「AGVの導入が思ったようにうまくいかない」
「現場から使われず、結局放置されてしまった」
「業者の提案通りに進めたはずなのに、なぜ?」
こうした声は、決して珍しいものではありません。むしろ、AGVを初めて導入する企業の多くが、同じ壁にぶつかっています。その原因は、AGVそのものの性能ではなく、導入前の準備と設計の“詰めの甘さ”にあるケースが大半です。
現場の導線、作業内容、スタッフの心理、保守体制までを加味した設計ができていなければ、どんなに高性能なAGVでも現場には定着しません。そして一度“失敗した導入事例”になってしまうと、社内の信用は回復しづらく、次の自動化プロジェクトにもブレーキがかかります。
この記事では、「なぜ失敗するのか」「どうすれば失敗を防げるのか」を、実際の現場課題に即した視点で、具体的かつ実務的に解説します。読まずに進めてしまうことの方が、はるかにリスクです。導入前の今こそ、立ち止まって“つまずきやすいポイント”を確認しておきましょう。
AGV導入で最も多い3つの失敗パターン|構造的ミスと対策ポイントを解説
AGVの導入は、設備投資というより“現場の再構築”に近い性質を持ちます。実際には、システムそのものではなく「導入の仕方」にこそ大きなリスクが潜んでいます。
本セクションでは、よくある失敗を3つに分類し、それぞれの背景・実態・解決の糸口を明確にします。ここで紹介する失敗事例は、実務で頻発するリアルな課題ばかり。「まさに自分の会社で起こりうる」ケースですので、事例の背景や回避策まで丁寧に掘り下げます。
失敗例1:目的が曖昧なままプロジェクトが走り出す
多くの企業で見られるのが「人手不足だから自動化を」という抽象的な理由だけでAGVを導入してしまうパターンです。現場課題の本質を明らかにせずにシステムを導入すると、目的と成果の乖離が起こり、導入後に「何のためのAGVか」が誰にもわからなくなってしまいます。
具体例として、作業のボトルネックが別工程にあったにも関わらず、搬送工程の自動化を進めてしまい、結果として効率が逆に悪化したケースがあります。これでは「設備導入=改善」ではなく「設備導入=混乱」となりかねません。
失敗例2:現場とのミスマッチに気づかず設置後に苦しむ
AGVは机上のロジックだけで導入できるものではありません。段差、狭小スペース、可動ラック、作業員との交差、照明条件など、物理環境が想定と少しでも違えば、その影響は大きく出ます。
たとえば、実際に導入してみたところ「通路の幅が足りず、AGVが旋回できなかった」という事例は珍しくありません。これは、現場調査を営業資料やカタログ値だけで済ませた結果です。後からルート変更やレイアウト改修が必要になれば、コストは一気に跳ね上がります。
失敗例3:現場作業者とシステム導入側の認識がズレたまま進行
最も見落とされがちなのが「人の理解と納得を得るプロセス」です。導入を決定した情報システム部門と、実際に使う現場作業者の間で認識の共有がないと、どんなに優れたAGVでも活用されません。
「ある日突然、何の説明もなくAGVが動き始めた」という現場の声が象徴的です。作業者から見れば、“動く障害物”にしか見えず、むしろ生産性が下がったと感じることさえあります。これを避けるには、導入前から現場を巻き込んだトライアルや教育の場を設け、「導入される側が主体的に理解できるプロセス設計」が不可欠です。
AGV導入における失敗パターンの因果構造
以下の表は、典型的な失敗パターンがどのように連鎖し、最終的な“AGV不活用”へとつながっていくかを視覚的に整理したものです。
失敗タイプ | 初期要因 | 中間結果 | 最終結果 |
---|---|---|---|
目的不明確 | 導入目的が曖昧 | 誤った課題設定により現場が納得せず協力を得られない | AGVが使われず、期待された成果が出ない |
現場未調査 | 通路・段差・搬送物など現場条件の未確認 | スペックと現場環境が合わず動作不良 | 改修コストが膨らみ、ROIが悪化 |
部門乖離 | 情報システム部門と現場の認識ズレ | 操作教育不足・現場の不安感増大 | 作業者がAGVを避け、定着しない |
補足説明
この表からも分かる通り、AGV導入における失敗は単独ではなく、複数の因果関係が連鎖する「構造的失敗」として発生します。初期段階での目的設定と現場調整の不備が、その後の工程すべてに影響を与えるため、最初の一歩を誤らないことが極めて重要です。
実践現場で聞いた「導入が頓挫した生の声」
国内のある物流センターでは、AGVの動作テストにすら進めないままプロジェクトが中止となりました。理由は、作業員が「AGVの存在に心理的ストレスを感じている」というアンケート結果です。設置場所や稼働音が作業に与える心理的負荷を想定しておらず、定着以前の段階で現場が拒否反応を示したのです。
これは、「物理的な安全性」と「心理的な安心感」は別であることを示しています。
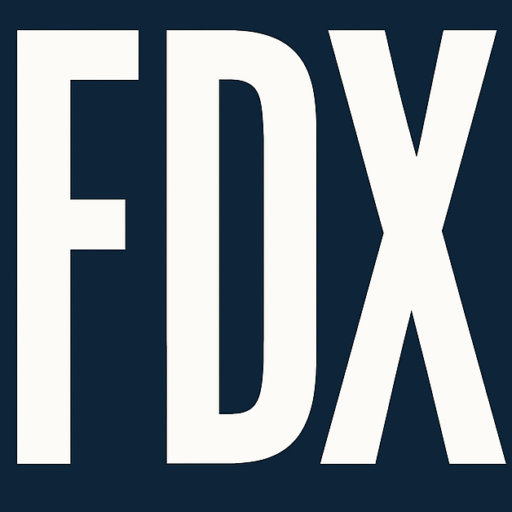
Factory DX
運営事務局
導入前に行うべきは、安全装置やセンサー性能の説明ではなく、作業員の“感情への配慮”を伴う対話的なコミュニケーションです。
導入失敗は“現場で起きる”のではなく“計画で始まる”
AGV導入に失敗した企業の大半は、「動かしてから問題に気づいた」のではなく、「動かす前に見落とされていた兆候があった」というのが実態です。
本記事を読んでいる段階であれば、まだ間に合います。
PoCの有無、現場の参加度、稟議文書の粒度を見直すだけでも、プロジェクトの成功率は2倍以上変わる──これは、複数の導入企業から得られた実務現場での経験則です。
AGV導入成功は“問いの質”にある|今すぐ見直すべき5つの準備項目
AGV導入に失敗する企業の多くは、「動かしてから考える」という姿勢でプロジェクトを進めています。しかし、実際に成果が出ている企業は、導入前に極めて高い精度で“現場との整合性”や“社内の納得感”を確保しています。
そのために有効なのが、自己評価による事前チェックです。
導入プロジェクトが動き出す前に、自社の準備状況を冷静に振り返るためのチェックリストを以下にご紹介します。これはただの形式的な確認ではなく、「導入後の現場混乱やROI低下を未然に防ぐ」ための実践的な評価基準です。
【チェックリスト】AGV導入前に確認すべき5項目
チェック項目 | 確認 |
---|---|
AGV導入の目的が明確か | □ Yes / □ No |
現場環境や業務フローの分析は完了しているか | □ Yes / □ No |
導入コストやROIの試算が行われているか | □ Yes / □ No |
現場作業者の理解と協力体制があるか | □ Yes / □ No |
操作マニュアルや教育資料の準備ができているか | □ Yes / □ No |
補足説明
このチェックリストは、導入準備の「抜け・漏れ」に気付くためのシンプルかつ強力なツールです。たとえば、目的が不明確なまま進めると、現場の協力が得られず定着しません。ROI計算が曖昧であれば、稟議が通っても経営陣の信頼を損なうリスクがあります。
なお、AGV導入におけるROIを高めるための実践的な戦略については、こちらの記事でも詳しく解説しています。
チェック項目に1つでも「No」があれば、そのポイントに対して計画を見直す必要があります。導入に失敗した企業の多くは、このような「基本確認の欠落」が最終的な運用不全につながっています。
なぜ「目的の明確化」がすべての起点になるのか
実際の事例では、同じAGVシステムを導入しても、「人手不足対策」として捉えた企業は運用に成功し、「最新技術を入れてみたかった」という企業は途中で頓挫しています。
違いは、“現場の困りごと”を具体的に把握していたかどうかにあります。
たとえば、「ピッキングエリアまでの距離が長く、スタッフの歩数が1日10,000歩を超えている」という定量的なデータがあれば、AGV導入によって「どれだけ削減できるか」を予測可能です。こうした数値的根拠が、経営判断の後押しにも、現場の納得にも直結します。
AGV導入の成否は、機器性能よりも準備段階の「問いの深さ」で決まります。このチェックリストを活用し、「まだ見えていない盲点はないか?」を確認することが、成功導入への最短ルートです。プロジェクトを本格始動させる前に、ぜひ一度立ち止まり、冷静に自社を評価してみてください。
また、自社での導入を失敗させないためには、検討から稟議・導入フェーズまでの全体像をあらかじめ理解しておくことが重要です。詳しくは以下の記事をご覧ください。
AGV導入の失敗は「1つのミス」じゃなく「連鎖する準備不足」から始まる
AGV導入がうまくいかない企業の多くは、失敗の原因を「技術選定ミス」や「操作習熟不足」といった“個別の問題”として捉えがちです。しかし、現実の失敗はもっと複雑で、導入の意思決定から現場運用に至るまでの各プロセスで起こる“複合的な連鎖”によって発生しています。
たとえば「AGVが動かない」という現象の背後には、目的の曖昧さ → 設計不備 → トライアル不足 → 運用混乱…というように、複数の課題が段階的に積み上がっているケースがほとんどです。こうした構造的失敗を未然に防ぐには、全体の因果関係を視覚的に把握しておく必要があります。
AGV導入失敗の構造的な連鎖モデル
以下は、AGV導入時によく見られる失敗の因果構造を図解した表です。各フェーズでの判断ミスや準備不足が、いかに次工程のトラブルへと波及していくかが一目で分かります。
AGV導入プロセス | 初期課題 | 中間障害 | 最終的な失敗結果 |
---|---|---|---|
導入目的の設定 | 目的が曖昧で評価軸が不在 | 成果指標が定まらず、現場が納得できない | AGVが使われず、投資対効果が出ない |
現場環境の把握 | 現地調査不足・通路や段差の見落とし | スペックと現場が不一致 | 走行不能・改修費用の増加 |
社内連携体制 | 部門間の情報共有が不足 | 操作手順やトラブル対応が現場に伝わらない | 作業者がAGVを避け、定着しない |
設計・検証工程 | PoC未実施・フリート構成未検討 | 複数台の渋滞・誤動作が発生 | 導入後の生産性が低下 |
保守・運用計画 | 維持管理体制が曖昧 | 故障対応が遅れ、業務停止 | AGVへの信頼低下と使用中止 |
補足説明
この表は、AGV導入における失敗が“どこで起きているか”ではなく、“どのように連鎖していくか”を明確に示すものです。AGVというテクノロジーを導入するだけで現場が変わるわけではなく、そこに至るまでの目的設計・環境整備・社内巻き込み・保守体制といった周辺構造の整合性が求められます。
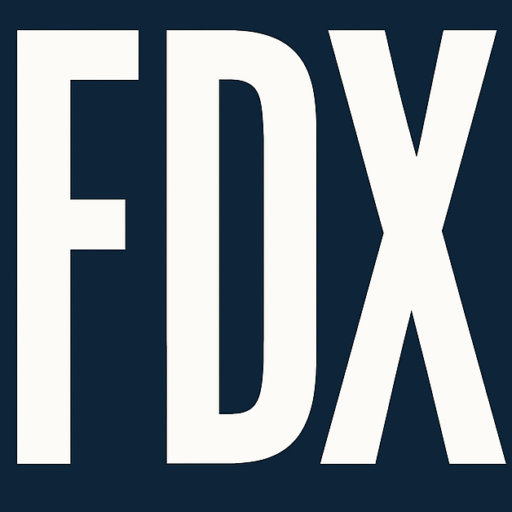
Factory DX
運営事務局
多くの失敗企業は、「AGVが悪かった」と技術要因に責任を押し付けてしまいますが、実際には“導入までの道筋そのもの”が失敗の原因であることを、この表が明らかにしています。
AGV導入に必要なのは技術力よりも“社内の整合性”という現実
AGV導入の初期段階でよく見落とされるのが「社内における費用負担部署の不明確さ」です。導入費は設備費に分類されることが多いですが、AGVの場合、ITインフラや保守契約も絡むため、総務・情報システム・生産技術など複数部門が関与します。
この役割分担があいまいなまま導入を始めると、「誰が主導するのか」「どこに費用計上するのか」といった意思決定のボトルネックが発生しやすくなります。結果、計画の初期段階で曖昧なまま進行し、プロジェクトが形骸化するリスクが高まるのです。
本セクションで理解すべき最重要ポイントは、「導入失敗は1つの問題から始まるのではなく、複数の“未整備な点”が連動して破綻を招く」という事実です。だからこそ、「設計・人・現場」の全体を俯瞰して整合性を確認することが、失敗しないAGV導入の必須条件となるのです。
最適なAGVを選ぶには、現場の用途や課題に合わせた比較軸が重要です。
導入成功企業が重視したポイントやチェックリストを1冊にまとめました。
検討初期で迷いがちな方は、今のうちに情報を整理しておきましょう。
→ 選定チェックリスト付きガイドを無料ダウンロード
AGV導入の勝ちパターン|成果を出す企業が外さない準備の鉄則3つ
AGVを導入しても成果が出る企業と、そうでない企業の差は、製品選定ではなく導入前の準備プロセスの深さと広さにあります。本セクションでは、成功企業に共通する要素を3つの視点から整理し、「自社にもできる具体行動」として取り組める内容に落とし込みます。
1. 課題の明確化:「なぜAGVが必要なのか?」に具体的な答えがある
成功企業では、AGV導入を「トレンドだから」「自動化が進んでいるから」ではなく、定量的・定性的な現場課題に基づいて判断しています。
たとえば、
- 慢性的な人手不足で、夜間や繁忙期に対応できない
- フォークリフト要員が退職し、安全性と作業負荷が懸念されている
- ピーク時に応援人員を割く搬送作業が非効率
- 長距離搬送で1日あたり数時間のロスが発生している
これらの課題を具体化すれば、AGV導入によって「何がどう改善されるべきか」の目標が明確になります。このように課題と解決策がリンクすれば、現場の理解も得やすく、ROIの設計も可能になります。
2. 現場データに基づく詳細分析:「そのAGV、本当に通れますか?」
成功企業は、AGVの選定において現場仕様との整合性を最優先しています。カタログスペックや営業資料だけで判断するのではなく、以下のような現場情報を「図面・実測値・動画記録」で可視化しています。
- 通路幅、曲がり角、傾斜、床材などのレイアウト
- 搬送物のサイズ、重心、積み下ろし方法
- 作業者との交差ポイント、動線
- 騒音・照度・温湿度といった環境要因
AGVにとっては数cmの段差や角度が致命的になることもあります。また、床材によってはセンサーの反応に影響が出るケースも。現場の“あたりまえ”を数値で記録し、それを元に仕様を確定することが、導入後の「想定外」を回避する鍵です。
AGV導入前に確認すべき現場仕様のチェックポイント
導入企業の多くが見落としやすい現場の重要データ項目を以下に整理しました。これを確認することで「そのAGVが本当に使えるか」の判断精度が高まります。
チェック項目 | 内容例(実際の確認ポイント) |
---|---|
通路幅・曲がり角 | 最小回転半径が足りるか、通路が狭くないか |
床材・段差・傾斜 | 滑りやすさ、凹凸、勾配による走行不安定のリスク |
搬送物の形状・重量 | 重心のズレ、長尺物など特殊物対応の必要性 |
作業者の動線 | 人との交差が頻繁か、安全対策は取れるか |
騒音・照明・視認性 | センサー精度への影響、暗所・明所の差異 |
駐車・充電ステーション配置 | 設置場所のスペース、電源容量は十分か |
この表を使えば、AGV導入前に「現場に合うかどうか」を漏れなく可視化できます。
3. テストと段階的導入:「まず動かしてみる」の慎重さが成功率を上げる
いきなり10台導入するのではなく、スモールスタート(PoC)を設けるのが成功企業の常套手段です。
PoCフェーズでは、以下のようなことを検証します。
ここで問題点をあぶり出し、調整した上で本格導入に進むことで、定着率もトラブル回避率も大きく向上します。
「現場の納得感」を高めた企業の施策例
ある部品製造企業では、AGV導入に先立ち、工場内に仮想AGVルートをテープで貼り、作業者が一週間そのラインを通るよう促す「動線慣れ期間」を設けました。
この施策の目的は「物理的な導入」よりも「心理的な受け入れ準備」であり、結果として正式導入時には「違和感なく始まった」という現場の声が多く、運用定着までのスピードが他社より圧倒的に早かったと報告されています。
AGV導入における成功の分かれ目は、“動かす準備”をいかに本気で取り組めるかにあります。この記事を参考に、自社でも「なぜ必要か」「現場は受け入れられるか」「実際に動くか」を、今すぐ見直してみてください。失敗を回避するために必要なのは、高価な機械ではなく、“具体的な準備”なのです。
AGV導入は「買って終わり」じゃない|4つの導入フェーズでみる失敗の兆候
AGV導入の成否は、製品そのものよりも「導入プロセス」によって決まるケースが大半です。つまり、“何を買うか”ではなく、“どう導入するか”が問われます。では、その違いはどこで生まれるのでしょうか?
以下では、計画段階から定着フェーズに至るまでの各プロセスについて、成功と失敗の典型的な特徴を比較形式で整理しました。これを参考に、自社がどのフェーズにリスクを抱えているかを見極める視点を持つことができます。
AGV導入の成否を分ける4フェーズ別チェックリスト
導入フェーズ | 成功導入の特徴 | 失敗導入の特徴 |
---|---|---|
計画段階 | 導入目的が具体的で、現場課題に基づいた分析が行われている | 「自動化したい」など漠然とした理由で課題設定が曖昧 |
現場との連携 | 作業者を巻き込んだヒアリングやトライアルを事前に実施している | 経営層・情シスだけで進行し、現場が蚊帳の外になっている |
システム設計 | 作業フローやレイアウトに最適化されたAGV仕様を選定・カスタマイズ | カタログスペックを優先し、現場と仕様がミスマッチを起こしている |
運用・定着 | 操作説明・マニュアル整備・教育体制が構築されている | トラブル対応や操作説明が不十分で、現場がAGVを敬遠している |
補足説明
この表は、AGV導入における「成功企業が共通して行っていること」と、「失敗する企業にありがちな落とし穴」を対比形式で整理したものです。特に重要なのは、“現場の巻き込み”と“カスタマイズ設計”の有無。AGVは既存業務に適応するのではなく、業務プロセスに合わせて設計すべき設備です。
さらに、多くの企業が陥るのは「買って終わり」という感覚です。導入した瞬間がスタートラインであり、現場に浸透させるまでの教育・運用設計がなければ成果は出ません。
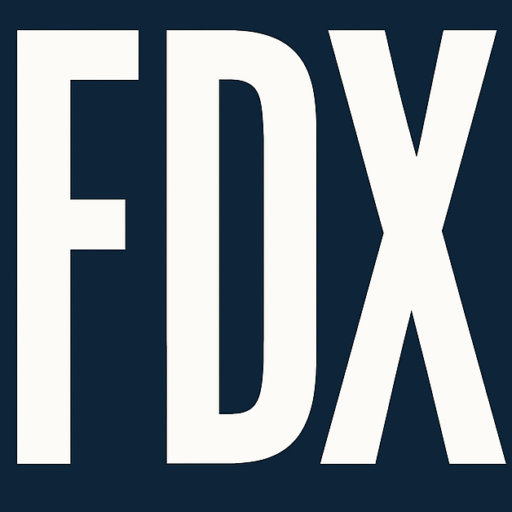
Factory DX
運営事務局
この点を明確に認識し、フェーズごとの注意点を社内で共有しておくことが、導入効果を最大化するポイントとなります。
現場ヒアリングで分かった「3つの誤解」
複数のAGV導入企業からヒアリングを行った際、以下のような“よくある誤解”が浮かび上がりました。
これらの“誤解”が解消されないまま導入を進めると、結果としてAGVが「高価なオブジェ」と化す可能性すらあります。表だけでなく、“なぜその状態になるのか”を現場目線で考えることが、真の成功には欠かせません。
先ほどの比較表と事例をもとに、自社の導入プロセスを振り返ってみてください。単なる設備導入ではなく、「現場を変えるプロジェクト」であるという認識を持てるかどうかが、成果を分ける第一歩です。今、どのフェーズで止まっているかを見極め、次の打ち手を明確にしていきましょう。
AGV導入前によくある質問と回答集|成功企業が押さえている10選
- AGVを導入するにあたって、最初に取り組むべきことは何ですか?
まずは「なぜAGVを導入するのか」という目的の明確化が最優先です。現場課題を洗い出し、人手不足の解消なのか搬送の効率化なのか、導入目的を定量・定性的に整理することで、その後の選定や設計がブレずに進みます。
- 工場や倉庫の広さが限られていても、AGVは導入可能ですか?
はい、可能です。導入の可否は面積の広さよりも、通路幅・曲がり角・交差点の設計など“動線条件”に依存します。狭小スペースでも、ルート設計を工夫すれば十分運用できます。
- AGVを導入したら、すぐに現場で使いこなせるようになるのですか?
現場への定着には準備期間が必要です。操作トレーニングやマニュアル整備、トライアル運用を1〜2週間ほど行うことで、作業者の理解と安心感が得られ、スムーズに運用へ移行できます。
- AGVの導入費用やランニングコストはどのくらいかかるものですか?
AGVの本体価格は、機能やサイズ、ナビゲーション方式によって大きく異なりますが、一般的には1台あたり100万〜700万円程度が目安です。
一方、年間のランニングコストには、バッテリーやタイヤの交換費用、定期保守点検、場合によってはソフトウェア更新や出張対応費用などが含まれます。
金額の目安としては、本体価格の約10%前後(年間10〜70万円程度)を想定すると、実態に近い予算計画が立てられます。
- AGV導入で失敗しやすいポイントにはどのようなものがありますか?
よくある失敗には「目的が不明確」「現場との情報共有不足」「現地環境との不一致」があります。これらは導入前に防げる問題が多く、特に現場を巻き込んだ導入計画が鍵となります。
- AGVのセンサーが誤作動を起こしやすい現場環境にはどのような特徴がありますか?
光の反射が強い金属床や直射日光が差し込む場所、粉塵の多い環境などは、レーザー・ビジョンセンサーの誤検知を引き起こす要因になります。導入前にセンサー方式と現場環境の整合性を確認することが重要です。
- 作業者がAGVに抵抗感を持ちやすいのはなぜですか?
AGVの動きが予測しづらく、ぶつかる・壊すという不安が心理的抵抗につながります。導入前に実機の走行デモや操作体験の場を設けることで、“共存への安心感”を醸成できます。
- AGV導入後の運用効率が想定より下がる要因には何がありますか?
AGV導入後にレイアウト変更や搬送物の仕様変更が行われると、当初設計が機能しなくなります。これを防ぐには、導入後も定期的に“運用レビュー”を行い、柔軟に対応できる設計体制を整えることが重要です。
- 複数台のAGVを運用する際に起こりがちなトラブルにはどのようなものがありますか?
FMS(フリートマネジメントシステム)が未整備だと、交差点での渋滞や衝突、待機優先順位の混乱が発生しやすくなります。走行ルールや台数ごとの制御設計が事前に必要です。
- 中小企業がAGVを導入する際、社内プロジェクト体制の構築において特に注意すべき点は何ですか?
各部門(製造、情シス、設備、安全衛生など)の責任分担が曖昧なままだと、導入後のトラブル時に「誰が判断し、誰が対応するか」が不明瞭になり、対応遅れの原因となります。RACIチャートなどを活用し、役割とフローを導入前に整理することが不可欠です。
まとめ|AGV導入の成否は「準備力」がすべてを決める
AGV(無人搬送車)の導入は単なる自動化設備の購入ではなく、「現場の業務そのものを再設計する」取り組みです。AGVが現場に馴染まなければ、最先端の機器であっても宝の持ち腐れになりかねません。
導入に成功している企業には、共通して以下の姿勢が見られます。
AGV導入に必要な準備要素の全体像
導入前に確認すべき準備項目を、戦略・環境・人・運用の4視点から表で整理しました。これらが揃ってはじめて、「現場に定着するAGV導入」が実現します。
視点分類 | 準備項目の主な内容 | 検討すべき具体項目 |
---|---|---|
戦略 | 導入目的と課題の整理 | ・なぜAGVを導入するのか ・誰のどの業務を改善するのか |
環境 | 物理条件と現場仕様の整備 | ・通路幅・段差・動線の確認 ・搬送物サイズ・重量・頻度 |
人 | 現場とのコミュニケーション設計 | ・現場ヒアリングとトライアル ・心理的ハードルの除去 |
運用 | 教育・保守を含む継続運用体制の構築 | ・マニュアル整備と定着支援 ・保守・改善のPDCA設計 |
この表は、AGV導入に必要な「準備の全体像」をフェーズごとに可視化したものです。よくある失敗の多くは、どれか1つでも抜け落ちていることが原因で起こります。特に、目的(①戦略)と人(③現場理解)に手を抜くと、いかに高機能なAGVでも現場で使われなくなってしまいます。
成功企業が「導入後にしていること」
AGVの導入自体はスタートに過ぎません。
ある製造業の事例では、「導入3か月後に現場からフィードバック会議を開き、AGVルートや走行タイミングを見直した結果、月間稼働率が60%→95%に向上した」という報告があります。
このように、「定着させたあとにどう改善していくか」までを見据えた導入計画こそが、AGV導入の本質的成功といえます。AGV導入は「買えば成功」ではなく、「準備できた組織だけが成果を得られる」領域です。
ぜひこの記事を通じて紹介した失敗パターン・成功の要因・評価チェックリスト・導入比較表を参考に、自社の現場と照らし合わせてみてください。
一歩目の見直しが、三歩先の失敗を防ぎます。
そしてその積み重ねが、AGV導入による本当の現場変革につながっていくのです。
ついやりがちな判断ミスや、後悔につながる落とし穴を解説しています。
現場で本当にあった失敗事例と、その対策もあわせて紹介。
「知らなかった」では済まされない前に、ぜひ目を通しておいてください。
→ 失敗事例と対策をまとめた資料を今すぐ見る