き・内部循環冷却など、空気の流れを制御する機構が求められます。
4. 可動部の密閉性と潤滑剤の種類も確認ポイント
駆動部は、摩耗による金属粉・潤滑剤の飛散といった問題を引き起こします。密閉構造であるか、潤滑剤がクリーン対応品であるか、またその使用量・補充方式まで含めて確認しましょう。
5. メンテナンス頻度と現場導線の最適化可能性
メンテナンスの頻度が高ければ、そのたびにクリーン環境が乱れるリスクが増します。また、メンテ時にAGVを取り出すためのスペースや導線が確保できるかも重要な選定基準です。
AGV導入全体の流れを網羅的に知りたい方は、こちらの『AGV導入ステップ完全ガイド|検討・稟議・試験導入・本格展開まで失敗しない進め方』も併せてご覧ください。
クリーンルームAGV選定チェックリスト
以下のチェックリストは、選定時に見落としがちなポイントを網羅的に確認できるように設計されています。社内の設備選定基準書としても活用できます。
チェック項目 | 内容・確認方法 | 推奨アクション |
---|---|---|
清浄度適合証明の発行元と試験条件 | 第三者機関発行か/ISO粒子条件と一致するか | 証明書原本と試験概要を入手・検証 |
材質とコーティングの耐薬品性 | SUS種別/塗装の剥離耐性 | 実機洗浄試験または製造元に確認 |
排気構造と冷却方式 | 上部排気か/HEPAありか/ファン位置 | 排気口の位置・経路図を確認 |
可動部の構造と潤滑仕様 | 密閉構造か/使用油脂の種類 | 分解図と潤滑剤の仕様書を確認 |
メンテナンス性と現場対応性 | 頻度/洗浄方法/AGVの取り回しやすさ | メンテマニュアルの確認・現場ヒアリング |
このチェック表は、担当者ごとの認識のズレを防ぎ、選定基準の明確化に役立ちます。導入判断の前に関係部署(品質管理・製造・保守)のレビューを通すことで、選定リスクをさらに下げることができます。
この5項目を網羅的に確認することで、AGV導入後にありがちな「こんなはずではなかった」というトラブルを大幅に減らすことができます。
特に清浄度が厳しい環境では、1つの見落としが全体工程に大きな影響を及ぼすため、細部にわたる構造評価と実用性のチェックが不可欠です。選定段階での丁寧な確認が、運用フェーズでの“安心”と“安定”を生み出します。
なぜAGV導入で失敗するのか?現場事例に学ぶ“見落としの盲点”とは
クリーンルーム対応AGVの導入において、仕様書だけを信じて導入を進めた結果、稼働後に発塵トラブルや不適合が判明し、再選定・再導入となるケースは少なくありません。
その背景には、「適合証明がある=問題なし」という誤った思い込みや、現場条件と仕様との整合性を検証していないという実務上の落とし穴があります。
ここでは、実際の失敗事例・成功事例を紹介するとともに、初期投資と長期コストの逆転リスクについても深掘りしていきます。
【失敗事例】適合証明だけで選定 → 導入後に発塵トラブル
ある医療機器メーカーでは、ISO Class 5に対応すると記載されたAGVをカタログベースで選定し導入。しかし、排気ファンが側面にあり、可動部が開放構造だったため、稼働後に微粒子の製品付着が頻発。クリーン環境が想定より悪化し、品質管理部門からNGが出され、わずか半年でAGVを再選定する事態となりました。
このケースでは、「適合証明の有無」だけを重視し、「どのような試験条件か」「構造が清浄度維持に適しているか」という観点が欠落していたことが原因です。
【成功事例】導入前のクリーン検証で仕様見直し
一方、精密部品メーカーでは、導入前にAGVの実機を用いた簡易的なクリーンテストを実施。その結果、候補機がClass 3環境での発塵許容量を超えていたことが判明。より高密閉構造で、排気位置が制御された別モデルに切り替えることで、導入後は異物混入ゼロ、歩留まりが17%改善しました。
この事例から分かるのは、「現場環境での評価=信頼できる仕様選定」だということです。導入前のテストは、手間ではなくリスク回避の保険になります。
成功したAGV導入の具体的なパターンについては、こちらの記事も参考になります。
失敗の構造的原因とその波及フロー
次に、AGV導入における失敗が、どのような構造的原因から起こり、最終的にどのような損失へつながるかを図で整理しました。
[誤認識]
適合証明だけで選定を決定
↓
[原因構造]
排気位置・可動部密閉性を未確認
↓
[直接影響]
発塵発生 → 製品に粒子付着
↓
[間接損失]
品質不良・歩留まり低下・クレーム発生
↓
[業務負荷]
AGV再選定 → 再稟議・納期遅延・二重コスト
失敗は一時的な機械不良ではなく、構造的な選定プロセスの問題に起因することが多くあります。導入後に発覚するほど損失は拡大するため、初期段階で「構造と運用の整合性」を見抜くことが重要です。
なぜ初期投資だけを重視すると長期的コストが増えるのか?
「この機種ならスペック的に対応してそうだ」「価格も安いし、納期も早い」
こうした判断でAGVを選定した結果、後から思わぬコストが発生することは少なくありません。
たとえば、導入から1年以内に清浄度不適合が明らかになれば、再選定・再導入のために数百万円単位の費用が追加で発生します。それだけではなく、クリーンルームの稼働停止、社内稟議のやり直し、製品不良に対するクレーム対応といった「目に見えないコスト」も累積されていきます。
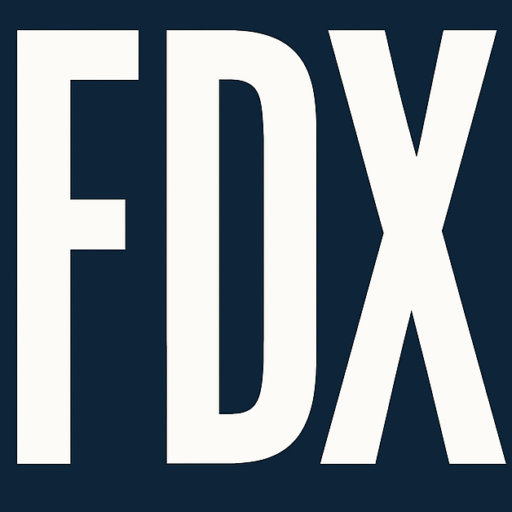
Factory DX
運営事務局
一方で、初期コストが高くても、発塵構造に優れ、構造密閉性が高いAGVを選べば、保守・運用の安定性が向上し、長期的な製品品質の安定・異物混入ゼロ・再稟議不要といった恩恵を受けられます。
AGV選定においては、「目先の価格」ではなく「構造と運用の整合性」こそが、企業の信用と利益を守る最も合理的な判断軸になるのです。
AGV選定で迷ったら必見!今すぐ使える比較チェックリスト5項目
クリーンルーム対応AGVの選定は、単なる設備選びではありません。それは製品品質・ラインの安定稼働・異物混入防止といった製造現場の根幹に関わる重要な判断です。しかし、多くの現場では「資料は揃っているが、何を見て判断すれば良いのか分からない」「社内稟議用に基準を整理したい」といった声が上がります。
こうした悩みを解決するために有効なのが、客観的なチェックリスト形式での比較検討です。複数メーカーのAGVを同じ基準で評価することで、主観に左右されず、仕様の比較や課題の洗い出しをスムーズに行えます。
とくに導入後のトラブルを避けるためには、「清浄度証明」「構造の密閉性」「材質と表面処理」「保守の実現性」といった要素を明確にチェックすることが欠かせません。以下に、実際の選定業務に活用できるチェックリストを用意しました。
AGV選定のチェックリスト(導入前の確認表)
導入前に複数メーカー・複数モデルを比較検討する際に、そのまま活用できるチェックリストです。要件の見落としや属人的な判断を排除し、稟議資料や技術仕様レビューにも対応可能です。
チェック項目 | 状態 | コメント/根拠資料 |
---|---|---|
清浄度適合証明の有無 | □ 済 / □ 未 | 発行元と試験環境の記載確認 |
材質仕様の明記(SUS種類・塗装) | □ 済 / □ 未 | SUS304/316Lの材質証明、塗膜仕様 |
排気設計(HEPA/循環型か) | □ 済 / □ 未 | 吸排気構造の模式図・仕様書 |
密閉構造(駆動部・制御部含む) | □ 済 / □ 未 | 可動部・モーター周辺の防塵設計図 |
洗浄・保守対応性(工具・薬品耐性) | □ 済 / □ 未 | 薬品使用可否と洗浄マニュアル有無 |
このチェックリストは、営業資料やカタログスペックだけでは見落とされがちな“構造的適合性”を客観的に評価するための道具です。
特にクリーンルーム環境においては、表面材質や排気構造が清浄度維持に直結するため、導入前に仕様の裏取りを行うことで、失敗リスクを大幅に削減できます。現場担当者・品質保証・保守部門との連携評価にも最適です。
このように、選定の判断軸を明文化しておくことで、技術担当者だけでなく、品質管理・経営層への説明も容易になります。また、複数メーカーを比較した際にも判断基準をぶらさずに検討できるため、より合理的で確実な設備導入が実現できます。
チェックリストはそのまま稟議書や比較表の一部としても活用可能です。導入の失敗を防ぎたいなら、まずはこのリストから始めてください。
まとめ|AGV導入を成功させる鍵は“清浄度と構造”の見極めにあり
クリーンルーム対応AGVの選定において、最も大きな落とし穴は「見た目のスペックや清浄度ラベルだけを信じてしまうこと」です。多くの導入失敗は、ISOクラスなどの“表面的な適合”と、実際のAGVの構造仕様との間にギャップがあることに気づかず、導入後にトラブルが顕在化するケースです。
逆に言えば、失敗を避ける方法は非常にシンプルです。
それは、「清浄度要件と構造仕様の整合性を導入前に徹底的にチェックすること」に尽きます。とくに重要なのは、排気方式、可動部の密閉性、使用材質、証明書の信頼性といった要素を、カタログ情報にとどまらず、実機や技術資料を通じて確かめる姿勢です。
導入準備に時間をかけることは、遠回りではなく長期的な品質維持・運用安定・社内評価の向上につながります。とくにクリーン環境下での製品は、少しの異物混入や粒子付着が大きな損失を招くため、AGV選定の精度がそのまま製造リスクの最小化に直結します。
もし選定に迷った場合は、自社だけでの判断にこだわらず、構造や清浄度制御に詳しい外部パートナーや専門家と連携し、仕様書ベースでの技術評価を行うのが効果的です。選定段階での“見立ての正確さ”が、その後の運用コストや品質トラブルの発生頻度を大きく左右することを忘れてはなりません。
選ぶべきは「とりあえず対応しているAGV」ではなく、「自社の清浄度環境に最適化されたAGV」です。その視点を持つだけで、導入後の安心感と長期的な成果は格段に高まります。
AGV導入後に発覚する「見込み違い」を避けるためのチェックリストを用意しました。
運用開始後に後悔しないために、導入前に確認すべき10のポイントを紹介。
先に知っておくことで、大きなトラブルを未然に防げます。
→ 失敗回避チェックリスト付き資料を今すぐダウンロード