AGV(無人搬送車)を導入したのに、なぜか現場の混乱が減らない――そんな経験はありませんか?
「これで人手不足も解消されるはずだった」「もうミスは減ると思っていた」…そんな期待を込めて導入したAGVが、思ったように稼働してくれない。実は、それはあなたの現場だけではありません。
多くの現場で聞かれるのは、「急に止まって動かない」「小さな不具合で作業が止まる」「トラブル時に誰も対応できない」といった、導入後の“運用の壁”です。
これらの原因は、AGVの性能不足ではなく、導入後の保守・点検体制が整っていないことにあります。
どれだけ高性能なAGVでも、使い方を誤ればすぐに能力を発揮できなくなります。埃でセンサーが反応せず、ルートを見失い、バッテリーも気づかぬうちに劣化していく。人と同じように、日々の点検とケアがなければ“働き続けられる環境”は維持できません。
本記事では、「AGVを導入した後、本当に稼働させ続けるにはどうすればいいのか?」という視点から、最低限整えておくべき運用ルールや、実際に多くの企業がつまずいた事例をもとに、今日から現場で役立つ実践的なノウハウをお届けします。導入前よりも、導入“後”の体制こそが、AGVの価値を決める分岐点なのです。
AGVの安定稼働はここで決まる!保守・点検が現場にもたらす効果
AGV(無人搬送車)は高精度な技術で制御されている一方で、非常に繊細な機械でもあります。だからこそ、故障や誤作動が生じた際の影響は大きく、定期的な保守・点検が安定稼働には不可欠です。
AGVの内部構造やパーツの役割については、こちらの記事で詳しく解説しています。
以下では、なぜ点検体制が必要なのか、その背景とリスクを整理して解説します。
故障による稼働停止は“見えない損失”を生む
AGVが停止すれば、単に搬送が止まるだけでなく、業務全体が滞ります。代替作業員の手配、手作業への切り替え、納期遅延による信用リスクなど、現場には多大な負担がのしかかります。たった1時間の停止でも、物流拠点によっては数十万円〜百万円規模の損失が発生するケースも珍しくありません。
特に多い見落としは「短時間の停止の積み重ね」です。日々の数分の遅延が週単位・月単位で大きな非効率を生み、結果として生産性の低下や利益圧縮に直結します。
安全性確保は“点検体制”から始まる
AGVは人と同じ空間を走行することが多く、センサーや停止機構にわずかな異常があるだけでも作業者との接触リスクが高まります。特に倉庫・工場のように人と機械が混在する環境では、些細な不具合が重大事故を引き起こす引き金になります。
点検を「安全管理の一環」として捉え直すことで、労災の未然防止だけでなく、従業員の安心感の醸成にもつながります。
メーカー保証・サポートの適用条件に直結
多くのAGVメーカーでは、定期点検が保証対応の前提条件とされています。記録がなかったり、推奨される頻度で点検が行われていなかった場合、「ユーザー過失」として有償対応になることもあります。
また、故障時にリモートサポートを受ける場合も、最新の点検記録がないと状況把握に時間がかかり、復旧が大幅に遅れることになります。
AGV保守・点検が機能しないことで生じるリスクの連鎖
AGVの軽微な不具合
↓
発見が遅れる
↓
誤動作・異常停止
↓
作業遅延・手配コスト増加
↓
納期遅延・顧客対応
↓
信頼低下・収益損失
このように、最初の段階で適切な点検と記録がされていないと、結果的に企業全体の信頼と利益に悪影響を及ぼします。運用負荷の軽減を目的に導入したAGVが、逆にリスク要因となってしまうのです。
AGVがうまく動かない原因とは?導入後によくあるトラブル事例集
AGVは導入した時点で「完成」ではありません。むしろ本当の運用はそこから始まります。導入後の数週間〜数ヶ月の間にトラブルが頻発する企業も多く、その原因の多くは機械の性能不足ではなく“人と仕組みの準備不足”にあります。
以下に、実際に現場で多く発生している代表的なトラブル事例とその背景を紹介します。
ケース1:日々の汚れが蓄積し、誤動作につながる
AGVの走行部やセンサーは、想像以上に埃や汚れに敏感です。タイヤに異物が付着すれば走行が不安定になり、センサーが曇れば誤認識のリスクが高まります。とくに「清掃ルールが存在しない」「担当が曖昧」といった運用体制の甘さが蓄積し、数週間後には致命的な誤動作に至るケースもあります。
これは、日常点検の“未整備”が引き金となる典型例です。
AGVのセンサーが安全性にどのように関係するのかについては、こちらの記事でも詳しく解説しています。
ケース2:レイアウト変更後のSLAM精度が低下
工場や倉庫内のレイアウト変更は珍しいことではありません。しかし、SLAM(自己位置推定マップ)を利用しているAGVにとっては、環境の変化=ナビゲーション精度の低下に直結します。マップの更新を忘れる、またはそもそも更新方法を理解していない場合、AGVが誤った場所で停止したり、ルートを見失うトラブルが発生します。
これは「AGVに対する知識不足」と「情報の共有不足」が根本原因です。
ケース3:担当者の退職でノウハウが消える
AGVの運用が属人化していると、担当者が異動・退職した瞬間から現場は無力化します。点検フローや障害対応手順がマニュアル化されておらず、現場の誰も正確な対応ができなくなった結果、小さな異常が長期化し、稼働率が著しく低下するケースも珍しくありません。
これは「仕組み化されていない運用体制」の危うさを示す好例です。
AGV導入後の典型的トラブルパターンと原因の構造
次の表は、実際の現場でよく見られる典型的なトラブルと、それを引き起こす根本原因を整理したものです。自社の運用体制と照らし合わせながら、見直しポイントを確認してみてください。
現場でよくある状況 | 背景にある本質的な原因 |
---|---|
毎日の運用で誤動作が発生 | 清掃ルールが存在しない、または形骸化している |
SLAMが正しく機能しない | レイアウト変更後にマップの更新を実施していない |
異常発生時に誰も対処できない | マニュアル未整備、運用が属人化している |
このように、トラブルの「現象」だけを見て対応していては、根本的な改善にはつながりません。
事前にルールを作り、記録を残し、誰が見ても分かる形にしておくことが、安定運用の鍵です。
なお、AGVの機能拡張として注目されている協働ロボット搭載型の活用事例については、こちらの記事で詳しく解説しています。
AGVの点検・保守は何をどれくらい?頻度と実施内容を徹底整理
AGVを安定的に稼働させるためには、点検と保守を適切に分類し、それぞれに合った頻度と実施体制を整備することが不可欠です。全ての点検を一括で管理するのではなく、日常業務の中で行う「日常点検」と、専門的な知識が必要な「定期点検」とに役割を分けることで、効率的かつ現実的な保守体制が構築できます。
以下に、点検の分類と主な実施内容、実施者、頻度をまとめた表を示します。
AGV点検・保守の分類と主な特徴
点検種別 | 実施者 | 頻度 | 主な内容 |
---|---|---|---|
日常点検 | 現場オペレーター | 毎日(出庫前後) | 外観確認(タイヤの摩耗・異物付着)、バッテリー残量、異常ランプ・音の確認 |
定期点検 | メーカー・保守業者 | 月次・年次など | センサーキャリブレーション、部品交換、ソフトウェア更新、精密診断 |
この表は、点検項目の責任範囲と目的を明確にすることで、作業の属人化や確認漏れを防ぐ助けとなります。
日常点検の1つである、バッテリー点検の際に押さえておきたい種類ごとの特徴や劣化サインについては、こちらの記事で詳しく解説しています。
日常点検は、運用前後の5分程度で完了するシンプルな作業でありながら、AGVの誤作動や重大故障の予防に直結する重要なステップです。現場オペレーターが毎日実施することを前提とし、専用のチェックリストを用いて項目の抜け漏れを防ぐ運用体制が求められます。
一方、定期点検では、AGV内部の状態を把握する精密な診断や、経年劣化部品の交換、ファームウェアのアップデートなどを行います。これらは専門知識や専用機器を必要とするため、メーカーや保守業者に依頼するのが一般的です。特に、自己位置推定(SLAM)を活用するAGVでは、マップの再調整やセンサーの再キャリブレーションが不可欠です。
なお、点検頻度はAGVの使用頻度や設置環境(粉塵、湿度、温度など)により異なるため、自社の運用実態に即したプラン設計が重要です。
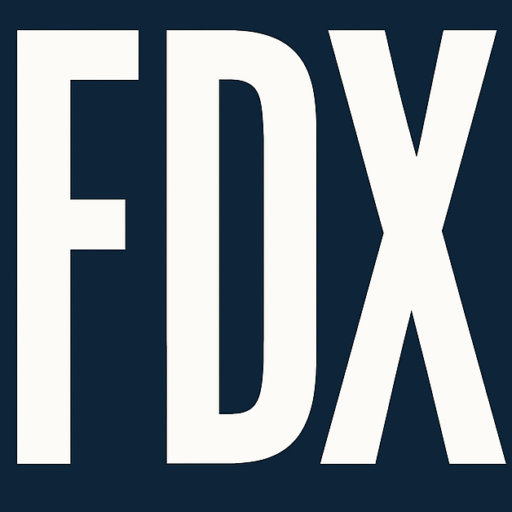
Factory DX
運営事務局
ただし、最低でも年1回はメーカーによる点検を受けることが、保証の維持やトラブルの早期発見につながります。
AGVが「止まらない」運用を実現するには、日常点検と定期点検の両輪が必要です。それぞれの役割と負荷を分けて設計することで、持続可能な点検体制を構築しましょう。
AGVの保守サービスはどこまで対応?種類と特徴を比較
AGVの安定運用を長期的に実現するには、自社対応だけでなく、外部の保守サービスを適切に活用することも欠かせません。とくに、トラブル発生時の迅速な対応や、高度なソフトウェア更新作業などは、メーカーやSIerの支援が不可欠です。以下に代表的な保守サービスの内容と特徴を整理しました。
AGVにおける代表的な保守サービスの比較
サービス内容 | 実施主体 | 頻度 | 備考 |
---|---|---|---|
緊急トラブル対応 | メーカー/代理店 | 随時 | 契約内容により即日〜翌日対応が可能 |
定期メンテナンス | メーカー | 月次/年次 | 点検内容・対応範囲は契約内容によって異なる |
ソフトウェア保守 | メーカー/SIer | 半年~年次 | SLAMの更新や設定最適化、ファームウェアアップデート等 |
教育サポート | メーカー/代理店 | 導入時/年1回 | 動画マニュアルの提供や集合研修などを含む |
この表は、保守契約を検討する際に重視すべきサービス内容と頻度を比較するためのベースになります。
緊急対応と定期点検は保守サービスの中核であり、とくに故障時の復旧スピードは業務全体に直結する重要なファクターです。対応速度は契約形態によって変動するため、自社の運用リスクに応じて柔軟に選定する必要があります。
また、ソフトウェア面の保守は見落とされがちですが、SLAMマップの更新や走行設定の最適化など、日々の精度や安全性に影響を及ぼす要素を含んでいます。定期的な更新を怠ることで、走行ミスや誤認識が発生するリスクが高まります。
教育サポートについては、新規導入時の定着や人員の入れ替え時に非常に有効です。とくに属人化の防止、現場での対応力向上には、継続的なマニュアル更新や研修体制の整備が不可欠です。
このように、各種サービスの特徴と自社ニーズを照らし合わせ、必要なサポートを過不足なく選定することが、長期的なAGV活用の鍵となります。
「こんなはずじゃなかった」を防ぐための、注意点を徹底的に洗い出しました。
見落としがちなポイントも、専門家の視点で丁寧に解説。
AGV導入前に必ず読んでおきたい実践的な資料です。
→ 失敗を避けるための注意点を今すぐ確認する
AGVを現場に根づかせるには?最低限整えておくべき運用ルール
AGV導入後の安定稼働は、製品の性能だけでは成立しません。
日々の運用を支える「ルール」と「習慣」の整備こそが、真の投資対効果(ROI)を高める鍵です。ここでは、社内で整備すべき基本的な運用ルールを、具体例とともに紹介します。
点検チェックリストの運用
日常点検は、担当者がその場で判断・対応するための最前線の仕組みです。ルール化されていないと、確認の質がばらつき、トラブルの早期発見が遅れる原因になります。チェックリストは、確認漏れを防ぎ、誰が・いつ・何を見たかを明確にする役割を果たします。
以下に、現場での運用にそのまま使える日常点検チェックリストの例を紹介します。
AGV日常点検チェックリスト(サンプル)
点検項目 | 内容 | 実施状況 | 備考・異常内容 | 点検者 | 日時 |
---|---|---|---|---|---|
外観確認 | 傷、異物付着、破損の有無 | □正常 □異常 | |||
タイヤ状態 | 摩耗、異物の巻き込み | □正常 □異常 | |||
センサーレンズ | 汚れ・破損の確認 | □正常 □異常 | |||
バッテリー残量 | 出庫前の残量確認 | □正常 □異常 | |||
異音確認 | 起動時・走行時の異音 | □正常 □異常 | |||
異常ランプ表示 | 表示の有無 | □正常 □異常 | |||
通信確認 | 管理システムとの接続状況 | □正常 □異常 |
このチェックリストは、点検内容を形式知化し、誰でも実施できるようにするための基本ツールです。記録欄を設けることで、異常傾向の追跡や、トラブル発生時の初動判断にも活用できます。
異常時の報告・対応フロー
トラブル発生時の対応が属人的になっていると、判断の遅れや連絡ミスにつながります。事前にフローを定義し、関係者間で共通理解を持つことが重要です。ポイントは、連絡経路を1本化し、現場掲示・フロー図化しておくことです。
例:現場担当者 → 上長 → メーカー連絡(連絡先一覧・契約ID付き)
これにより、異常発見から対応開始までの時間を最小化できます。
マニュアルと教育体制の整備
AGVに関する知識を一部の担当者に依存するのではなく、全体で共有可能な状態にする必要があります。動画とPDFを組み合わせたマニュアル、チェック表、フロー図などのビジュアル資料を用意することで、新入社員や派遣スタッフでも対応しやすくなります。
特に、操作ロックの解除方法や異常ランプの意味など、「現場で迷いやすいポイント」に対して図解で示すことが効果的です。
AGVを「誰でも安全に使える仕組み」にするためには、チェックリスト、報告フロー、マニュアルの三位一体での整備が不可欠です。
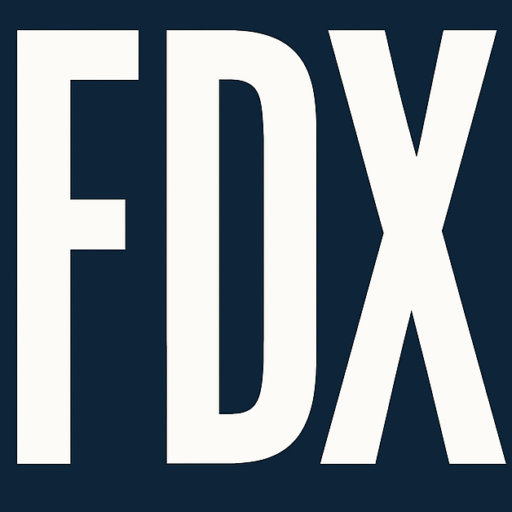
Factory DX
運営事務局
最初から完璧を目指すのではなく、必要最低限からでもまずは運用を可視化することが、事故や停止のない安定稼働の第一歩です。
AGVを少人数でも維持できる方法とは?ミニマム保守体制の実例
AGVの保守体制を整えると聞くと、「人手も予算も限られている中小企業には無理では?」という声が聞かれることがあります。しかし、すべてを完璧に揃えようとしなくても、最小限のリソースで安定稼働を実現する方法は十分に存在します。
実際、導入初期から大規模な体制を整備するよりも、小さく始めて運用に合わせて拡張していくアプローチの方が、無理なく定着しやすい傾向にあります。以下に、現実的な体制の構成要素とポイントを整理したテーブルを紹介します。
中小企業に適したミニマム保守体制の基本構成
項目 | 推奨内容 |
---|---|
担当者 | 1名(他業務と兼任でも可) |
点検頻度 | 毎日5分の簡易点検+月1回の点検 |
外部サポート | 年1回の契約(SLAM更新、ファームウェア整備など) |
予備部品 | タイヤ、バッテリーのみ事前にストック |
この構成は、初期導入の現場でもすぐに着手でき、必要に応じて段階的に拡張できる柔軟な運用モデルです。
日常点検は、現場作業の一部としてルーチン化することで負担を最小限に抑えられます。チェックリストを活用すれば、作業者が交代しても品質を一定に保つことが可能です。
また、年1回の外部点検契約を活用することで、SLAMマップの更新やセンサー調整といった専門性の高い作業を確実にカバーできます。これにより、突発的な精度低下や誤作動のリスクを抑えられます。
予備部品の確保も重要です。とくに摩耗しやすいタイヤや劣化しやすいバッテリーだけでも備えておけば、トラブル時の対応スピードが大きく向上します。
大切なのは、完璧な体制ではなく、「止めない仕組み」を小さく始めて育てていくことです。必要最低限から始めても、AGVを長く安定して活用することは十分に可能です。
AGVトラブル発生!現場で迷わないための対応手順まとめ
AGVは日々の点検を行っていても、突発的な異常やトラブルが完全にゼロになるわけではありません。重要なのは、「発生した異常に対して誰が、いつ、どのように対応するか」が現場で明確になっているかどうかです。
属人的な判断に任せてしまうと対応が遅れ、被害や損失が拡大する可能性があります。そこで、あらかじめ標準対応フローを定め、誰でも即時に行動できる仕組みを整えておくことが必要です。
AGV異常時の標準対応フロー
1. AGVが異常停止
↓
2. 現場担当者が現物を確認
- 異常ランプの点灯有無
- 異音の有無
- 表示エラーや挙動の異常
↓
3. エラーコードや状態ログを記録
- 画面表示の撮影
- 管理表へのメモ
↓
4. マニュアル・チェック表を参照し、初期対応が可能か判断
├─ Yes:
│ 5. リセット・清掃などの初期対応を実施
│ 6. 点検記録に入力して終了
└─ No:
5. メーカー・代理店に連絡(連絡先一覧を参照)
6. 現場で状況を説明し、修理・交換の判断を仰ぐ
このフローは、現場対応のスピードと正確性を高めるための標準プロセスです。印刷してAGVステーション付近に掲示すれば、誰が対応しても同じ手順で処理できます。
異常が発生した場合、どのような内容を記録に残すかも重要です。対応履歴は、再発防止策の検討やメーカーとの情報共有にも役立ちます。記録すべき項目を明確にし、漏れなく記入できるテンプレートを準備しておきましょう。
AGV異常時対応記録テンプレート(記入例付き)
項目 | 内容記入欄例 |
---|---|
異常発生日時 | 2025/04/03 10:42 |
発見者名 | 山田 太郎 |
発生場所 | 第2搬送ライン・東側 |
AGV機種・ID | AGV-100SL / ID: 0021 |
異常内容 | 停止位置が大幅にずれる。SLAMマップ読み取りエラー |
エラーコード | E-1052 |
初期対応の有無 | □あり(リセット・センサー清掃) / □なし |
メーカー連絡 | □実施済(日時:/担当者:/対応先:) |
対応結果・備考 | センサー清掃で復旧。マップ更新を依頼予定 |
このテンプレートは、現場での異常発見から報告・復旧までを一貫して記録するためのツールです。書式を統一することで、トラブルの傾向分析や引き継ぎもスムーズに行えるようになります。
異常発生時の対応力は、運用の成熟度を測るバロメーターでもあります。標準フローと記録体制を整備することで、誰が対応しても同じ品質を保つことができ、トラブルの早期解決と再発防止につながります。
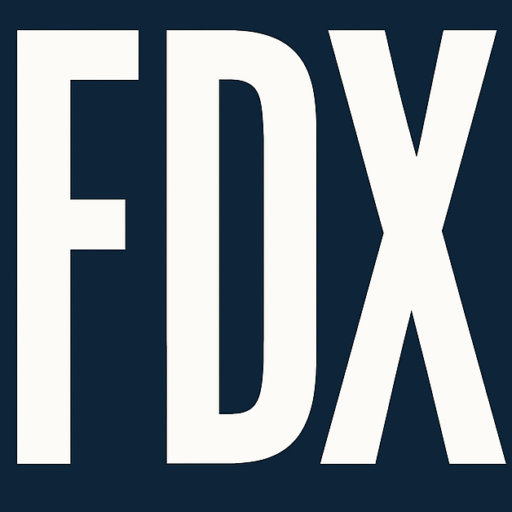
Factory DX
運営事務局
中小企業であっても、仕組みで補える部分を整えることがAGV活用の安定稼働に直結します。
AGV保守・点検に関するよくある質問【導入後の悩みを事前に解消】
- AGVの日常点検は誰がどのくらいの頻度でやるべき?
基本的には現場オペレーターが「毎日、稼働前後」に実施するのが理想です。タイヤの異物確認、バッテリー残量、センサーの汚れチェックなど、5分以内で終わる簡易点検で十分効果があります。
- 定期点検はどのくらいの頻度で必要?
一般的には「月1回〜年1回」が目安です。使用環境や走行時間によって最適な間隔は異なりますが、少なくとも年1回はメーカーまたは認定業者による診断を受けることで、重大故障の予防につながります。
- 保守契約は結んだ方がいい?それとも自社対応で十分?
高頻度で稼働するAGVや、自己位置推定(SLAM)など高機能型を導入している場合は、保守契約を推奨します。突発トラブルへの即時対応や、定期的なファームウェア更新などは社内だけでは限界があります。
- バッテリーの寿命はどのくらい?劣化を見抜くポイントは?
一般的に約3年が目安ですが、充電サイクルや温度環境により前後します。持続時間の急減や満充電後の電圧低下が見られたら、交換検討のサインです。
- SLAM方式のAGVはレイアウト変更後もそのまま使える?
いいえ。SLAM方式ではレイアウトの変更=地図の再構築が必須です。変更後にマップ更新を行わないと、誤動作やルート逸脱が発生しやすくなります。
- AGVの点検記録はどこまで詳細に残すべき?フォーマットはある?
点検日時・担当者・異常の有無・簡単なコメントを残す程度で十分ですが、エラーコードや写真付きで残すとトラブル分析に非常に有効です。自社仕様のチェックリストをEXCELやGoogleフォームで運用する企業も増えています。
- 雨天対応のAGVでも、センサーが濡れると誤動作する?
はい。IP等級が高くても、センサー部分に水滴が付着すると誤認識を起こす可能性があります。特にLiDARや超音波センサーは水に弱いため、雨天後の拭き取り・乾燥が推奨されます。
- バンパースイッチって実はほとんど作動しないって本当?
事実です。バンパースイッチは「最終手段」の安全装置であり、通常はセンサーによる検知で停止するのが基本。バンパースイッチに依存する設計は、むしろ安全リスクを高めます。
- AGVのファームウェア更新って何をしてるの?自分でできる?
SLAM地図の最適化、制御ソフトのバグ修正、バッテリー管理の調整などが行われますが、誤設定は致命的な誤作動を引き起こすため、原則はメーカーまたはSIerに依頼すべきです。
- 導入から2年以上経つと、初期トラブルより“運用疲労”が起きやすくなるって本当?
はい。「仕組みが形骸化してくる」「担当者が異動する」「ルートが徐々に変化している」といった“ゆるやかなズレ”が蓄積し、2〜3年目以降にエラーや不具合が増える傾向があります。定期的な“運用レビュー”が長寿命化の鍵です。
まとめ|AGVを止めない現場が実践する運用と保守の基本
AGVを導入すること自体は、課題解決のスタート地点に過ぎません。ROI(投資対効果)を最大化し、長期間にわたって安定稼働を実現するために最も重要なのは、「日々の運用体制」と「現場での習慣化」です。
とくに中小企業では、限られた人員と予算の中でAGVを管理しなければならないことがほとんどです。しかし、それを理由に品質管理を諦める必要はありません。大切なのは、いまの体制でできる最小限から始めて、継続的に改善していく視点を持つことです。
AGVの導入前から本格運用までの全体像を理解したい方は、以下の記事もあわせてご覧ください。
では、実際にどのような運用姿勢がAGVの寿命を延ばすのでしょうか?以下に、その要点をまとめました。
AGV運用の成熟度と継続改善のサイクル
[導入初期]
↓
点検ルール・報告体制を最小単位で設計(人・仕組み)
↓
運用に慣れながら記録・フィードバックを蓄積
↓
異常・改善要望に応じてチェック項目や対応フローを更新
↓
教育・マニュアルの整備 → 属人化の排除
↓
[安定稼働・長期運用へ]
このサイクルを現場に定着させることができれば、トラブルの早期発見と対応精度が高まり、結果としてAGV自体の寿命や性能も最大限に活かされることになります。
AGV運用の本質は、高額な設備を「止めない仕組み」を社内に構築できるかどうかです。完璧な体制でスタートする必要はありません。むしろ、トラブルや改善を経験しながら自社に最適な運用ルールを作り上げていく「実践知」こそが、最強の運用資産になります。
導入後の運用力がAGVの価値を決める――その認識こそが、他社との差別化を生み出す最大のポイントです。
初めてのAGV導入で多いトラブルと、その予防策をわかりやすく解説しています。
現場の声をもとにまとめたチェックリストで、抜け漏れを防ぎましょう。
事前に読んでおくことで、後悔のない選定が可能になります。
→ トラブル防止マニュアルをPDFで確認する