自社のAGV、最近バッテリーの持ちが悪くなっていませんか?
24Vで本当に足りているのか、それとも48Vにすべきなのか――搬送力や稼働時間の課題に直面したとき、バッテリー選定は「後回しにできない設備戦略」そのものです。
実際、バッテリー容量の誤選定や寿命の見落としによって、
「搬送途中でAGVが停止してラインが止まった」
「交換サイクルが想定より早く、予算がひっ迫している」
「拡張導入時に既存機体との電圧不整合が発生した」
といったトラブルは少なくありません。
この記事では、24V/48Vバッテリーの違いや用途別の使い分けだけでなく、
寿命の目安・種類ごとの特徴・適切な交換タイミング・カスタマイズ事例まで、実務で役立つ情報を包括的に整理しています。
もしこの記事を読まずに「何となくの経験値」でバッテリー選びをしてしまえば、その判断ミスは、設備の稼働率・安全性・コスト全体に影響を与えるかもしれません。
今後のAGV運用で無駄なく、止まらず、安全に稼働させるためにも、まずはこの記事で“今、本当に知っておくべきAGVバッテリーの全体像”を押さえておきましょう。
AGVバッテリーとは?産業用無人搬送車(AGV)の基礎知識
AGVとは|工場や物流、自動車・ロボットでの用途と役割
AGV(Automated Guided Vehicle:無人搬送車)は、工場や倉庫、物流センター、あるいは電子部品の製造ラインなどで、人手を介さずに荷物や部品を運搬するための自律走行型ロボットです。磁気テープやレーザーガイド、SLAM(Simultaneous Localization and Mapping)といった技術を使い、事前に設定されたルートに従って走行する点が特徴です。
特に近年は、労働力不足と生産性向上の課題を同時に解決する手段として、製造業から物流業界まで急速に普及しています。AGVは単なる運搬装置ではなく、生産性・安全性・品質の安定に貢献する「インフラの一部」として機能しているのです。
物流ではピッキングや仕分けに活用され、電子部品や精密機器製造では「人が触れるべきでない繊細な搬送」に使われるなど、用途は年々高度化・多様化しています。
AGVバッテリーの重要性と製品に求められる性能・機能
AGVのパフォーマンスと稼働率を根幹から支えているのが「バッテリー」です。AGVは常に自律走行するため、電源供給の安定性と長時間稼働が求められる構成となっており、搭載するバッテリーの選定はそのままシステム全体の生産性に直結します。
以下は、AGVバッテリーに求められる主な性能要件です。
特にBtoBの現場では、「途中で動かなくなる」「バッテリー寿命が予測より短い」といったトラブルが工程停止や出荷遅延という重大リスクにつながります。そのため、単にスペックを見るだけでなく、実運用における信頼性と運用負荷の低さもバッテリー選定のカギとなります。
近年のAGVバッテリー技術動向とラインナップの種類
AGVに使用されるバッテリーは、以下のように複数の種類が存在しますが、近年は「リチウムイオン型」への移行が加速しています。
以下の表は、主なバッテリータイプの違いと技術動向を簡潔にまとめたものです。
バッテリータイプ | 特徴 |
---|---|
鉛蓄電池(従来型) | ・低コスト ・充電時間が長い ・寿命が短い |
リチウムイオン | ・高エネルギー密度 ・短時間充電が可能 ・BMS連携による管理がしやすい ・価格は高めだが長寿命 |
固体電池(新技術) | ・まだ実用段階は限定的 ・安全性・密度・寿命で次世代候補 |
【補足説明】
現在、AGVの電源としてもっとも採用が進んでいるのはリチウムイオン電池です。これは、1回あたりの充電時間を短縮し、稼働時間を最大化するために不可欠だからです。また、遠隔監視や自動充電システムと連動できるのも強みです。
一方で、鉛蓄電池は価格優位性がある反面、交換頻度と運用コストの面で課題が残ります。また、固体電池は今後の展望として注目されているものの、現在は限定的なAGV導入にとどまっているのが実情です。
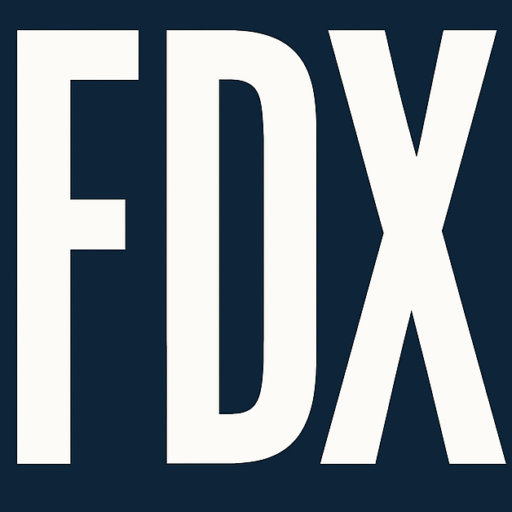
Factory DX
運営事務局
リチウムイオンへの移行が進む理由は、スペックだけでなく“現場の回転率を落とさない”という実務的な背景があるんです。
AGV向けカスタムBMSのリアル導入効果
従来のBMS(バッテリー管理システム)は「電圧監視や過電流保護」程度の管理にとどまっていました。しかし、業務でAGVを大量導入しているある物流現場では、AGV向けにカスタム設計されたBMSを導入したことで、稼働トラブルが劇的に減少したという事例があります。
このカスタムBMSには以下のようなAGV運用に最適化された機能が搭載されていました。
- 高出力時のセルバランシング高速化:走行開始直後の高負荷状態で起こるセル不均衡をBMSがリアルタイムに補正。これにより内部抵抗上昇を抑え、初動の加速性能の劣化が月間30%改善。
- CAN通信によるルート最適化情報と連携:ルート情報や荷重状況をBMSが受け取り、充電中に適切なマッチングや予熱・冷却制御を自動化。無駄な冷却や急速充電による劣化を回避。
- 予知保全アラートの高度化:「充電中にセルごとの電圧変動パターン」を元に劣化兆候を予測。従来比で交換前トラブルを70%削減するシステム設計。
カスタムBMS連携の全体スキーム(AGV運用フローに組み込む)
AGV稼働状況 → ルート/荷重データ → BMSへ送信
└─ BMS:セルバランス/冷却制御/異常瞬時検知
└─ 予知アラート → メンテ計画に反映
この運用で得られたノウハウは、単品機体の改良ではなく、「複数台で動くライン全体の安定稼働」を念頭に設計された点に独自性があります。
特に、高出力セッション直後にバッテリー内部が不安定になりやすいAGV特性に対し、セルバランスのリアル制御で性能維持できた点は、現場運用から導き出された実効性の高い知見として注目に値します。
なお、バッテリーを含めたAGV内部構造の全体像を把握したい方は、こちらの記事でパーツ構成の仕組みを解説しています。
AGVバッテリーのタイプ・種類|鉛蓄電池とリチウムイオンの比較
鉛バッテリー vs リチウムイオン電池のメリット・デメリット
AGVに使用されるバッテリーの主な選択肢として、現在も併存しているのが「鉛蓄電池」と「リチウムイオン電池」です。選定にあたっては、価格や性能だけでなく、導入環境や運用方法に応じた適合性を見極めることが極めて重要です。
特に物流現場や製造現場では、「すでに鉛蓄電池が主流だったため継続使用している」「新規導入時にはメンテナンス性とトータルコストを重視してリチウムイオンを選定した」など、過去の選択が現在の制約になっているケースも少なくありません。
以下に、鉛蓄電池とリチウムイオン電池の比較をまとめた表を掲載します。導入前の判断材料としてご活用ください。
《比較表》AGV用バッテリー:鉛蓄電池とリチウムイオン電池の性能比較
項目 | 鉛蓄電池 | リチウムイオン電池 |
---|---|---|
初期導入コスト | 安価 | 高価 |
寿命(サイクル数) | 300〜500回程度 | 2000〜4000回程度 |
メンテナンス性 | 定期補水や点検が必要 | メンテナンスフリー |
充電時間 | 長い(6〜10時間) | 短い(1〜3時間) |
重量・サイズ | 重く大型 | 軽量・コンパクト |
環境対応 | 廃棄時に鉛処理が必要 | リサイクル処理が比較的容易 |
BMS(バッテリーマネジメント) | 非対応が多い | 多くの製品で標準搭載 |
温度特性 | 高温・低温にやや強い | 温度管理が必要 |
【補足説明】
鉛蓄電池は初期コストを抑えられる利点があるものの、寿命が短くメンテナンス負荷も高いため、結果的にトータルコストが上昇するケースが多く見られます。一方で、リチウムイオン電池はBMSとの連携による稼働最適化や省メンテナンス運用が可能となり、中長期的な投資対効果に優れる点で支持されています。
鉛蓄電池からリチウムイオンバッテリーへの置き換えは可能?
AGVの稼働環境が変わるなかで、「既存AGVに搭載された鉛蓄電池をリチウムイオンバッテリーに置き換えたい」というニーズは年々高まっています。結論から言えば、多くのケースで物理的・技術的に置き換えは可能ですが、いくつかの要点を慎重に検討する必要があります。
主な検討ポイントは以下の通りです。
- バッテリーの形状・取り付け寸法:既存スペースに収まるか
- 電圧仕様の一致:既存AGVの設計電圧と合致しているか
- 充電器の互換性:リチウム用の専用充電器が必要な場合あり
- BMSや車載制御との連携:CAN通信やRS485制御が必要な場合がある
- 安全装置との整合性:過充電・過放電の保護が既存設計と適合するか
現場でのトラブルを回避するためには、AGVメーカーまたは電源技術者と相談のうえ、実機検証を必ず実施することが推奨されます。また、「リチウムへの更新=性能向上」という単純な話ではなく、システム全体の調整が必要になる点に注意が必要です。
AGV用リチウムイオンバッテリーの採用が進む理由と安全性
AGV業界ではここ数年、リチウムイオン電池の採用比率が飛躍的に高まっています。その背景には単なる技術革新だけでなく、「実際の運用現場で得られるメリットの明確さ」があります。
主な採用理由は以下の3点に集約されます。
また、安全性についても大きく進化しています。特にAGV用途におけるリチウムイオンバッテリーは、多層の保護回路と温度センサー、過充電保護、短絡保護などの多重安全設計が施されています。さらに近年は、発火リスクの低いLFP(リン酸鉄リチウム)系セルを用いた製品も増えており、安全と性能を両立させる方向での開発が進んでいます。
このように、リチウムイオン電池は単なる「電源」ではなく、AGV全体の稼働効率と安全性を左右する戦略的コンポーネントとして認識されています。
動く充電ステーション(モバイルチャージャー)の導入効果
近年、中国の特許(CN104836293A)で公開された「AGVに合わせて自ら移動する充電ステーション」の実装は、充電効率とライン稼働率に劇的な改善をもたらす施策として注目されています。この構想は、AGVの送電が低下すると、充電ステーション自身がAGVを追尾し接続・充電を開始する仕組みです。
この方式を導入した物流現場の運用事例では、以下のような効果が報告されています。
モバイルチャージャー連携フロー
AGV SoC低下 → AGVが充電要求を送信
↓
モバイルチャージャーがAGV位置へ移動
↓
自動接続・充電開始
↓
所定SoCに達したら移動再開
この方式は、固定充電ステーションへの移動時間が不要となるため、AGV1台あたりの運搬サイクルを10〜15%向上させられる可能性があります。大量導入ラインや混流運用環境では、AGVが大きく走行制限されずに常に動き続けるため、製造現場全体のリードタイム短縮に大きく貢献します。
24V・48V AGVバッテリーの比較|容量・定格・用途選びのポイント
24Vバッテリーの特徴・適合装置・用途事例
24V仕様のAGVバッテリーは、小型〜中型の搬送車両や自律移動ユニットに多く採用されており、特に製造現場での部品供給、軽量品のピッキング用途などに適しています。
この電圧帯は、以下のような特長があります。
- システム設計がシンプルで、制御機器との互換性が高い
- バッテリーセル数が少なく、安全回路設計が容易
- コストが抑えやすく、小規模ラインでも導入しやすい
用途としては、工場内の部品供給用AGV、医療機関での物品搬送カート、精密部品工場での静音搬送など、「小回り・低速・短距離」の搬送ニーズに適した構成が主流です。
一方で、高出力や長距離搬送を必要とする用途にはスペック的に制限があるため、選定には搬送重量・傾斜走行の有無・連続稼働時間などの要素を考慮する必要があります。
48Vバッテリーの特徴・自動化ラインでの運用メリット
48Vバッテリーは、比較的大型で高負荷の搬送用途に対応するために採用される仕様で、近年ではスマートファクトリーや物流自動化ラインでの中心的な電源規格となりつつあります。
48V帯には以下のようなメリットがあります。
特に、長距離搬送・高速化・多点間搬送が求められる生産ラインや、大型パレット搬送AGVなどでは、48V設計による効率性と安定稼働が重視されています。
なお、48V仕様を採用する場合、制御盤や充電器、車両設計も一体で最適化する必要があり、システム構築の段階からバッテリー仕様を明確にすることが求められます。
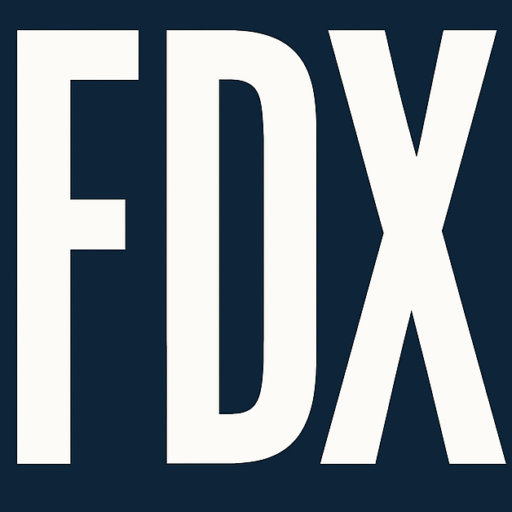
Factory DX
運営事務局
最近は、48Vを標準化しておくことで“将来のAGV拡張”にも対応しやすくなると考える現場が増えてきています。
選定時に確認したい容量・サイクル・サイズ・性能データ
AGV用バッテリーを導入・更新する際に最も重要なのが、「実運用に適した仕様選定」です。単に容量が多ければ良いわけではなく、稼働時間・充電サイクル・サイズ制約などとのバランスが重要です。
以下は、バッテリー選定時に比較検討されるべき主要項目を一覧化したものです。実際のスペック表や提案資料と照らし合わせながらご覧ください。
《比較表》AGVバッテリー選定時に重視すべき仕様一覧
項目 | 比較指標例 | 確認ポイント例 |
---|---|---|
容量(Ah) | 30Ah / 50Ah / 100Ah など | 搬送距離、稼働時間、車両重量と照合 |
電圧(V) | 24V / 36V / 48V | 駆動モーター・制御盤との互換性 |
サイクル寿命 | 1000回 / 2000回 / 4000回以上 | 使用頻度に応じた耐用年数の見積もり |
外形寸法 | 290×180×150mm など | AGVシャーシ内スペースとの干渉有無 |
充電時間 | 1時間〜8時間 | 運用スケジュールとの整合性 |
動作温度範囲 | -10℃〜45℃ など | 使用環境(倉庫内/屋外/冷蔵倉庫等)との整合性 |
【補足説明】
これらの要素を選定前に明確にすることで、導入後の「持たない」「入らない」「充電間に合わない」といったトラブルを未然に防ぐことができます。特に24時間稼働が求められるラインでは、サイクル寿命と充電時間のトレードオフ設計が極めて重要です。
AGVバッテリーのセル・モジュール設計とmm寸法の考え方
AGVバッテリーは、セル(単電池)を直列・並列に組み合わせて電圧・容量を構成する「モジュール化設計」が一般的です。この構成は、性能設計と同時に、搭載スペースとの調和も求められるため、実装時の物理寸法が非常に重要となります。
設計時の基本的な考え方は以下の通りです。
- 電圧調整はセルの「直列数」で調整(例:3.2V×15直列=48V)
- 容量調整はセルの「並列数」で調整(例:3.2V 10Ah×3並列=30Ah)
- 放熱・衝撃対策を考慮し、セルは固定構造またはカートリッジ式で設計
- 通信対応BMSが搭載される場合、モジュール毎にCANポートや温度センサが必要
設計図上では収まっていても、コネクタ・ハーネスの逃げや取付金具の厚みで干渉するケースが現場ではよく発生します。実際にはCADデータと現物寸法の差異も考慮し、数mm単位の余裕を持った配置設計が推奨されます。
AGV選定で迷っている方へ、比較に役立つ実践的な資料をお届けします。
現場別の選定ポイントや、よくある見落としも丁寧に解説しています。
今の検討段階でこそ、手元に置いておきたい内容です。
→ 比較ポイントまとめ資料を今すぐ見る
AGVバッテリーの寿命・劣化・診断|長寿命化のコツ
寿命の目安と劣化原因|運用時の注意点
AGVバッテリーの寿命は、運用の方法や環境に大きく左右されます。製品カタログに記載されている「サイクル寿命(充放電回数)」はあくまで理想的な条件下での目安であり、実際の現場ではその通りにはならないケースが大半です。
一般的に、リチウムイオン電池のサイクル寿命は2000〜4000回程度、鉛蓄電池は300〜500回程度とされますが、以下のような運用が寿命を縮める主な原因となります。
これらの劣化要因を避けることで、バッテリー寿命を大きく延ばすことが可能です。特に24時間稼働の工場ラインでは、メンテナンス性やバッテリー交換頻度が直接、稼働率とコストに跳ね返るため、導入初期からの設計と運用が重要になります。
また、AGVの稼働を止めないための点検・保守の実践方法については、こちらの保守・点検マニュアル記事もあわせてご覧ください。
サイクル回数・充電・放電がバッテリー寿命に与える影響
バッテリーの寿命に影響を与える最大の要素が、充放電の「深さ(DoD:Depth of Discharge)」と充放電回数(サイクル数)です。
たとえば、同じリチウムイオンバッテリーでも、1回あたりの使用量がバッテリー容量の30%程度に抑えられている場合と、80%以上を毎回使い切る場合では、寿命に2倍以上の差が出ることがあります。
また、急速充電ばかり行っていると内部抵抗が上昇し、発熱や電圧降下を引き起こしやすくなります。
以下は、放電深度とバッテリー寿命の相関イメージを示した図解です。
放電深度(DoD)とサイクル寿命の関係
放電深度 | 想定サイクル寿命 |
---|---|
100% | 約500〜700回 |
80% | 約1000〜1500回 |
50% | 約2000〜3000回 |
30% | 約4000〜6000回 |
【補足説明】
この表からも分かるように、「フル充電・フル放電を毎回繰り返す運用」よりも、「適切な残量管理を行いながらの部分充放電運用」の方が、バッテリーの長寿命化には効果的です。特に、AGVをシフト制で運用する場合は、中間充電による部分運用戦略が推奨されます。
バッテリー診断・測定・制御機能での寿命把握
バッテリーの状態を正確に把握し、早期に劣化を検知するには、BMS(Battery Management System)や専用の診断ツールの活用が有効です。
BMSは以下のようなデータを常時監視し、異常や劣化傾向を早期に通知する役割を果たします。
- 電圧、電流、セル温度のリアルタイム監視
- SOC(State of Charge:充電率)推定
- SOH(State of Health:劣化度)推定
- 充放電履歴の記録と異常データのログ化
これにより、実際の使用状況に応じた実効寿命の推定が可能となり、保守計画や交換タイミングの最適化につながります。また、AGV側のPLCやMESと連携することで、ライン停止を未然に防ぐ「予知保全」的運用も実現可能です。
廃棄・環境対応・交換時の安全対策
バッテリーの交換時には、「安全な取り扱い」と「法令順守」が求められます。特に鉛蓄電池は有害物質を含むため、専門業者による適切なリサイクル処理が義務付けられており、不法廃棄や誤処理は重大な法的リスクを伴います。
一方、リチウムイオン電池も破損状態での処理や輸送には厳しい規制(UN38.3 など)があり、以下のような対策が必要です。
- 事前にSOC(充電率)を30%以下に抑えて輸送
- 端子の絶縁処理と個別梱包
- 使用済バッテリーの専用容器保管
- 管理台帳での交換履歴の記録
また、廃棄後の再利用や回収スキームも拡大しており、使用済セルの再利用を前提としたエコ設計が評価される傾向にあります。
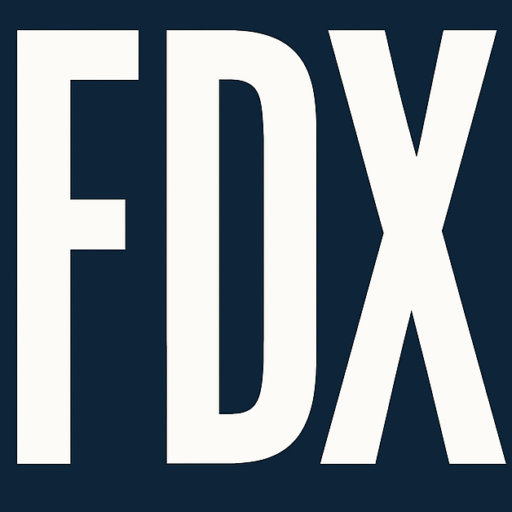
Factory DX
運営事務局
今後はESG(環境・社会・ガバナンス)評価への対応として、バッテリー回収スキームの確立が求められる場面が増えると予想されます。
AGVバッテリー交換時期と手順|トラブル・停止を防ぐ実践ガイド
バッテリー交換のサイン・診断データの見極め方
AGVのバッテリーは、使用頻度や充放電の条件によって劣化速度が大きく異なります。見た目や感覚だけでは判断できないため、交換のタイミングを誤ると、予期せぬ停止や工程遅延といったリスクに直結します。
適切な交換時期を把握するには、以下のデータとサインを総合的に確認することが不可欠です。
また、BMS連携型のAGVであれば、過去ログから充電履歴・使用履歴を抽出し、実効的な寿命を予測することも可能です。
AGVバッテリー交換の基本手順と必要な資料・部品
AGVバッテリーの交換は、単に「外して入れ替える」だけでは済まない、精密機器としての注意が必要な作業です。手順や確認項目を誤ると、車両の異常動作や制御エラー、最悪の場合は発火や短絡の危険も伴います。
以下は、AGVのバッテリー交換時に一般的に必要となる工程と必要資料・部材を整理したものです。
特にBMSや車載PLCと連携しているAGVの場合、単純な交換だけでは機器が起動せず、ID認識や初期化作業が必要となることがあります。交換履歴を明確に残すことで、将来の不具合発生時にも追跡調査が容易になります。
交換時のコスト削減&ライン停止対策
AGVバッテリーの交換には、バッテリー自体のコストだけでなく、交換作業にかかる人件費や停止時間による間接コストも発生します。これらを最小限に抑えるには、予防保全型のスケジューリングと標準化された交換体制の構築が不可欠です。
以下のような対策が、コスト削減と安定稼働に直結します。
加えて、年次・月次での「稼働状況×電池劣化率」をモニタリングし、交換リードタイムを加味した在庫計画を立てておくと、突発トラブルによるライン停止の回避につながります。
AGVバッテリー充電・運用・メンテナンスの最適化
専用バッテリー充電器とワイヤレス充電の活用法
AGVの稼働効率を最大化する上で、充電器の選定と運用方式は非常に重要な要素です。特にリチウムイオンバッテリーの場合、最適な充電器を使用しないと、電池劣化や過熱、システム故障の原因となる可能性があります。
専用のリチウムイオン対応充電器には、以下のような機能が搭載されていることが一般的です。
- 出力電圧・電流の自動調整(CC-CV制御)
- 過充電防止・過熱保護機能
- BMSとの連動によるフル充電制御
- 通信機能による履歴管理・遠隔監視
一方、近年ではワイヤレス充電(非接触充電)の導入も進んでおり、車両が充電ポイントに停止するだけで自動的に充電が開始される仕組みが採用され始めています。これにより、コネクタの抜き差しミスや摩耗、接点トラブルといった物理的な課題が大幅に減少し、保守コストの削減にもつながっています。
充電管理・バッテリー制御システムの設計・実装ポイント
AGVの充電運用を最適化するには、「いつ・どこで・どの程度充電するか」をシステム的に制御する仕組みが必要です。特に24時間稼働体制やマルチライン搬送で導入されるAGVでは、単純なフル放電→フル充電のサイクルでは運用効率が低下します。
以下のような運用制御が有効です。
以下は、充電運用における代表的な方式と特徴を比較した図解です。各自の運用環境に応じた方式を選定する際の参考にしてください。
AGVバッテリー充電方式の比較
方式 | 特徴・適用ケース |
---|---|
定時フル充電 | ・夜間停止時などにまとめて充電 ・スケジュール型、最も一般的 |
中間充電(機会充電) | ・稼働の合間に短時間ずつ充電 ・連続運用時やピーク対策に有効 |
ワイヤレス充電 | ・車両の停車位置で非接触充電が可能 ・設備費は高いが保守性が高い |
【補足説明】
各方式には導入コストや設備要件、運用負荷の違いがあります。例えば中間充電は稼働率向上に寄与する一方、導入にはBMS・AGV制御・フロア導線の全体設計が必要となるため、初期導入時の設計段階から織り込むことが重要です。
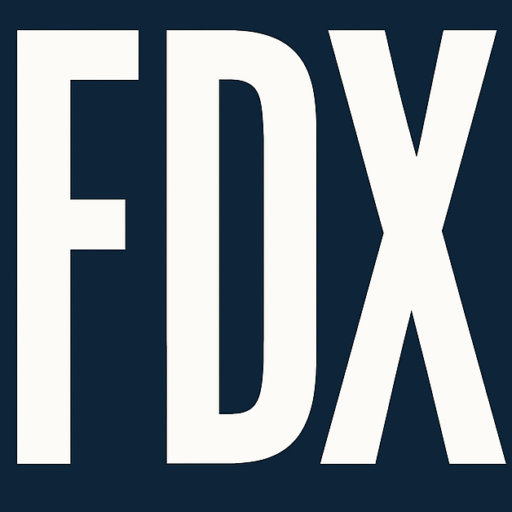
Factory DX
運営事務局
“フル充電+中間充電の併用”が最近のトレンドです。AGVの稼働状況に応じて、柔軟にハイブリッド設計するのが実務的ですね。
AGV・AMRでの効率的なバッテリー運用事例
実際の運用現場では、AGV・AMRの稼働パターンや業種特性に合わせて、バッテリー運用の最適化が図られています。以下は、導入企業における代表的な事例です。
- 電子部品メーカーA社(多品種小ロット対応)
→ 各フロアに複数の中間充電ポイントを設置し、AGVが搬送完了ごとに短時間充電を自動実施。バッテリー交換頻度を従来比40%削減。 - 物流センターB社(24時間稼働)
→ AMR(自律移動ロボット)と連携し、ピーク時以外に順次充電を行う「時間帯分散型充電ロジック」を導入。ピーク時の充電渋滞を回避し、稼働率を92%まで向上。 - 医療品製造C社(異物混入対策)
→ ワイヤレス充電導入により、コネクタ摩耗による異物混入リスクを解消。クリーンルーム対応を維持したまま、充電効率を改善。
これらの事例からも、バッテリー運用の最適化は単にコストだけでなく、品質・安定性・現場の安全性向上にも直結することが分かります。
AGVバッテリー選定・カスタマイズ・最新オプション紹介
バッテリーパック・モジュール設計のカスタム対応
AGVに搭載されるバッテリーは、既製品をそのまま使用するだけでなく、運用条件や車両仕様に合わせて「パック構成」「モジュール構造」「セル構成」などをカスタマイズするニーズが年々高まっています。
特に、以下のような要件を持つ企業ではカスタム設計が必須となるケースが多く見られます。
- シャーシ寸法が特殊で、既成サイズでは収まらない
- 高耐振・高防塵・高温環境での運用を想定
- 通信制御(CAN/Modbus)と連動したBMS構成が必要
- 1台ごとに異なる電圧・容量が求められる多機種少量生産ライン
設計の自由度を持たせるには、「セル単位→モジュール→パック」まで一貫して設計・製造対応ができるバッテリーメーカーやOEMパートナーの選定が重要です。さらに、放熱設計や組立工数の最適化、サービス性(脱着のしやすさ)も長期運用を見据えた設計要素として重視されています。
用途別・環境別に最適なAGVバッテリー選び方
バッテリーの選定基準は、単に電圧・容量といったスペック値だけでは不十分です。実際の運用環境に最適化された設計が行われていないと、期待通りの稼働が得られなかったり、寿命が著しく短くなるリスクがあります。
以下は、使用環境や用途ごとに推奨されるAGVバッテリー構成の一例を整理した表です。
《比較表》用途・環境別のAGVバッテリー選定ポイント
用途・環境 | 推奨構成例 | 選定上のポイント |
---|---|---|
クリーンルーム内搬送 | リチウム(LFP)密閉型 | 粉塵なし、端子絶縁、コネクタレス構造など |
長距離搬送/傾斜路対応 | 48V・高容量リチウム(NMC) | 高出力対応、温度管理、回生充電対応 |
屋外・高温・寒冷地運用 | 耐候構造+保温ヒーター搭載パック | 耐熱ヒューズ、-20~+60℃対応設計 |
軽量物ピッキング用途 | 24V/30Ahリチウム薄型モジュール | スペース制限、小型軽量、カートタイプ対応 |
【補足説明】
このように、現場での環境条件や搬送対象の違いに応じて、バッテリー仕様は柔軟に設計されるべきです。特に新規導入時には、現場ヒアリングと同時に充電設備・交換導線も含めて全体最適を行うことが求められます。
AGV向け最新バッテリー機能と選定サポート資料|失敗しない導入準備
近年では、AGV向けに特化したバッテリーシリーズが各メーカーから登場しており、リチウムイオンをベースに、より安全性・軽量化・制御性を高めたモデルが主流になっています。中でも注目されるのは以下のような新技術・新製品です。
また、メーカー各社では「AGV向けバッテリー導入ガイド」「車種別対応表」「導入事例集」などの技術資料も整備されており、個別の選定時に大いに参考になります。
資料請求時には以下の情報を整理しておくと、適切な提案を受けやすくなります。
- 搬送重量/稼働時間/充電時間の目安
- AGVの型式・導入台数・制御インタフェース
- 既設の充電器仕様(有無)・設置スペースの制限
- 使用環境(温度・湿度・防爆など)
このような事前整理があることで、メーカー側もより実用的な提案が可能となり、開発・調達コストを抑えつつ、長期的な安定運用を実現できます。
AGVバッテリーのQ&A|選定・寿命・交換でよくある質問まとめ
- 24Vと48VのAGVバッテリー、選ぶ基準は何ですか?
基本的には「搬送重量」「走行距離」「走行速度」「勾配の有無」によって選定されます。24Vは軽量・短距離向け、48Vは中~大型AGVや傾斜走行、長距離搬送に適しています。
- 48Vにしたら電力消費も倍になりますか?
いいえ。電力は「電圧×電流」で決まるため、48Vにすると同じ出力でも電流を抑えられます。これにより、配線の発熱やエネルギーロスが減り、むしろ効率が向上する場合もあります。
- 同じ容量(Ah)でも稼働時間に差が出るのはなぜですか?
放電深度(DoD)、バッテリー内部抵抗、温度、負荷の安定性などが影響します。同じAhでも実効稼働時間は異なり、現場環境での評価が必要です。
- バッテリー寿命って、何年持てば「優秀」なんでしょうか?
通常は3~5年が目安ですが、リチウムイオンバッテリーで5〜7年持続するケースもあります。充電管理や温度管理を徹底すれば、寿命を延ばすことが可能です。
- AGVバッテリーって途中交換しづらいですか?運用止まってしまいますか?
最近のモデルでは、交換が容易なカートリッジ式やスライド式が普及しており、特別なスキルがなくても短時間で交換できます。計画的な予備バッテリー配置と動線設計が重要です。
- 同じAGVに24Vと48Vのバッテリーを並列接続して併用できますか?
できません。異なる電圧のバッテリーを接続すると、電位差によるショートや劣化、発火のリスクがあります。必ず同一電圧・同一型番・同一履歴のバッテリーを使用してください。
- バッテリーの内部温度分布って、寿命にそんなに関係あるのですか?
非常に関係します。セル間の温度差が10℃以上あると、劣化スピードが大きくなります。セルごとの温度管理と放熱設計は、寿命延長のために欠かせません。
- リチウムイオンと鉛蓄電池で「満充電の定義」って違うのですか?
違います。鉛は電圧で充電状態をある程度判断できますが、リチウムイオンは電流収束を基準に判断するため、BMSによる制御が不可欠です。見た目の電圧では正確に判断できません。
- 寿命判定ってSOCじゃなくてSOHで見るべきって本当ですか?
はい、正しい判断にはSOH(State of Health)を確認する必要があります。SOC(State of Charge)は現在の充電状態を示すだけで、劣化具合はSOHでしか分かりません。
- バッテリーのmm寸法、図面通りでも収まらないことありますか?
よくあります。図面上では収まっていても、コネクタの逃げやハーネスの曲げ半径、固定具の厚みなどで干渉が起きることがあります。数mm単位の設計マージンを取るのが安全です。
まとめ|AGVバッテリー導入の本質は24V・48Vの違いだけでは語れない
AGVの運用を支えるバッテリー選定は、単なる「電圧」や「容量」の問題ではなく、現場環境や業務内容、運用コストや将来の保守体制まで含めた、極めて戦略的な意思決定です。
本記事では、24Vと48Vという代表的な電圧帯を軸に、それぞれの特徴・用途・寿命・交換時期・設計観点・診断方法まで、導入検討時に押さえておくべき要素を多面的に解説しました。
特に注目すべきポイントは以下の通りです。
また、メーカーによるカスタマイズ対応や、使用環境に合わせた選定基準、交換・充電戦略の最適化事例も紹介し、「自社の場合はどう考えればよいか?」という視点で判断できる構成としました。
今後AGVの導入・拡張・リプレースを検討する際には、本記事で得た情報を元に、自社の搬送ニーズ・作業負荷・保守体制を見直し、より高効率かつトラブルの少ない運用を実現してください。
初めてのAGV導入で陥りがちなミスを、チェックリスト形式でまとめました。
現場や運用の状況に合わせたポイントを押さえることで、リスクを最小化できます。
後戻りできない導入前に、ぜひ一度ご覧ください。
→ AGV導入前チェックリストを無料で見る