自動化や省人化の流れが加速するなか、AGV(無人搬送車)は多くの工場や物流センターで導入が進んでいます。「人件費の削減」「作業の標準化」「24時間稼働の実現」など、業務効率化の要として大きな期待を背負っています。しかし、AGVを導入したにもかかわらず、ヒヤリ・ハットや接触事故、誤搬送といった問題がなくならない現場も少なくありません。
なぜ、最先端のテクノロジーを搭載したAGVでも、安全面のトラブルが後を絶たないのでしょうか。
その根本的な原因は、センサーの性能不足や設定ミスといった「機械側の問題」だけではなく、現場に最適化されていない「安全設計の不備」にあります。
本記事では、AGVの安全性を確保するために不可欠なセンサー技術の全体像、安全運用設計のポイント、そして実際に発生した事故とその教訓をもとに、「安全に使いこなせるAGV」の条件を徹底解説します。
AGV運用の盲点とは?現場で頻発する4つの安全リスクとその要因
AGVの運用現場で発生する主な安全リスクは、大きく分けて以下の4つに分類されます。それぞれのリスクは現場の構造や運用ルール、センサー構成によって顕在化しやすく、見過ごされがちな原因が潜んでいます。
障害物との衝突
通路の幅が狭かったり、棚や壁の配置が変わるようなレイアウトでは、AGVが障害物に気づかず接触してしまうケースがあります。特に、急なカーブや死角が多いエリアでは、センサーだけでは検知しきれない場合があり、接触による設備破損や商品損傷のリスクが高まります。
人との接触
人とAGVが同じエリアで作業をする場合、見通しの悪い交差点や、作業員の動線がAGVのルートと交差する場所は接触リスクが高くなります。作業員がAGVの接近に気づかない、あるいはAGVが死角にいる人を検知できない状況が、事故につながります。
誤搬送・ルート逸脱
ナビゲーションの要であるQRコードや磁気テープが汚れたり破損していた場合、AGVは正しいルートを認識できずに誤搬送を起こすことがあります。また、ナビゲーションシステムの設定ミスが誤走行の原因となることもあります。
QRコード誘導型AGVの精度を左右する貼り方の注意点については、こちらの記事で詳しく解説しています。
通信エラー・制御不能
AGVは無線LANや通信プロトコルを通じて管理システムと連携していますが、電波干渉や通信不良がある環境では、指示が正しく伝わらず停止したり、想定外の動作を起こすリスクがあります。これらは単なる一時的なトラブルにとどまらず、ライン全体の稼働停止に直結することもあります。
AGVの安全性はセンサーが決める|知っておきたい構成技術と選定ポイント
AGV(無人搬送車)が安全に稼働し続けるためには、「人や障害物を正確に検知する能力」が欠かせません。特に近年、工場や物流センターでは人とAGVが同じ空間で作業をすることが増えており、衝突や接触事故を未然に防ぐには、AGVの“目”であるセンサー技術がその真価を問われる状況となっています。
センサーはAGVの知覚機能にあたり、その精度と反応速度が安全性を決定づける要素です。しかし、センサーには得意・不得意があり、現場の環境や運用方法によっては単独では限界があります。だからこそ、どのセンサーを、どこに、どう配置するかは、安全設計の中核的なテーマであり、AGV導入時に最も慎重に検討すべきポイントなのです。
ここでは代表的なセンサーの特性を比較しつつ、読者が「どれをどう使えば安全性が高まるのか」を具体的にイメージできるよう整理していきます。
センサー種類と機能の比較一覧
AGVの安全設計で最初に考慮すべきポイントは「どのセンサーをどこに、どのように設置するか」です。以下は、主要センサーの役割と特徴を一覧化したものです。
センサー種類 | 主な役割 | 検知距離目安 | 得意な検知対象 | 苦手な条件・注意点 | 主な設置位置 | 導入コスト感 |
---|---|---|---|---|---|---|
LiDAR(レーザー) | 周囲360°の障害物検知 | 2〜10m | 固定物体(棚・壁・人) | 環境光の影響、透明・黒物体 | 本体上部中央 | 高め |
超音波センサー | 近距離の障害物検知 | 0.1〜2m | 壁面、足元など低位置の物体 | 斜面・ガラス面は苦手 | 前方・側面 | 中程度 |
カメラ(ビジョン) | 人物・QRコードの識別 | 1〜5m | 人物、標識、印刷物 | 暗所や逆光で性能低下 | 前面/上部 | 高め |
バンパーセンサー | 接触時の非常停止 | 接触時 | 全対象(物理接触) | 一次被害が発生してから作動 | 本体前後左右 | 低め |
安全用PLC | 緊急停止制御、システム連携 | 制御全体 | センサー入力全体 | 設計と検証に専門知識が必要 | 制御盤・本体内部 | 中〜高 |
AGV導入時には、現場の環境条件と照らし合わせながら、最適なセンサー構成を見極めることが求められます。
なぜ「複数センサーの併用」が必要なのか?
LiDARは高精度で広範囲をカバーできますが、ガラスや透明な素材には弱く、逆に超音波センサーは狭い範囲しか見えないものの、低い障害物には強い傾向があります。カメラは画像認識によって人物やQRコードの識別に優れるものの、暗所や逆光といった照明条件に大きく左右されるという弱点があります。
このように、どのセンサーも「万能」ではなく、必ず検知漏れや誤認識のリスクが存在します。
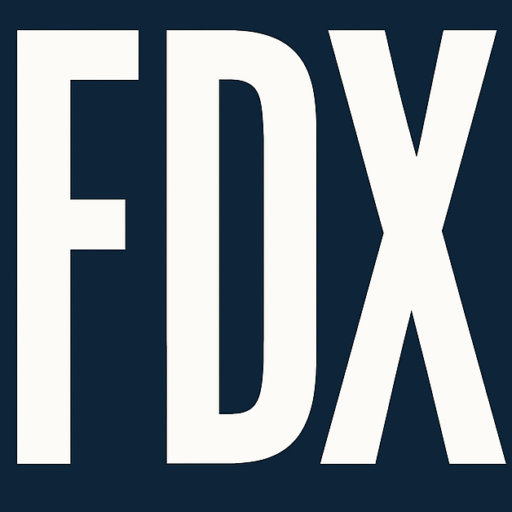
Factory DX
運営事務局
だからこそ、異なる特性を持つセンサーを組み合わせ、互いの弱点を補完し合うことが、実運用における最適解なのです。
たとえば、LiDARで広域スキャンを行いながら、足元の物体検知を超音波センサーで補完し、QRコードの読み取りはカメラで担う。さらに、非常停止用としてバンパーを設置し、全体の安全制御はPLCが統括する。こうした「多層構造の安全設計」は、ヒューマンエラーが起きがちな現場でこそ、真の強みを発揮します。
センサー性能を活かすための「環境設計」
センサーの性能を100%引き出すには、センサー選定だけでなく「周囲環境の整備」が不可欠です。カメラでQRコードを読み取るには、照度が一定以上であること、コードが汚れていないことが前提です。LiDARの性能も、反射率の低い素材や逆光などで精度が落ちることがあります。
よって、センサーの「物理的な視界」を確保するために、以下のような環境整備が求められます。
- AGV通路の清掃ルールを徹底し、QRコードやラインの汚れを防止する
- 照明を均等に配置し、暗所・逆光を最小限に抑える
- センサー前の視界を遮る什器や荷物を置かないようにする
これらは一見地味な運用ルールですが、安全性の観点ではきわめて実効性の高い施策です。
また、QRコード方式をはじめとする各ナビゲーション技術の特徴と、導入環境に応じた選び方については、こちらの記事で詳しく解説しています。
センサーの「死角」をどう対策するか
どれほど高性能なセンサーを使っても、「死角ゼロ」は実現できません。たとえば、LiDARは水平面をスキャンするため、AGVの直下や足元には検知漏れが発生します。また、AGV本体の背面や側面に人が近づいた際、センサーの配置によっては反応できないこともあります。
こうした死角に対応するためには、以下のような設計的工夫が求められます。
- AGV前後左右にバンパーを設置し、接触時に即停止できるようにする
- 超音波センサーを側面にも配置し、近距離での検知範囲を広げる
- 死角の多い交差点やカーブにはミラーやLED警告灯を設置し、人の注意を促す
センサー設計はあくまでも「リスクを減らす手段」であり、現場ごとの運用設計と組み合わせてはじめて最大の効果を発揮します。
「センサーに任せきりにしない」運用体制を
センサーはAGVの安全性を支える柱ですが、それだけでは安全性は確保できません。
なぜなら、センサーは「検知する」ことはできても、「判断する」ことまでは単独ではできないからです。だからこそ、作業員の教育や現場ルールの整備、定期点検・メンテナンスが欠かせません。
また、事故が起きたときの「フェイルセーフ設計」、つまり安全に停止できる体制が整っているかも重要です。安全用PLCや緊急停止スイッチ、遠隔監視システムといったハード・ソフトの両面を通じて、万一の際にも対応できる仕組みを構築することが、AGV運用の成熟度を高めるカギとなります。
このように、センサー技術はAGV安全設計の「出発点」であり、運用設計・環境整備・教育体制と一体化してはじめて、本当の意味での「安全なAGV」が実現します。
AGVを止めないための点検体制や運用ルールの整備については、こちらの記事でも詳しく解説しています。
技術の選定と同じくらい、使う現場の状況を理解し、設計に反映させる目線が求められます。ユーザーが導入・運用の過程でこの視点を持つことで、事故のない、効率的なAGV運用へと確実に近づくことができるでしょう。
AGVの安全走行はこう設計する|事故を防ぐ制御技術と現場設計の最適解
AGVにどれだけ高性能なセンサーを搭載しても、それだけで安全が担保されるわけではありません。センサーは「状況を感知する機能」であり、その感知結果をもとに「どう動くか」を判断するのは、設計と制御技術の役割です。
つまり、センサーと制御は両輪であり、一方が欠けていては真の安全性は実現できないのです。
このセクションでは、AGVが安全に走行し続けるために欠かせない設計・制御の考え方を、実際の現場視点を交えて掘り下げていきます。特に、減速ゾーンの設定、危険エリアのゾーニング、そして異常検知時の即時対応は、事故を防ぐための実務的な柱です。
安全マージンと減速ゾーンの設計
AGVが障害物や人に接近した際に自動で減速・停止する仕組みは、安全設計の基本中の基本です。
たとえば、AGVが走行中に人影を検知した場合、3メートル手前で減速し、1メートル以内に入った時点で完全に停止するような「二段階制御」が一般的です。これはLiDARや超音波センサーの検知距離を踏まえ、AGVの慣性や床面状況(滑りやすさ)なども加味して設定されます。
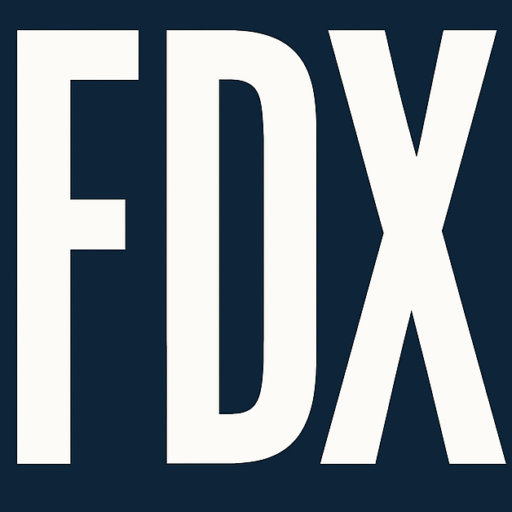
Factory DX
運営事務局
重要なのは、「減速→停止」の距離設計が現場に最適化されているかどうかです。
通路幅、作業者の動線、AGVの積載重量などに応じて、安全マージンは再設計されるべきです。単に工場全体で「一律3メートル前で減速」とするのではなく、エリアごとに動線とリスクを分析し、きめ細かなゾーン設定を行うことで、真の安全性が確保されます。
また、減速ゾーンを「見える化」する工夫も効果的です。床に色分けやラインを引き、「この先徐行エリア」と視覚的に伝えることで、人とAGVの双方に注意喚起ができます。これはセンサーにはできない「人への配慮」であり、現場力を高める設計です。
危険エリアのゾーニングと走行制限
事故が起きやすいエリアには明確な特徴があります。例えば、フォークリフトが頻繁に通行する開口部、作業者が密集する作業台周辺、荷物の出入りが激しい搬出入スペースなどは、接触リスクが非常に高くなります。
こうした場所には、AGVが自動で進入しないよう「危険エリア」としてゾーン制御をかける必要があります。最新のAGVは地図データに応じて「このエリアは進入禁止」「このエリアは徐行」などのルールを持たせることが可能です。センサーがそのエリアに入ったことを検知すると、走行スピードを変える、進行を止めるといった動作に自動的に切り替わります。
ゾーン制御による安全エリア分割のイメージ図
▼ AGVのゾーン制御マップ例(上面レイアウト)
++
| 赤:危険エリア(進入禁止) |
| ┌──────┐ |
| │ │ フォークリフト |
| └──────┘ 出入り口 |
| |
| 黄:減速エリア(徐行) |
| ──────────────── |
| 青:通常走行エリア |
| →→→→→→→→→→→→→→→→→→→→ |
++
ゾーン制御はAGVそのものの制御精度だけでなく、「現場をどう可視化するか」「リスクをどうルール化するか」という視点が重要です。AGVはルールに従って動くだけなので、そのルールを設計する側の責任が、安全性の成否を分けると言っても過言ではありません。
また、ゾーン分けはメンテナンスやレイアウト変更時に見直されるべきです。設計当初は安全だったルートも、棚の配置が変わったことで死角が生まれたり、人の動線が交差したりすることがよくあります。ゾーニングは一度設計したら終わりではなく、定期的なレビューが必要です。
異常検知時の自動停止・通知機能
センサーの誤作動やシステム異常は、どんなに優れた機器でもゼロにはできません。
だからこそ、「異常が起きたとき、どれだけ早く・安全に止められるか」が安全設計の最後の砦となります。
たとえば、超音波センサーが誤検知を起こして通信が断絶された場合、AGVがそのまま動き続ければ、接触事故に直結します。そのため、安全用PLC(プログラマブル・ロジック・コントローラー)は異常信号を検知すると即時に走行を停止し、管理システムに通知を飛ばします。
この制御が「機械的な保険」として確実に機能していることは、現場の信頼性を保つうえで欠かせません。特に夜間や人手の少ない時間帯には、AGV自身が異常を自己判断し、必要な停止処理と情報伝達を完結できる体制が求められます。
異常検知時の安全制御フローチャート
▼ AGVの異常検知フロー
[センサー異常検知]
↓
[安全用PLCが受信・解析]
↓
[AGV自動停止]
↓
[管理システムに即時通知]
↓
[作業者が現場確認/復旧対応]
このようなフェイルセーフ機構は、万一の事故時に「なぜ止まらなかったのか」という致命的な問いを防ぐための最低限の安全装置です。AGVの選定時には、この制御系の信頼性(応答速度、誤動作率、冗長設計)も必ず確認しましょう。
安全制御設計は「現場で生きる設計」であること
制御設計において忘れてはならないのが、「現場で本当に使われる運用に即しているか」という視点です。たとえば、減速距離を3メートルと設定していても、実際の通路幅が2メートルしかなければ、その制御は機能しません。
同様に、AGVが減速するはずのエリアに私物の棚が置かれていたり、フォークリフトと共通ルートを取らざるを得ない構造だったりすれば、理論上の設計と現場実態のギャップが事故の原因になります。
だからこそ、安全制御設計は図面上の設計だけでなく、「現場観察」と「現場ヒアリング」を踏まえて調整されるべきです。設計者と現場担当者が連携し、仮運用とレビューを重ねながら設計を磨き上げるプロセスこそが、安全運用の鍵を握っています。
AGVは単なる移動機械ではなく、「人と共に動く現場の一員」です。その前提に立った設計と制御の工夫が、接触ゼロ・事故ゼロを実現するための最短ルートと言えるでしょう。安全は「製品の性能」ではなく「設計と運用の融合」によってつくられるという視点が大切です。
AGVのセンサー配置と運用ゾーンの関係|事故を防ぐ設計とは
AGVの安全運用において、センサーの設置位置とそのカバー範囲は、検知精度に直結する極めて重要な要素です。どれほど高性能なセンサーを搭載していても、「どこに設置するか」「どの方向をカバーするか」が不適切であれば、死角が生まれ、事故の原因になり得ます。
また、センサーの検知能力を最大限に活かすには、センサー単体の性能だけでなく、現場全体の運用設計と連動させたレイアウトが不可欠です。このセクションでは、AGVのセンサー配置と安全運用エリアの関係を図解しながら、具体的な活用例や注意点を紹介します。
AGV本体のセンサー配置(上面図)
┌────────────────────┐
│ カメラ(QR検知・人物識別) │
│ │
│ 超音波 ◀── 前方 ──▶ 超音波 │
│ │
│ バンパー [AGV本体] バンパー │
│ │
│ LiDAR(360度)中央設置 │
└────────────────────┘
この図は、AGVに搭載される代表的なセンサーの配置を上面から見たレイアウトとして示したものです。
中央に設置されたLiDARは、360度の周囲検知を可能にするAGVの“目”ともいえる存在です。物体までの距離を高精度で測定でき、AGVの進行方向だけでなく、側面や後方の障害物にも素早く反応します。
AGVの前方には、近距離での障害物検知に優れた超音波センサーが設置されています。これは主に足元の障害物や、棚やパレットなど低位置の対象物を検知する役割を担っています。
さらに、カメラは上部または前面に配置され、QRコードの読み取りや人物の認識を担当します。照度の影響を受けやすいため、安定した光環境が前提となります。
そして最も物理的に反応するのが、前後左右に取り付けられたバンパーセンサーです。これは物体に実際に接触した瞬間に作動し、即座にAGVを停止させます。あくまで“最終手段”としての安全装置ではありますが、接触後にしか作動しないため、事前防止ではなく「二次被害の最小化」に寄与します。
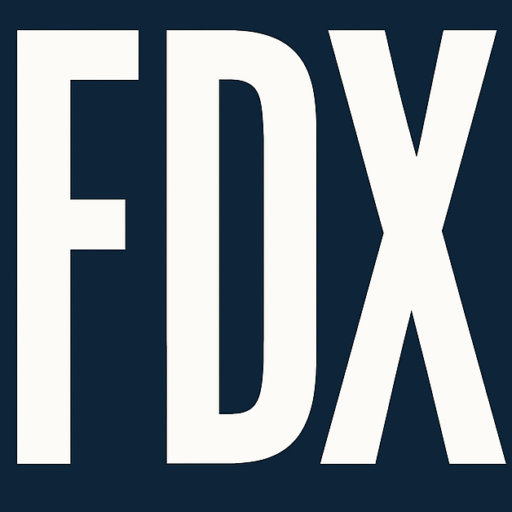
Factory DX
運営事務局
死角を減らしつつ、センサー同士が相互補完するような配置が、安全性を大きく向上させる鍵となります。
このように、AGVの各センサーは特性が異なり、それぞれが異なる方向・目的を持って配置されています。
エリアごとの安全運用設計(ゾーン色分け)
┌─────────────┐
│ 危険エリア(立ち入り禁止) │ → AGV進入不可ゾーン(赤)
├─────────────┤
│ 減速エリア │ → AGV徐行エリア(黄)
├─────────────┤
│ 通常走行エリア │ → 通常ルート(青)
└─────────────┘
センサーの配置と同様に重要なのが、現場全体の運用設計です。AGVがどのエリアでどのように走行するかをあらかじめ設計しておくことで、事故のリスクを事前に大きく低減できます。
この図にあるように、AGVの運行エリアは大きく分けて3つにゾーニングされます。
- 赤色の「危険エリア」は、作業者が頻繁に出入りする場所やフォークリフトの走行エリアなど、AGVとの接触リスクが高いため、原則として進入禁止とします。
- 黄色の「減速エリア」は、人とAGVが交差する可能性がある空間や、視界が悪くなるカーブ、出入口付近などに設定され、AGVはこのエリアでは自動的に徐行します。
- 青色の「通常走行エリア」は、障害物も人の往来も少ない、安全性が高いゾーンです。AGVはこのエリアで通常速度での運行が可能です。
このようなゾーン設定は、AGVの制御システムと連動させることで自動化が可能です。たとえば、減速エリアに入ると自動的に速度が制限され、危険エリアに近づくと警告を発したり、進入を停止するなどの制御を行うことで、安全性を一段と高められます。
加えて、このゾーン分けは視覚的にも現場作業員に伝える必要があります。床面に色分けを施す、サインボードや注意喚起表示を設置するなどの工夫を通じて、ヒューマンエラーを未然に防ぐことができます。
ゾーニングとセンサー配置は別個のものではなく、両者が連携して初めて実効力を持ちます。センサーが検知した情報をもとに、どのゾーンでどの動作をするのかを定義すること。それがAGVの安全な運用を可能にする、最も基本的で、かつ最も強力な仕組みと言えるでしょう。
現場ごとに異なるレイアウトや作業フローに対応するためには、このような柔軟な運用設計が不可欠です。安全運用は、センサー技術だけでなく、それを支える「設計の意図」と「現場の理解」の両輪によって初めて成立するということを、あらためて意識しておきたいところです。
AGV導入で接触事故が起きた本当の理由|見落とされた設計ミスとは?
テクノロジーが高度化しても、事故はゼロにはなりません。ここでは、実際に発生したAGVの接触事故や誤搬送トラブルを紹介し、その背景と見落とされがちな要因、そこから得られる教訓を整理します。
ケース①:作業員の足とAGVが接触した事故
背景と発生状況
ある製造工場で、作業員が部材を積み下ろししていた場所にAGVが接近。作業員がLiDARの死角に入っていたため、AGVは人を検知できずそのまま前進し、足先に接触。幸いにも軽傷で済んだものの、直後にラインが停止し、復旧・報告対応で半日のロスが発生しました。
問題点と原因
- LiDARの設置位置が高すぎて足元が検知範囲外だった
- 作業員の動線設計がAGVルートと交差していた
- 作業員がAGVに気づくまでの警告が不足していた
教訓
センサーに頼りきるのではなく、動線設計や作業者への教育、予防的なゾーン設定が重要です。現場視点の「ヒューマンファクター」まで含めた安全設計が求められます。
ケース②:QRコードの読み取り不良による誤搬送
背景と発生状況
別の物流センターでは、AGVがQRコードを読み取れず、誤ったルートを走行し、本来とは異なる工程に部材を搬送してしまいました。結果、後工程の生産ラインが停止し、作業者は手作業で修正対応に追われました。
原因と見落としポイント
- QRコードの汚れや破損が読み取り精度を大きく低下させていた
- 照明のムラや反射によってカメラが誤認識した
- コードメンテナンスや定期清掃がルーチン化されていなかった
教訓
「機械が勝手に正しく動くはず」という思い込みは禁物です。センサー性能を最大限に引き出すためには、物理環境(光、清掃、反射防止など)の整備も不可欠です。
AGVのトラブル事例やその防止策について、より多角的な視点から知りたい方は、以下の記事も参考になります。
ヒヤリ・ハット事例:接触事故の発生プロセス
事故が起きたプロセスを時系列で整理すると、以下のような流れが見えてきます。
▼ 作業員と接触した事例(プロセス図)
[作業員がAGVルート内に立ち入り]
↓
[死角でセンサーが検知できず]
↓
[AGVが通常速度で接近]
↓
[接触(軽傷発生)]
↓
[稼働停止 → 報告対応 → 半日ロス]
このように、センサーだけに頼った設計では防げないリスクが存在します。複合的な設計・教育・メンテナンス体制が不可欠です。
AGVが人と安全に働く時代へ|センサー・AI融合の最前線を徹底解説
技術は日進月歩です。ここからは、今後さらに進化が期待されるAGVの安全技術と、選定時に確認すべき基準について紹介します。
協働型AGVの台頭
従来のAGVは「人がいない環境で使う」ことを前提として設計されていましたが、今では「人と共存する」協働型AGVが増えています。たとえば、人の動きをセンサーで先読みして減速したり、手を挙げる動作を認識して停止する機能を持ったモデルも登場しています。
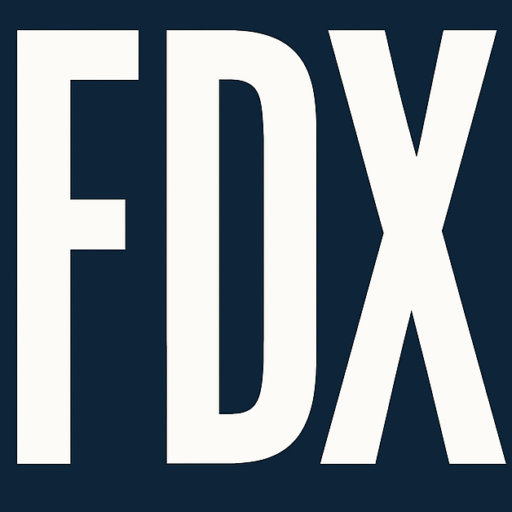
Factory DX
運営事務局
これにより、より柔軟で人間中心の現場運用が可能となっています。
センサー冗長化とAIによる高度な判断
センサー1つに異常が起きても安全性を維持できるよう、複数のセンサーを同時に使用する「冗長設計」が普及しつつあります。さらに、AIによる映像解析を組み合わせることで、人の動作パターンや環境の変化をリアルタイムに学習し、判断することが可能となっています。
センサー冗長化+AI融合による判定構造図
以下は、複数センサーの情報を統合してAIが判断し、PLCが制御するイメージ図です。
▼ センサー冗長構造+AI処理のイメージ
[LiDAR]──┐
↓
[超音波]──→【センサーハブ】→【AI判定ユニット】→【制御PLC】
↑
[カメラ]──┘
・センサーハブで統合 → AIが異常判断 → PLCが停止制御
このような構造により、見逃しや誤検知のリスクが劇的に減少し、現場に最適化された運用が可能になります。
安全規格(ISO3691-4など)の対応チェック
AGVを選定する際に見落とされがちなのが、安全規格の対応有無です。スペックや速度ばかりが注目されがちですが、「どの安全規格に準拠しているか」を確認することで、その製品がどこまで信頼できるかが判断できます。
AGV導入前の確認事項として、ぜひ以下の観点をチェックしてください。
項目 | 対応状況確認のポイント |
---|---|
ISO 3691-4 対応 | 安全走行設計の基本指標 |
フェイルセーフ機構の有無 | 緊急停止が自動で行えるか |
センサー冗長設計の採用有無 | 単一障害で誤作動しない構造か |
運用支援体制(サポート・教育) | 導入後のフォローがあるか |
このリストを参考に、導入候補のAGVが安全面で十分な設計を持つかどうか、選定時に必ず確認してください。
まとめ|AGVの安全性を高めるにはセンサーと運用設計の両立が不可欠
AGVの安全性を確保するためには、ただ高性能なセンサーを搭載するだけでは不十分です。現場の構造や人の動線、作業者の習熟度、物理環境(光・温度・清掃状況)など、多角的な要素を考慮したトータルな安全設計が不可欠です。
センサーはあくまでも「リスクを検知する道具」であり、それをどう配置し、どう運用し、どう管理するかによって、実際の安全性は大きく変わります。AGVを「現場のパートナー」として根付かせるためには、以下の観点を網羅的に整備することがカギとなります。
- 検知精度に合ったセンサー構成と配置設計
- 人と機械の動線が交差しないレイアウトの見直し
- 異常時に即座に止まるフェイルセーフ設計
- 定期点検・清掃・教育のルーチン化
- AIや冗長化による次世代的なリスク予測の導入
- 規格(ISO3691-4等)への対応確認と導入前後の支援体制
これらを総合的に満たすことで、AGVは「事故を未然に防げる安全な運用資産」となり、現場の生産性と安心感の両立が実現します。
無料AGV資料ダウンロードのご案内
「こんなはずじゃなかった」を防ぐための失敗回避チェックリスト付き。
設備・人員・搬送ルート…見逃しやすい落とし穴が詰まっています。
導入前に確認しておくだけで、安心感が格段に違います。
→ 導入前チェックリスト付き資料を今すぐ見る