AGV(無人搬送車)を導入する際、「床にQRコードを貼れば簡単に動く」と考えている方は少なくありません。確かに、QRコード誘導は低コストかつ柔軟な方式として注目されています。しかし現場では、「思った通りに走らない」「突然止まる」「誤作動を起こす」といったトラブルに悩むケースが後を絶ちません。
本記事では、AGVのQRコード誘導方式について、単なる仕組み解説にとどまらず、「現場で失敗しないために必要な実践知」を徹底的に解説します。導入前に知っておくべき設計の要点、貼付精度の重要性、精度トラブルの具体的な原因と対策まで、現場担当者が自分ごと化できる構成でお届けします。
- AGVが止まる・ズレるのはなぜ?QRコード誘導で現場が陥りがちな誤解
- AGVはどうやって動いている?QRコード誘導の基本メカニズムを解説
- AGV運用の成功例に学ぶ QRコード誘導が最適な現場とは
- どの方式が現場に合う?AGVナビゲーションの違いを比較で解説
- QRの貼り方が精度を左右する|AGV運用で押さえるべき設置の基本
- AGVの誤停止を防ぐには|QRコード読み取り精度を保つための基本対策
- AGVの誤作動を防げ|QRコード誘導トラブルの実例と対応策
- AGV運用の失敗から学ぶ|QR誘導トラブルの実例と再発防止策
- AGVの安定稼働に欠かせない|QRコード誘導を成功させる3つの要点
- QRコード誘導で失敗しないために|AGV導入の実践ポイント総まとめ
AGVが止まる・ズレるのはなぜ?QRコード誘導で現場が陥りがちな誤解
AGV(無人搬送車)のQRコード誘導は、「簡単に導入できる」「床にコードを貼ればすぐ走る」といった印象を与えがちですが、それが大きな落とし穴になることもあります。実際、導入現場で多く報告されているのは、「止まる」「ズレる」「途中で読み込めない」といったトラブルです。
たとえば、導入して間もないある製造現場では、毎日のようにAGVが特定の地点で停止。その都度スタッフが再起動対応に追われ、業務効率が大きく低下しました。原因は、床に貼られたQRコードが光沢床材に反射して読み取れなかったこと。現場では「コード自体に問題はなかったはず」と認識していましたが、環境条件の見落としが原因でした。
このように、QRコード誘導は「簡単なようで、実は繊細」な技術です。手軽に設置できる一方で、現場環境・貼付精度・点検体制が適切でなければ、運行中に小さなズレが蓄積し、大きなトラブルへと発展するリスクがあるのです。
もし、次のような疑問や状況に心当たりがあるなら要注意です。
- AGVが突然停止することがあるが、原因が分からない
- QRコードは貼ったが、特定の場所で読み取れない
- 新しい経路を追加したが、うまく走行できない
これらはすべて、「QRコードさえあれば動く」という誤認がもたらす典型的な失敗例です。
誤解と実態を比較する:QRコード誘導の“あるある”誤解と現実
AGVのQRコード誘導にまつわるよくある誤解と、それに対する実際の運用課題を一覧にまとめました。
誤解されがちなポイント | 実際に起こる現場課題 |
---|---|
QRを貼るだけで走行できる | カメラとコードの視認関係・照明環境に左右される |
コードが見えていれば必ず読み取れる | 光の反射・影・床の汚れで読取エラーが発生する |
少しくらい斜めに貼っても問題ない | 数ミリのズレがAGVの停止・誤作動を引き起こす |
テスト時に動いたなら、本番も問題ない | 現場環境が時間や天候で変化しやすい |
AGVのソフトが優秀だから補正してくれるはず | 読み取りエラーは物理的トリガーで起こるため補正困難 |
この表からも分かる通り、AGVのQRコード誘導は「設置時の目視での“なんとなく”の判断」では安定稼働を実現できません。導入前に現場環境を緻密に確認し、読み取り精度や運用時のチェック体制を整備することが不可欠です。
AGVはどうやって動いている?QRコード誘導の基本メカニズムを解説
QRコード誘導は、AGVの自己位置推定方式の中でも物理的なマーカーを使うことで、システムの簡略化と導入コストの削減を両立する技術です。AGVの底部に取り付けられたカメラが、床に貼付されたQRコードを逐次読み取り、自分の現在地や次の指令を把握します。
この方式では、QRコードそのものに以下のような情報を埋め込むことができます。
- 現在位置情報(x,y座標など)
- 動作指令(停止・旋回・加速など)
- 分岐判断(右折・左折・直進の分岐指令)
読み取った情報はAGV本体に搭載された制御プログラムによって解析され、あらかじめ設定されたルートマップと照合されながら走行が制御されます。
この仕組みのメリットは明確です。
- 物理的に経路が明示されるため、自己位置の誤認が起こりにくい
- レイアウト変更にも柔軟に対応可能
- 設備改修が最小限で済み、導入コストを抑えられる
一方で、弱点も存在します。特に、QRコードとカメラの物理的関係が乱れるとすぐに読取不能となるため、施工精度と点検体制の確立が不可欠です。
ここで触れたカメラや制御プログラムといったAGVの主要パーツが実際にどう機能しているかについては、こちらの記事で構造面からわかりやすく解説しています。
AGVを現場で安定稼働させるには、QRコードの貼付作業が単なる「貼る作業」ではなく、走行インフラを築く重要な工程であるという意識が求められます。現場での導入支援や施工テンプレートの導入を含め、「設計・施工・運用」が一体となった取り組みが成功の鍵を握ります。
AGV運用の成功例に学ぶ QRコード誘導が最適な現場とは
AGVにおけるQRコード誘導は、低コストかつシンプルな方式であるため、特定の現場環境で大きな効果を発揮します。その代表的な例が、小規模物流倉庫や、生産ラインの頻繁なレイアウト変更に対応しなければならない工場です。
なぜこれらの現場でQRコード誘導が選ばれるのか。その理由は、単に「安いから」ではありません。QRコード誘導が持つ、柔軟性と設置容易性という特性が、現場の制約や運用実態に非常にマッチしているからです。
たとえば、従来の磁気テープ誘導では、レイアウト変更時にテープの再設置や埋設工事が必要でした。一方、QRコード誘導であれば、床に貼る・剥がすの作業だけで経路変更が可能です。
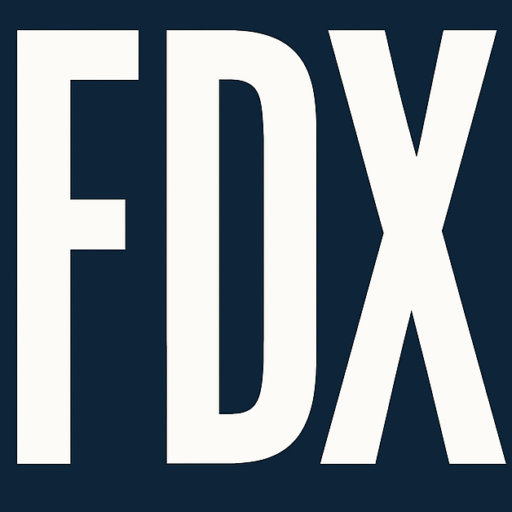
Factory DX
運営事務局
これは、特に「生産計画や製品種が頻繁に変わる中小製造業」にとって、極めて大きなメリットとなります。
また、建物の構造上、天井の高い倉庫や床材に特殊処理がされている場所では、SLAM方式のようなカメラ・センサーによる自己位置推定がうまく機能しない場合もあります。QRコード方式であれば、床面を基準とするため、構造物の影響を受けにくく、現場条件への適応力が高いのです。
このように、QRコード誘導は単なる「安価な代替手段」ではなく、現場の課題と適合する設計思想を持った選択肢であることが分かります。
経路や導入方式の選定に加え、“運用中の安全確保”が重要です。特に、AGVの衝突防止や誤搬送防止には、センサー設計と配置最適化が欠かせません。センサーによる安全性強化の具体策はこちらの記事をご覧ください。
QRコード誘導が適している現場タイプと導入理由の整理
以下に、QRコード誘導が特に適している現場の特徴と、その導入理由を対応づけて整理しました。
現場タイプ | 選ばれる理由 |
---|---|
小規模な物流倉庫 | 初期費用を抑えたい、設備改修が難しい、運用がシンプルで済む |
レイアウト変更が頻繁な生産現場 | 経路の再設定が容易、床に貼り直すだけで対応可能 |
中小製造業・部品工場 | 高額なSLAMや磁気誘導の導入が難しい、導入スピードが求められる |
天井が高い、構造が複雑な建屋 | SLAMが使いづらい、自己位置推定に建物の影響を受けにくい |
複数の製品ライン・工程が交差する工場 | 経路の複線化・ルート切替が視覚的に管理できる、柔軟な誘導が可能になる |
このような特性を活かせる現場では、QRコード誘導の価値は非常に高く、費用対効果が大きい投資となり得ます。
どの方式が現場に合う?AGVナビゲーションの違いを比較で解説
AGVのナビゲーション方式は、QRコード誘導だけでなく、磁気誘導やSLAM(Simultaneous Localization and Mapping)など多様な選択肢があります。方式ごとに、設置のしやすさ、運用の柔軟性、精度、コストが異なるため、自社の運用目的に合った方式を選定することが重要です。
たとえば、高精度な動きが求められる製造ラインでは磁気誘導が適していますが、現場の変更が少ないことが前提です。SLAM方式は最も高機能で柔軟性に優れていますが、その分システム構築や導入コストが大きく、専任人材も必要になります。
QRコード誘導はその中間に位置し、「導入しやすさ」と「運用の柔軟性」の両立を求める企業にフィットします。
AGVナビゲーション方式の比較表
QRコード誘導と他方式(磁気・SLAM)の違いを一覧化。導入前に向き不向きを明確に把握するのに役立ちます。
項目 | QRコード誘導 | 磁気誘導 | SLAM(自己位置推定) |
---|---|---|---|
設置の容易さ | 高い(貼付で完結) | 中程度(埋設工事あり) | 低い(マッピング作業) |
柔軟性(経路変更など) | 高い | 低い | 高い |
誘導精度 | 中程度 | 高い | 高い |
コスト | 低い | 中程度 | 高い |
適した現場規模・用途 | 中小規模/可変環境向け | 工場ラインなど固定経路 | 広域/複雑環境 |
この表からも明らかなように、QRコード誘導は「現場の変化に強い」「試験導入がしやすい」「初期投資が少ない」といった利点があります。だからこそ、「まずは導入して自動化をスタートしたい」という現場には最適な選択肢となるのです。
磁気テープやSLAM方式を含めたAGVナビゲーション方式の違いと選定ポイントについては、こちらの記事で詳しく解説しています。
逆に、すでにラインが固定されており、高速・高精度な運搬が求められる現場では磁気やSLAMが選ばれるべきです。技術の良し悪しではなく、「どの現場に何が合うか」という視点こそ、ナビゲーション方式を選定するうえで最も重要です。
QRの貼り方が精度を左右する|AGV運用で押さえるべき設置の基本
AGV(無人搬送車)がQRコード誘導で正確に走行するためには、単にQRコードを貼るだけでは不十分です。精度の高い運用を実現するには、「貼付の正確さ」と「レイアウト設計」に細心の注意を払う必要があります。
とくに以下の3点は、AGVの停止・誤走行などのトラブルを未然に防ぐための基本中の基本です。
- カメラとQRの位置関係(真下・水平)
- QRコードの間隔と配置設計
- 床材や照明の外部環境への配慮
カメラとQRの位置関係(真下・水平)
AGVに搭載されたカメラがQRコードを正確に読み取るためには、カメラの視野内にQRコードが常に真下で水平に収まるよう貼り付けることが重要です。カメラの中心軸とQRコードがずれていると、認識率が下がり、誤検知や読み取りミスにつながる可能性があります。
QRコードの間隔と配置設計
走行中のAGVが次の行動を判断するためには、適切な間隔でQRコードが配置されている必要があります。直線、カーブ、交差点、停止ポイントなど、走行条件に応じて貼付ピッチを変えることで、正確な誘導が実現できます。
床材や照明の外部環境への配慮
QRコードの読み取り精度は、床材の反射や照明環境によって大きく影響を受けます。たとえば、光沢のある床では照明が反射して読み取りエラーが発生しやすく、影や汚れも大きな障害となります。施工前に現場の床材や光源の配置を確認することが不可欠です。
QRコード貼付位置の基本構造
まず最も基本的なルールは、「QRコードはAGVのカメラが真下から垂直に視認できる位置に正確に配置する」という点です。この視認関係を視覚的に表すと、以下のようになります。
[ 上面図(俯瞰) ]
──────────────────
AGV本体(カメラ搭載)
↓
┌────────┐
│ QRコード │ ← 走行ライン中央に貼付
└────────┘
──────────────────
この図が示すように、AGVの底面に設置されたカメラは、進行方向に対して垂直にQRコードを読み取る構造になっています。そのため、走行ラインの中央から数ミリでもずれていたり、傾きがあるだけで、認識ミスや誤差が生じてしまいます。
貼付の際は以下を必ず確認してください。
- QRコードは必ず平滑で凹凸のない面に密着させる
- 粘着力が弱い素材は避け、業務用強粘着シートを活用
- 複数人でクロスチェックし、直線基準で貼るのが望ましい
QRコード貼付時の施工精度と並び、AGV誘導で広く用いられる磁気テープの貼り方にも共通する注意点があります。磁気テープの施工手順や失敗事例に関しては、こちらの記事も参考になります。
QRコード貼付間隔の目安表
QRコードの貼付は、どこに何枚貼るかも重要です。貼付間隔が不適切だと、AGVが次のQRコードを捉えられずに停止する、または過剰な指示入力で誤作動する可能性があります。
以下は、走行条件ごとの最適なQRコード貼付間隔をまとめた表です。
走行条件 | 推奨間隔の目安 | 備考 |
---|---|---|
直線区間 | 800〜1000mm | 高速走行時は短めに調整可能 |
カーブ/交差点付近 | 400〜600mm | 曲がり角での精度確保のため必須 |
停止・旋回ポイント | 任意(個別配置) | 命令QRを明示的に配置 |
この表のポイントは、「状況に応じた可変性」です。たとえば、直線では800〜1000mmで安定走行可能ですが、カーブでは視認角度や車体の振動が発生しやすいため、貼付間隔を半分以下に詰める必要があります。
また、停止ポイントでは、停止命令を確実に伝えるため、他のコードより大きめのQRコードを個別に配置することも効果的です。
QRコード貼付のOK・NG比較例
ここでは実際にありがちな施工ミスと、理想的な貼付例を対比形式で示します。
貼付例 | 状態 | 判定 | 解説 |
---|---|---|---|
水平・中央に密着 | カメラ真下、平滑面に施工 | OK | 最も安定して読み取りが可能 |
斜めに傾いて貼付 | AGV進行方向と角度ズレあり | NG | 誤認識・読み飛ばしの原因になる |
浮きや段差あり | QRの端が浮いている・段差あり | NG | 影・反射が起こり読み取りエラー発生 |
このようなNG例は、初期施工時に「目視でなんとなく真っ直ぐ」に貼ってしまうことが主な原因です。とくに薄い素材の床や、微妙な傾斜がある現場では、治具やテンプレートを使用して物理的に位置合わせするのが確実です。
さらに、貼付後のカメラ視認テストを必ず行い、AGVが実際に読み取れているかどうかを確認する運用ルールを整えることが不可欠です。
選定の失敗は、現場に合わないAGVを選ぶことから始まります。
タイプ別の特徴比較と選び方のコツをわかりやすく解説しました。
検討の方向性を正しく見極めるために、今手に入れてください。
→ AGV選びの基本資料を無料で確認する
AGVの誤停止を防ぐには|QRコード読み取り精度を保つための基本対策
AGVがQRコードを安定的に読み取り、正確に走行するためには、「貼る位置が正確であること」に加えて、「カメラの構造特性に応じた設計配慮」が不可欠です。特に、AGVに搭載されているカメラの向きによって、QRコードに求められる条件は大きく変わります。
AGV用カメラは、大きく分けて以下の2タイプに分類されます。
- 上向き読取型:カメラが下からQRコードを見上げて読み取る方式
- 下向き読取型:カメラが上から床面のQRコードを見下ろして読み取る方式
それぞれの構造的な特徴と、QRコードの設計・運用における注意点を、以下の図で整理します。
[ カメラ読取型の違い ]
┌────────────┐
│ 上向き読取型 │ ← 高い位置から見るため「サイズ・照明」が重要
└────────────┘
┌────────────┐
│ 下向き読取型 │ ← 床の傷・汚れに影響されやすく「清掃と貼付精度」が重要
└────────────┘
この図からも分かるように、上向き型は比較的高い位置からQRコードを捉える必要があるため、「視野の確保」と「照明環境」がカギを握ります。AGV本体のシャシーや周囲の障害物が視界を遮らないように配慮しつつ、QRコード自体のサイズを大きめに設定するのが一般的です。
一方で、下向き型カメラはQRコードとの距離が近いため、コードの小さな汚れや、床面の凹凸・反射といった「マイクロレベルの環境要因」に非常に敏感です。導入前に、床材の性質、日常清掃体制、光の当たり方を総合的に確認し、状態を維持できるよう運用設計する必要があります。
また、いずれの方式でも共通して重要なのが、「光源とQRコードの相互作用の理解」です。QRコードに対して真上から強い照明が当たると反射してカメラが読み取れなくなるケースが多いため、光源の位置や拡散板などを工夫することで精度が格段に向上します。
AGVの誤作動を防げ|QRコード誘導トラブルの実例と対応策
QRコード誘導は非常に明快な仕組みである一方で、「物理的マーカーを正確に視認する」というシンプルゆえの脆弱さも抱えています。以下は、実際の現場で頻出するトラブル原因とその対応策を整理した一覧表です。
問題カテゴリ | 主な原因例 | 現場での対策例 |
---|---|---|
コード劣化・破損 | 剥がれ・印刷不良・摩耗 | 耐久素材の使用・定期点検 |
貼付ミス | 斜め貼付・浮き・段差の影響 | 専用治具を用いた正確な施工 |
照明の影響 | 光沢素材による反射・影 | マット調QR使用・照明拡散調整 |
カメラ側の問題 | レンズ汚れ・焦点ズレ・振動によるズレ | 定期メンテナンスと点検ルール整備 |
この表が示すように、QRコードの読み取り精度を保つには、施工面・素材選定・照明環境・機器整備のすべてにおいて“地味だけれど確実な管理”が必要です。
たとえば、「摩耗によるコード劣化」は目視では気づきにくく、印刷品質の微細な欠損がAGVの誤動作を誘発します。このような問題に対応するためには、耐候性に優れた素材(ラミネート加工、UVインクなど)を選定し、定期点検のタイミングでQRコードの貼り替え基準を明文化しておくと効果的です。
また、「照明による反射問題」は現場によって大きく差が出る要素で、自然光が入る現場や光沢のある床材では特に注意が必要です。光を拡散させる照明器具への変更や、QRコード自体をマット調に加工することで、大幅な改善が期待できます。
カメラ側の問題に関しても、「定期清掃と点検体制の整備」が基本です。レンズがほんの少し汚れているだけでも、読み取り精度に明確な影響が出るため、日常点検ルーチンに「レンズ清掃」「角度確認」「振動緩衝の固定チェック」を組み込むことを推奨します。
以上のように、QRコード読み取りの安定性は「設計・施工・運用・保守」のすべてが噛み合って初めて成立するものであり、特定の要素だけを改善しても根本的な解決にはなりません。
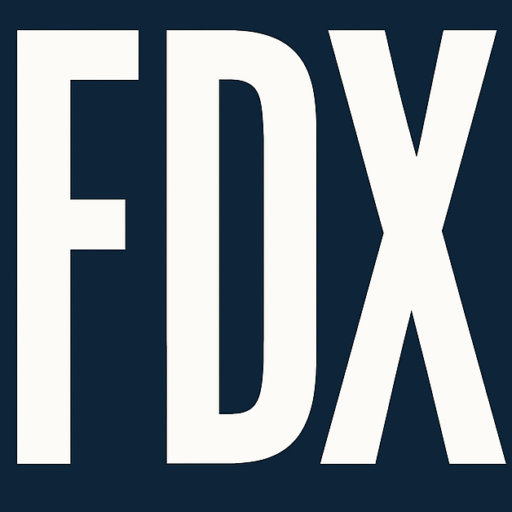
Factory DX
運営事務局
とくに中小製造業の現場では、人員や時間の制約がある中でも、こうした基本動作をいかに“仕組み化”できるかが成功の分かれ道です。
今後の導入・運用に向けて、チェックリスト形式の点検帳票などを整備しておくことも、実効性ある施策といえるでしょう。
AGV運用の失敗から学ぶ|QR誘導トラブルの実例と再発防止策
QRコード誘導はシンプルな仕組みですが、その運用には精密さが求められます。現場では「思わぬ要因」でAGVが停止・逸脱するケースが多く報告されており、それらの背景には「施工精度のわずかなズレ」や「光環境の変化」など、見逃しがちな原因が潜んでいます。以下では、実際の現場で発生した2つの典型的なトラブル事例とその対応策を紹介します。
トラブル事例1:QRコードの貼付角度のズレ
ある製造工場で、AGVが毎回同じ箇所でコースを外れてしまうという不具合が発生しました。現場の初期判断では「機体側の故障では?」と疑われましたが、詳細な調査により、実際の原因は「QRコードがごくわずかに斜めに貼付されていた」ことでした。
QRコードの角度ズレは数度程度であっても、AGVの進行方向に対して微妙な誤認識を招き、積み重ねによって走行精度に大きな影響を及ぼします。特に進行方向に対して角度が異なると、カメラが読み取るタイミングや補正ロジックが乱れ、コース逸脱が発生しやすくなります。
この現場では、専用の貼付テンプレート(貼り治具)を導入し、QRコードの設置精度をミリ単位で管理。以降、同様のトラブルは再発していません。
トラブル事例2:照明の反射による読み取り不能
別の物流倉庫では、AGVが特定のエリアで必ず停止してしまうという問題が発生しました。故障ではなく、原因は「そのエリアの床材が光沢仕上げ」であったこと。そして、天井照明がQRコードに強く反射していたため、カメラが読み取りエラーを起こしていたのです。
対策として、該当エリアの照明配置を変更し、光がコードに直射しないよう調整。さらに、QRコード素材をマット調に変更したことで反射を抑え、問題は完全に解消されました。
トラブル発生時の対応フローチャート
AGVが突然停止・逸脱したとき、現場が冷静かつ迅速に対応するためには「確認の流れ」が明確であることが不可欠です。以下はその基本的なフローです。
トラブル発生
↓
QRコード確認(剥がれ・汚れ・傾き)
↓(問題なし)
カメラ確認(レンズ・取付角度)
↓(問題なし)
照明確認(反射・影の発生有無)
↓(原因特定)
現場修正・再発防止策導入
このフロー図は、現場対応の標準手順を明確化したものであり、トラブルの初動対応における“迷い”や“属人化”を防ぐために有効です。QRコード貼付の状態や読み取り角度、カメラの固定や清掃状況、そして照明環境といった「AGV精度に影響する全要素」を段階的に確認できる構成になっています。
特に再発防止策の導入には、点検チェックリストの作成や定期確認ルーチンの仕組み化が有効です。
AGVの安定稼働に欠かせない|QRコード誘導を成功させる3つの要点
QRコード誘導の本質的な難しさは、「技術的に簡単であるほど、人的ミスや見落としが精度を左右する」点にあります。だからこそ、現場導入時に以下の3つの視点を確実に押さえることが、成功と失敗を分ける重要なポイントになります。
- 設計段階での導線計画と貼付位置の精査
AGVがスムーズに走行するには、QRコードの貼付位置だけでなく、施設内の導線全体を踏まえたレイアウト設計が求められます。事前に現場マップ上でAGVの通過ルート、旋回ポイント、停止位置を明示し、貼付テンプレートとセットで運用設計することが理想です。
- 現場環境(照明・床材)との整合性確認
床材の反射性、照明の角度、日照の入り方など、読み取り環境に影響を与える要素を事前にチェックし、必要に応じて照明器具やQR素材を変更する対応が必要です。とくに季節や時間帯によって自然光の入り方が変わる現場では、照度の変化による読み取り精度のばらつきを見落とさないようにします。
- 導入後の点検体制とトラブル対応フローの整備
QRコード貼付後も、AGVが継続的に安定稼働するには、点検体制の確立が不可欠です。貼付状態・コード劣化・カメラのズレなどを定期的に確認し、対応の属人化を防ぐチェックリストの整備、トラブル発生時の対応フローの文書化を推奨します。
AGV誘導方式の選定フローチャート(簡易版)
最後に、自社の現場にとって最適なAGV誘導方式が何かを簡易的に判断するためのチャートを紹介します。
Q1. 現場の経路は頻繁に変更される?
├─ はい → Q2
└─ いいえ → 磁気誘導が候補
Q2. 高精度・自己位置推定が必要?
├─ はい → SLAM方式
└─ いいえ → QRコード誘導
このチャートは「運用柔軟性」と「精度要求」を2軸で判断する設計です。頻繁なレイアウト変更が求められる現場にはQRコード誘導が適しており、一方で高精度な動作が必要な場合はSLAMが候補となります。既存の設備改修が難しく、コストを抑えたい中小規模現場にはQR誘導が最も現実的な選択肢となるでしょう。
このように、トラブルの実例と対応策を通じて現場での“気づき”を促し、導入・運用フェーズごとのチェックポイントを押さえておくことが、AGVの安定稼働に直結します。シンプルな技術だからこそ、「ミスを起こさない設計・運用体制」の構築が最大の差別化要素となるのです。
QRコード誘導で失敗しないために|AGV導入の実践ポイント総まとめ
QRコード誘導方式は、その表面的なシンプルさから「床にコードを貼ればすぐにAGVが動く」という誤解を招きやすい技術です。実際、初期導入時には「意外とすぐに動いた」と感じるケースも少なくありません。
しかし、安定した長期運用を目指す際には、その“簡単さ”の裏側にある深い設計思想と緻密な施工・管理が求められます。
例えば、AGVの読み取りカメラがQRコードを正しく認識するためには、数ミリ単位の貼付精度が必要です。また、貼付したコードが光沢のある床で照明に反射して読めなくなる、あるいは埃や摩耗によって視認性が下がる、といった「物理環境の影響」も決して無視できません。
さらに、以下のような技術的な注意点が複合的に関係します。
- QRコードのサイズと印刷品質が適切であるか
- カメラの解像度・視野角がコード検出に適しているか
- コード間隔と読み取りタイミングの整合性があるか
- 環境照度や天井高など、読み取り条件に変動がないか
つまり、QRコード誘導とは「単なる走行指示の貼り付け」ではなく、「走行インフラの構築そのもの」なのです。
もしこれからQRコード誘導を検討している現場担当者がいれば、以下のステップで計画を進めることを推奨します。
- 導入前シミュレーションを徹底する
AGVが走行するルートを事前にマッピングし、QR貼付箇所、間隔、旋回位置などを仮設計した上で、実地テストを行う。 - 貼付精度と照明の管理をルール化する
テンプレートや治具を用いた貼付マニュアルを整備し、点検タイミングもルーティン化する。 - トラブル発生時の対応手順を明文化する
本記事内で紹介した「トラブル発生時の対応フローチャート」などを現場掲示し、属人化せず誰でも初動対応できる体制をつくる。
このように、「一見シンプルに見えるが、実際は運用設計力が問われる」というのがQRコード誘導の最大の特徴です。
裏を返せば、これらの基礎をきちんと押さえることで、中小規模の現場でも比較的低コストでAGV導入が可能となり、自動化による生産性向上を着実に実現できるという、非常に再現性の高い仕組みでもあります。
すなわち、QRコード誘導は「簡単に見えて、奥が深い」技術。そしてこの“奥深さ”を理解し、丁寧に向き合う現場こそが、AGV導入の恩恵を最大化できるのです。
AGV導入でつまずきやすいポイントを、具体的な失敗事例とともに解説。
よくある落とし穴とその回避策を、導入前にチェックできます。
「知らなかった」で後悔しないために、今のうちに確認しておきませんか?
→ よくある失敗と対策まとめ資料を無料ダウンロード