「人手が足りない」
「搬送作業にムダが多い」
「でも、AGVを入れて本当にうまくいくのか?」
そんな悩みを抱える製造業・物流業の現場は少なくありません。
実際、AGV(無人搬送車)の導入は年々増加していますが、“導入して終わり”ではなく、“どう使うか”が成功の分かれ道となっています。
本記事では、AGVを導入して現場改善に成功した企業10社の事例を、目的・業種・AGVタイプごとに分類して紹介します。
「他社がどのように課題を整理し、どんな構成で効果を出しているのか?」を具体的に知ることで、自社に近い導入モデルを見つけやすくなるはずです。
さらに、事例から共通する成功要因・導入の工夫・失敗を防ぐ視点まで網羅。
AGV導入を単なる設備投資ではなく、現場設計の再構築とROI最大化のプロジェクトにするためのヒントを詰め込んでいます。
まずは、自社と似た課題・現場構成を持つ事例から読み進めてみてください。導入に向けたヒントが、きっと見つかるはずです。
AGV導入成功の共通点を探る|事例を読み解く3つの分類軸
AGV(無人搬送車)の導入は、単なるロボット導入にとどまらず、「現場の課題解決」に直結する重要なプロジェクトです。したがって、他社事例を参考にする際には、単に表面的な成功事例を見るだけでなく、「自社にとっての再現性」を見極めることが欠かせません。
本記事ではそのために、AGV導入事例を以下の3つの軸で分類し、ユーザーが自身の状況と照らし合わせながら活用できるよう設計しています。
業種別:製造業/物流業
AGVが担う役割は業種によって大きく異なります。製造業では「工程間搬送の自動化」や「ライン連携」が主眼となる一方、物流業では「棚入れ・ピッキング」など倉庫内作業の効率化が中心です。そのため、業種別の分類は初期段階での事例選別に非常に有効です。
導入目的別:人手不足対策/搬送効率化/夜間対応/温度環境対応 など
AGV導入の本質は「何を解決したいのか」です。同じAGVでも、「人手を減らす」目的と「搬送の正確性を上げる」目的では設計思想も導入フローも変わります。目的軸を明確にすることで、安易な模倣による失敗を防ぎ、導入ROIの最大化が図れます。
AGVタイプ別:低床型/フォークリフト型/AMR/牽引式/小型AGV
現場のレイアウトや作業フローによって最適なAGVのタイプは異なります。例えば、狭小エリアや入り組んだ通路では小型AGVやAMRが有効ですが、大量搬送には牽引式やフォークリフト型が向いています。AGVの特性理解は、選定精度を高め、無駄なコストを回避する要となります。
導入パターン分類の早見チャート
以下の図は、「自社の状況に合う事例はどれか?」を探すための視点整理チャートです。
[業種]
├─ 製造業
│ ├─ 課題:工程間の属人化 → タイプ:低床型AGV/SLAM式
│ ├─ 課題:多品種少量/頻繁な品番変更 → タイプ:AMR/小型AGV
│ └─ 課題:夜間出荷対応 → タイプ:テープ式AGV
└─ 物流業
├─ 課題:棚入れ混雑/ピッキング非効率 → タイプ:フォーク型AGV/AMR
├─ 課題:出荷ピークの混雑 → タイプ:牽引式AGV
└─ 課題:低温対応/人員負担軽減 → タイプ:耐寒仕様AGV
【目的別に整理】
人手不足対策 → 少人化対応AGV(AMR/フォーク型)
搬送効率化 → 自動搬送・最短ルート設計が可能なAGV
夜間対応 → 簡易運用型AGV(磁気誘導/テープ式)
温度環境対応 → 耐寒/耐熱AGV
このように多軸的に分類することで、単なる「成功事例の羅列」ではなく、自社にとっての「導入可否の判断材料」として事例を読み解くことができます。
AGVの具体的な導入構成に加え、機種選定の段階で役立つ国内外メーカーの特徴については、こちらの記事で詳しく比較しています
AGV導入で現場がどう変わったか|製造業における具体事例5選
AGV(無人搬送車)は、単なる省人化ツールではありません。製造業の現場では、「生産工程の再設計」や「人・モノの流れの最適化」といった、より本質的な改善に結びついています。このセクションでは、導入背景・AGVの構成・得られた成果をひも解きながら、導入が成功した“本質的な理由”に迫ります。
① 電子機器メーカー|多品種・少量生産への柔軟対応
頻繁な品番切り替えや不規則な生産工程が原因で、搬送が属人化。AGV導入前は、人員配置の最適化に頭を悩ませていました。
低床型AGV(磁気誘導式)を製造ラインに連携させることで、段取り変更にも自動追従できる搬送体制を構築。結果として、不要な待機工数を排除し、稼働率が15%向上。2人で対応していた搬送を1人で担えるようになりました。
これは、「変化に強い搬送体制」をどう築くかという観点で参考になります。
② 自動車部品工場|工程間搬送の標準化
従来は、紙伝票を頼りに作業員が手作業で搬送していたため、急な工程変更時には混乱が発生していました。
SLAM式AGVと生産スケジューラを連携させることで、リアルタイムで柔軟に搬送ルートを変更できる仕組みに進化。搬送ミスが激減し、突発対応にも即応可能に。加えて、「搬送状況の可視化」が改善活動の加速にも貢献しました。
これは、標準化だけでなく“柔軟性のある標準”の重要性を示す好例です。
③ 食品製造工場|夜間出荷の自動化
夜間出荷作業は限られた人員で対応していたため、作業負荷の偏りや品質リスクが課題でした。
磁気テープ式AGVを仕分けエリアに組み込み、単純な搬送業務を自動化。深夜の作業が完全に無人化され、出荷処理の安定化とクレーム減少を実現しました。
この事例は、「無人化しやすい業務」に的を絞る戦略の有効性を示しています。
④ 精密機器組立|狭小エリア対応の搬送支援
90cm未満の狭い通路では台車が詰まり、しばしば作業遅延の原因に。従来のAGVでは対応困難な現場でした。
小型AGVとピッキングカートを連携させ、通路幅に最適化された搬送ルートを実現。作業遅延リスクを大幅に減らし、歩行距離も20%削減されました。
狭い現場でもAGVが活用できることを示した、「スペース制約への打開策」です。
⑤ 医療機器メーカー|検査工程との同期化
検査済みの製品を手運びしていたため、工程間で待ち時間や手戻りが発生。品質管理の観点でも課題がありました。
AMRと検査装置をRFIDで連携し、搬送とトレーサビリティを同時に実現。工程の再設計にもつながり、全体工数を30%削減できました。
この事例は、「品質管理と搬送の統合」という高次目的を果たしたモデルとして注目されます。
クリーンルーム環境でのAGV導入に関しては、こちらの記事で清浄度クラス別の選定ポイントを詳しく解説しています。
事例比較表|製造業におけるAGV導入パターンと効果
No | 業種 | 課題 | AGVタイプ | 特筆すべき成果 |
---|---|---|---|---|
① | 電子機器メーカー | 多品種生産・段取り頻発 | 低床型(磁気誘導) | 工数ゼロ化・人員最適化 |
② | 自動車部品工場 | 搬送の混乱とミス | SLAM式 | 可視化・柔軟性・ミス削減 |
③ | 食品製造工場 | 夜間作業の人手負担 | 磁気テープ式 | 無人化・品質安定 |
④ | 精密機器組立 | 狭小通路による遅延 | 小型AGV | 歩行距離削減・作業安定化 |
⑤ | 医療機器メーカー | 手運び・検査工程の非効率 | AMR(RFID連携) | 工数30%削減・工程再設計実現 |
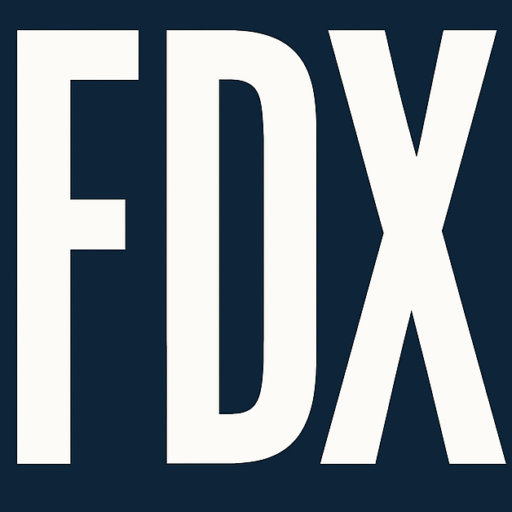
Factory DX
運営事務局
このように、各事例は異なる課題に対して、適切なAGVタイプと構成で解決を図っており、「課題とAGV構成の一致度」が成果を左右する要因であることがわかります。
単にAGVを導入するのではなく、「何をどう変えたいのか」を明確にし、構成を設計することが成功への第一歩となります。
なお、AGVの導入は多くの場合、高額な初期投資が伴います。こうした導入費用を抑えるための補助金制度の活用については、申請の注意点や成功パターンを解説したこちらの記事をご覧ください。
成功事例に共通する構成とは|AGV導入パターン別の横断比較まとめ
物流現場では、人の移動距離や滞留の発生、温度環境など、「作業環境そのもの」がボトルネックになりやすいのが特徴です。AGVの導入によって、こうした根本課題にどう切り込んだのか。以下の事例を通じて、構成の意図と得られた成果を読み解いていきます。
⑥ 3PL倉庫|入荷搬送の無人化
繁忙期や特定時間帯に棚入れ作業が集中し、人手が回らず滞留が発生。入荷処理の遅延が常態化していました。
ここではフォークリフト型AGVをWMS(倉庫管理システム)と連携させることで、重量物を自動で棚入れ可能に。作業時間を30%短縮したうえ、ヒューマンエラーによる事故ゼロを継続中です。
この事例は、「人手依存が事故リスクに直結する作業には、重量物対応AGVが効果的」という示唆を与えます。
⑦ アパレルEC倉庫|ピッキングの歩行距離削減
アパレル商材の取り扱いは商品点数が多く、繁忙期には作業員の歩行距離が増大。結果として生産性にばらつきがありました。
棚搬送型のAMRと在庫管理システムを連携し、作業者の元に棚を自動搬送。導線を1/3に短縮し、生産性は1.8倍に向上。さらに熟練度に依存しない作業構成を実現しました。
これは、「移動を減らすことで、個人差のない作業効率が実現できる」という本質を突いた事例です。
⑧ 日用品倉庫|出荷エリア混雑の解消
出荷処理が集中するピーク帯では、通路が作業員や台車で混雑し、安全面にも懸念がありました。
牽引式AGVを導入し、仕分けラインと統合。物量が集中するエリアの搬送を自動化し、混雑を緩和。処理能力が20%向上しただけでなく、安全性の向上にもつながりました。
このように、「ピークの一時的混雑は、搬送の自動化で緩和できる」という点が実用的です。
⑨ 冷凍食品物流|低温環境対応型AGVの導入
−20℃以下の冷凍倉庫では作業員の身体的負荷が大きく、作業のたびに庫内の温度変動も発生していました。
耐寒仕様のAGVを導入し、ゾーン間搬送を完全自動化。作業者の立ち入り回数を半減させ、温度変動による品質リスクも軽減。作業時間も短縮されました。
これは、「人が入るほどリスクが増す現場では、AGVが“品質保証装置”としても機能する」という新しい視点を提供します。
⑩ EC物流センター|人と共存する混在環境対応
業務が属人的で、経験者に作業が偏っていたため、新人や応援人員がうまく適応できず、教育がボトルネックでした。
AMRを人と協働できるエリアに配置し、標準化された作業フローに統合。誤搬送は20%減少し、ストレスの少ない作業環境が整いました。
この事例は、「自動化の目的が“人を減らす”ではなく、“人が働きやすくなる設計”に変化している」ことを象徴しています。
AGV導入パターンと成果比較表(物流業編)
No | 倉庫タイプ | 課題 | AGV構成 | 成果 |
---|---|---|---|---|
⑥ | 3PL倉庫 | 入荷の人手不足と滞留 | フォークリフト型×WMS | 棚入れ30%短縮、事故ゼロ更新中 |
⑦ | アパレルEC倉庫 | 歩行距離・生産性のムラ | 棚搬送型AMR×在庫管理 | 生産性1.8倍、導線1/3に短縮 |
⑧ | 日用品倉庫 | 出荷ピーク時の混雑 | 牽引式AGV×仕分けライン | 処理能力20%UP、安全性も向上 |
⑨ | 冷凍食品物流倉庫 | −20℃環境での負荷と品質 | 耐寒AGV×ゾーン搬送 | 立ち入り半減、品質リスク軽減 |
⑩ | EC物流センター | 経験者偏重・教育負荷 | AMR×人協働エリア | 誤搬送20%減、標準作業・ストレス軽減 |
これらの事例に共通するのは、「AGVを単なる機械としてではなく、“現場設計の一部”として活用している」点です。作業環境、人の特性、物流の特性に応じてAGVをどう使うか。それが成功の分かれ目になります。自社の課題と照らし合わせて、導入構成のヒントとしてぜひ活用してください。
導入パターンごとに何が効いたか|AGV活用の横断的成功要因まとめ
AGVの導入に成功している製造業の事例には、ある共通点があります。それは、「課題に対して最適なAGVタイプと構成を選定していること」、そして「そのAGVが現場にどう適合するかを明確に設計していること」です。
以下に、製造業における代表的な導入パターンと、それぞれの成功要因を整理します。個々の現場に対して、どのような思考プロセスでAGVを選んだのかを読み解くことで、自社の導入判断のヒントになるはずです。
① 多品種少量生産の柔軟搬送に、低床型AGV×ライン連携
段取り変更が頻発する現場では、人の判断に頼ると属人化しやすくなります。AGVを製造ラインと連携させることで、柔軟な品番切り替えに追従できる自動搬送を構築。
この自動性が、属人性の排除と稼働率向上を両立しました。さらに、人員を2名から1名に再配置でき、生産体制全体の最適化にも寄与。AGV導入が、生産フローそのものの可視化にも貢献しました。
② 工程間の混乱解消に、SLAM式AGV×スケジューラ連携
生産の順序が流動的な現場では、柔軟なルート設計が可能なSLAM方式が有効。スケジューラとの統合により、突発的な工程変更にも対応できる動的な搬送体制を確立しました。
従来は工程変更のたびに手配ミスや滞留が発生していましたが、自動ルート再構成によりその課題を解消。結果として、搬送効率だけでなく現場のストレス軽減にもつながりました。
③ 夜間出荷業務の省人化に、テープ式AGV×仕分けエリア連携
単純作業が集中する夜間は、AGVによる完全無人化がROIに直結します。テープ式は初期導入のハードルが低く、分かりやすいルート設定が可能な点も採用理由です。
導入後は、夜勤作業の常駐人員がゼロになり、労務コストが大幅に削減。さらに、作業ミスやクレームの発生率も低下し、出荷品質の安定にも貢献しました。
④ 狭小通路への対応に、小型AGV×ピッキングカート連携
幅90cm未満という物理制約に対して、AGVのサイズ選定が決め手となりました。ピッキング工程と直結させることで、遅延リスクを最小化しつつ、移動効率も向上させています。
これにより、通路の詰まりが解消され、搬送待機による生産ラインの停止がなくなりました。加えて、歩行距離が約20%削減され、作業者の負担軽減にもつながっています。
また、傾斜やスロープといった床面の物理条件も、AGV導入設計では見逃せません。登坂角度ミスが引き起こす問題については、こちらの記事をご覧ください。
⑤ 検査工程との同期化に、AMR×検査装置(RFID)連携
人による搬送ではトレーサビリティが担保できないという課題に対し、AMRの自由移動性とRFIDの組み合わせで、自動搬送と品質保証を同時に達成。これは、搬送=品質管理の一部という視点転換の好例です。
結果として、検査後の誤出荷リスクがゼロになり、工程間の再調整も不要に。工数は30%以上削減され、全体の工程リードタイムも短縮されました。
製造業におけるAGV導入パターンマップ
以下は、製造業におけるAGV導入事例を横断的に整理した比較表です。各現場の課題に対して、どのタイプのAGVが選ばれ、どのような構成・工夫によって成果が得られたのかを一目で確認できます。自社の課題と照らし合わせながら、最適な導入パターンを見極める参考にしてください。
課題カテゴリ | 採用AGVタイプ | 成功の決め手 |
---|---|---|
多品種・段取り頻発 | 低床型AGV | ライン連携による柔軟搬送 |
工程間の混乱 | SLAM式AGV | スケジューラ連携で動的ルート対応 |
夜間の無人化 | テープ式AGV | 単純作業の自動化による省人化 |
狭小通路の制約 | 小型AGV | 通路対応サイズによる安全搬送 |
品質保証・連携遅延 | AMR(RFID連携) | トレーサビリティ確保と工程再設計 |
このように、各成功事例に共通するのは「現場課題に対して、技術と構成をどう最適化したか」という視点です。
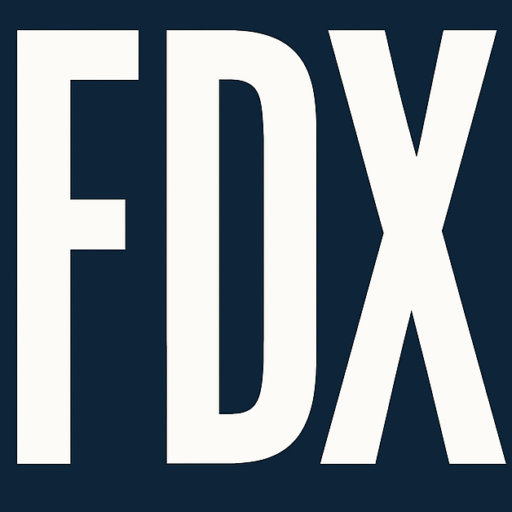
Factory DX
運営事務局
ただAGVを導入するのではなく、「何のために、どのように導入するのか」を明確にしなければ、成果は限定的になります。
物流業編|AGV導入で成果を出した現場の成功要因
物流現場のAGV導入は、製造業以上に「現場レイアウト」「物量の変動」「作業者の動線設計」が成果を左右します。なぜなら、倉庫作業は“動く人とモノ”の制御が中心であり、その最適化が作業効率に直結するからです。
ここでは、5つの導入事例から共通する「成功の構造」を解き明かし、どのような構成が物流現場に適しているのかを解説します。
⑥ 入荷作業の省人化に、フォーク型AGV×WMS連携
課題は、入荷集中時に発生する棚入れ作業の滞留。人手依存では限界があり、処理遅延や誤格納のリスクが常態化していました。
そこで、フォークリフト型AGVを導入し、WMSと連携させることで「棚番単位の自動搬送」を実現。人間よりも正確な棚入れが可能になり、作業時間の短縮だけでなく、事故リスクもゼロに近づけました。
重量物搬送や棚格納においては、AGVによる“定位置搬送”の安定性が最大の武器になります。
⑦ ピッキングの歩行距離削減に、棚搬送型AMR×在庫管理連携
EC倉庫では、人が商品を探して歩き回る従来方式が非効率の温床でした。とくにアパレルなど多品種商品を扱う現場では、生産性に大きなムラが出やすい。
そこで、棚ごと作業者のもとに運ぶ「棚搬送型AMR」を導入。作業者はその場から動かずピッキングできるため、導線は1/3に短縮、生産性は1.8倍に向上。
この事例は、“人が動く”から“棚が動く”へと発想を転換した構成が、パフォーマンスを飛躍的に高めることを証明しています。
⑧ 出荷エリア混雑の解消に、牽引式AGV×仕分けライン統合
出荷ピーク時間帯は、台車や作業員で通路が混雑。接触事故や遅延が発生していました。
そこで導入されたのが、複数台車を一度に運べる牽引式AGV。仕分けラインと連動させ、交通導線をあらかじめ整備することで、混雑を緩和。作業の安全性と処理能力を同時に向上させました。
「台車渋滞」が起きやすい現場では、搬送単位の集約と導線整備が鍵となります。
⑨ 低温環境への対応に、耐寒AGV×ゾーン搬送構成
−20℃以下の環境では、作業者の滞在時間に制約があり、出入りのたびに温度変化が発生。これが品質リスクに直結していました。
導入されたのは、耐寒対応AGVによるゾーン搬送。人が介在しない動線を構築することで、立ち入り回数を半減。冷気保持による品質安定も図れました。
この事例は、AGVが“省人化ツール”にとどまらず、“温度制御の一部”として機能することを示しています。
⑩ 経験依存からの脱却に、AMR×人協働エリア運用
属人化が進んだ現場では、作業の平準化が困難で、教育コストも高止まり。応援人員の即戦力化が課題でした。
そこで、人と共存できるAMRを協働エリアに導入。標準フローの中にAGVを組み込み、誤搬送を減らしつつ、作業者の心理的負荷も軽減されました。
この事例は、自動化=省人化ではなく、「作業を誰でもできる状態に整える」ことが成果に直結するという、現場設計視点の象徴です。
なお、協働ロボットを搭載したAGVの導入により、“搬送だけでなく作業もこなすロボット”として活用が広がっています。導入効果や注意点については、こちらの記事で詳しく解説しています。
成功要因マトリクス|物流業における導入目的と構成の関係
以下は、物流業におけるAGV導入の成功パターンを「課題カテゴリ」「採用AGVタイプ」「成功の決め手」の3軸で整理した一覧表です。現場ごとの課題に対して、どのような構成が成果につながったのかが一目でわかります。自社の課題と照らし合わせながら、導入検討時の判断材料としてご活用ください。
課題カテゴリ | 採用AGVタイプ | 成功の決め手 |
---|---|---|
入荷作業の省人化 | フォークリフト型AGV×WMS | 棚番管理の自動化と事故リスク低減 |
ピッキング効率化 | 棚搬送型AMR×在庫管理 | 歩行削減と熟練度の平準化 |
出荷エリアの混雑緩和 | 牽引式AGV×仕分けライン | 複数搬送による導線の整理と安全性向上 |
冷凍エリア対応 | 耐寒AGV×ゾーン搬送 | 人立ち入り削減と品質保持の両立 |
教育負荷・作業平準化 | AMR×人協働エリア運用 | 誤搬送削減と作業標準化による属人性の排除 |
このように、物流業においては「課題に即した構成選定」と「現場設計への落とし込み」が成功の分岐点となります。
AGVは単なる搬送ロボットではなく、「現場全体の設計に組み込むべき要素」として捉えることで、ROIと現場力の両立が可能になります。自社の課題と照らし合わせ、最適な導入モデルを探る材料としてご活用ください。
どの課題に、どのAGV事例が効いたか?|目的別マトリクスで徹底整理
AGV導入で成果を上げる企業は、例外なく「明確な導入目的」と「自社環境に合った導入パターン」を押さえています。しかし多くの現場では、「なんとなく便利そう」で検討が始まり、結局ROIが不明確なまま頓挫するケースも少なくありません。
そこで重要になるのが、「目的起点で事例を読み解く視点」です。
以下のマトリクスは、製造業・物流業それぞれにおいて、各導入目的に対応する成功事例を整理したものです。自社の課題が「人手不足」なのか「夜間対応」なのかなど、起点を明確にすることで、近い導入パターンを効率的に見つけることができます。
業界×導入目的別対応マトリクス
以下の表は、AGV導入事例を「導入目的 × 業界(製造業・物流業)」のマトリクス形式で整理したものです。
自社の課題がどの目的に該当するかを起点に、近い業種・環境の成功事例を探す手がかりとして活用してください。導入前の検討ステップにおける“課題と構成のマッチング精度”を高めるための参考資料として有効です。
導入目的 | 製造業 事例No | 物流業 事例No |
---|---|---|
人手不足対応 | ①, ②, ④, ⑤ | ⑥, ⑦, ⑩ |
搬送効率化 | ①, ②, ⑤ | ⑥, ⑦, ⑧ |
夜間稼働 | ③ | ⑩ |
冷凍環境対応 | – | ⑨ |
工程間連携・標準化 | ②, ⑤ | – |
活用のヒント:このマトリクスをどう使うか?
このマトリクスは、単なる分類表ではありません。導入検討の初期段階で「どの課題に対し、どのようなAGV構成が機能するのか」を仮説立てする道具です。
たとえば:
- 夜間稼働を完全無人化したい → 製造業では事例③(食品工場)に注目。物流では⑩(ECセンター)で部分無人化を実現。
- 工程間の作業属人化を解消したい → 事例②と⑤が共通して工程連携を自動化しており、現場再設計の参考に。
- 冷凍倉庫での人員負担を軽減したい → 該当は物流事例⑨のみ。耐寒対応AGVの仕様や構成は非常に実用的。
このように、目的別に最適なAGVのタイプと構成を照らし合わせることで、「うちの現場でも再現可能か?」という判断がスムーズになります。
AGV導入の鍵は「現場との相性」です。このマトリクスを出発点に、該当しそうな事例を深堀りしていくことで、導入の成功率を格段に高められるはずです。
ただ導入するだけでは失敗する|現場主導でAGVを活かす方法
AGV導入の成否は、機種の選定や仕様の優劣だけで決まるわけではありません。むしろ、「現場がどれだけ主体的に導入プロセスを設計・検証し、合意形成を図ったか」が、成功を左右する決定的な要素になります。
以下では、実際に成果を上げた企業に共通する“現場発の工夫”を紹介し、その背景と効果を解説します。
① ルートの仮設計とシミュレーションの徹底
AGVは、単なる自動搬送機ではなく、「作業フローの一部」です。実運用を前提としたルート設計を行わなければ、現場での“詰まり”や“想定外の遅延”が頻発します。
導入前に現場主導でルートの仮設計を行い、複数パターンでシミュレーションを重ねた企業では、初期トラブルの回避率が大きく向上しています。これにより、「現場に合った構成か?」という視点で、AGV選定の最終判断にも役立てられました。
② 工程ごとの“役割設計”を明文化して社内合意を形成
AGV導入が頓挫する典型例は、「誰が何をすべきか不明確なまま進行し、現場の反発を招く」ケースです。そこで成功企業は、導入フェーズから現場管理者・作業者を巻き込み、工程ごとに“人とAGVの役割分担”を明文化しました。
このアプローチにより、全関係者が自分ごととして理解・納得し、運用時のトラブルも自主的に改善されやすくなります。AGV導入を“技術導入”ではなく“現場文化の更新”として位置づけた好例です。
③ 小規模からのテスト導入でリスクと学習コストを最小化
いきなり全ラインで導入するのではなく、1ラインまたは1エリアからの段階的展開を採用することで、万一のトラブルにも柔軟に対応できる余地を確保。
この段階的アプローチは、現場ノウハウの蓄積と成功体験の共有がしやすくなるという副次的効果も生み出します。結果として、社内の横展開もスムーズに進む傾向があります。
AGV導入プロセスのタイムライン
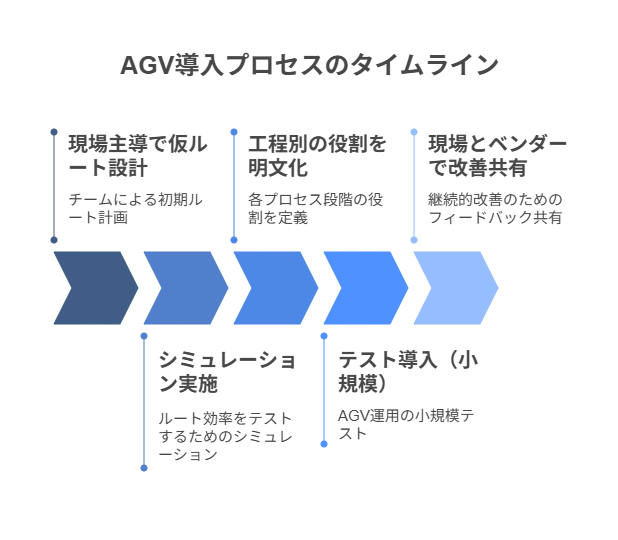
これらの工夫に共通するのは、「技術導入を現場目線で咀嚼し、自社の運用文化に落とし込んでいる」点です。どれも派手な施策ではありませんが、実際の運用に耐えうる導入を実現するには不可欠なプロセスです。
AGV導入を検討する際には、機能や価格だけでなく、こうした「現場側の準備と巻き込み方」にも十分な時間とリソースを割くことが、結果として最短の成功ルートとなります。
気になる事例があった方は、自社で導入する際のステップや注意点も整理しておくとスムーズです。
以下の記事でくわしく解説していますので、参考にしてみてください。
なぜ失敗するのかを事例から逆算|AGV導入前のチェックポイント
AGVの導入は、単なる省人化プロジェクトではありません。成功事例の裏には、導入目的の解像度と現場設計の精度が必ず存在します。逆に、それが曖昧なまま進めた場合、導入後に「動いてはいるが効果が見えない」「現場に合わない」という“機能不全状態”に陥るケースが少なくありません。
以下では、失敗を回避するために押さえておくべき視点を、実例に基づいて整理します。
「人手を減らす」が目的では不十分
よくある誤解が、「人手不足だからAGVを導入する」という短絡的な発想です。重要なのは、人を“減らす”ことではなく、“再配置”するのか“標準化”するのかという明確な意図を持つこと。
たとえば、夜間対応を完全無人化した食品工場(事例③)は、「単純作業の夜勤をゼロにする」ことが目的でした。一方、工程標準化を進めた部品工場(事例②)は、「属人作業を平準化し、変化に強い運用体制を作る」ことが目的です。
どちらも“人手を減らす”とは言えますが、目的の粒度が異なれば、AGVの選定・構成・導入方法もまったく異なるという点が極めて重要です。
「便利そう」ではなく「何を代替したいか」を明確にする
AGVは決して魔法の箱ではありません。導入しても、従来業務との置き換えポイントが不明確なままでは、かえって工程が複雑になることもあります。
たとえば、EC物流センター(事例⑩)では、経験者に偏っていた作業をAMRによって平準化することを目的としました。AGVを導入すること自体が目的なのではなく、「教育負荷や誤搬送の原因となる属人性をAGVで代替する」ことが本質でした。
このように、何をどこで、どのように“代替”するのかを言語化することが、成功の土台となります。
AGV運用の安定化を図るうえでは、稼働時間や充電方式に応じたバッテリーの選定も欠かせません。種類や寿命、選び方については、こちらの記事で網羅的に解説しています。
成功している現場は「目的・ルート・役割」が明確
多くの成功事例に共通するのは、AGV導入後の運用が非常にシンプルであるという点です。なぜなら、事前に「何のために・どこを通って・誰が何をするか」が明文化されているからです。
シンプルさはトラブルの少なさと直結し、現場の納得度や改善スピードにも大きく影響します。複雑な技術を使うからこそ、運用はできるだけシンプルであるべきです。
失敗を防ぐための3つの明確化フレーム
AGV導入で失敗を避けるためには、単なる製品選定ではなく、「何のために、何を置き換え、どう運用するのか」という3つの視点を明確にすることが不可欠です。以下の表は、導入前に必ず整理しておきたい思考フレームを質問形式でまとめたものです。社内検討のチェックリストとしてもご活用ください。
明確化すべきポイント | 質問例(確認すべき視点) |
---|---|
導入目的の明確化 | 再配置なのか? 標準化なのか? 完全無人化を目指すのか? |
代替対象の明確化 | どの工程の、どの作業をAGVに置き換えるのか? |
運用構成の明確化 | 誰が何を担当し、AGVはどこを通って何を運ぶのか? |
このフレームを導入検討初期に活用することで、「とりあえず入れてみる」ではなく、「入れる前に導入の意味を整理する」姿勢が身につきます。AGV導入を一過性の施策に終わらせず、現場設計の再構築と継続的な改善の起点とすることが、真の成功につながる視点です。
AGV導入事例に正解はない 自社に置き換えて考える視点を
AGV導入の成功事例には、確かに一定の型があります。しかし、現場ごとの条件、目的、制約に応じて、最適な構成や運用方法は大きく変わります。大切なのは、事例そのものを「完成された正解」と捉えるのではなく、自社に活かすための“ヒント”としてどう読み解くかという視点です。
たとえば、同じように「人手不足対策」を目的としてAGVを導入した企業でも、
- ある現場では夜間帯の無人化に集中し、
- 別の現場では属人業務を標準化して再配置を実現するなど、
目的の粒度や現場の状況によってアプローチはまったく異なります。
つまり、「同じ課題」でも「同じ答え」にはならないということです。
事例を見るときは、「うちには合わない」と切り捨てるのではなく、
- 自社と共通する課題はあるか?
- 再現できる運用設計はどれか?
- カスタマイズが必要な部分はどこか?
といった問いを立て、自社流に応用する思考が重要です。
この記事で紹介したマトリクスや構成別の事例比較を起点に、まずは「自社の課題に近いパターン」を見つけてください。そのうえで、小さく試しながら検証し、運用に合う形へと調整していくプロセスこそが、AGV導入を現場改善につなげる最短ルートです。
AGV導入は、単なる装置の購入ではなく、現場の設計を問い直すチャンスです。事例をヒントに、自社にとっての“最適解”を探る第一歩を踏み出しましょう。
「自社にも当てはまる事例はあるだろうか?」 そんな疑問に応える、導入タイプの見極め・比較・ROI試算まで網羅した AGV導入まるわかりガイド を無料配布中です。現場別・目的別に最適な導入パターンが見えてきます。